Татьяна Астафьева
Lesen Sie den Artikel auf Deutsch
Интервью Дениса Александровича Иголки , технического директора REDPATH DEILMANN GmbH журналу “Глобус”
За этой технологией будущее шахтного строительства, отмечают специалисты. О нюансах и преимуществах метода рассказывает представитель компании Redpath Deilmann, осуществляющей такие работы
Проходка шахтных стволов — один из самых длительных и дорогостоящих этапов в строительстве горно-обогатительного комбината с подземным традиционным способом добычи руды. В зависимости от горно-геологических условий месторождений стоимость проходки и крепления таких устройств в среднем может составлять от 15 до 50 % от общего объёма требуемых инвестиций в такое предприятие.
Снизить затраты на данном этапе, сократить время проходки и крепления стволов, соответственно, ускорив ввод в эксплуатацию объекта, при этом повысив уровень безопасности конструкций для людей и региона присутствия, можно за счёт проходки шахт механизированным способом.
Такие работы по новой уникальной технологии впервые на евразийском континенте ведёт компания REDPATH DEILMANN GmbH, реализуя проект на территории Республики Беларусь. Подробнее об особенностях технологии, о данном объекте, а также о компании в целом рассказал Иголка Денис Александрович , технический директор REDPATH DEILMANN GmbH
Более чем вековая история и присутствие по всему миру
Для начала немного истории. В 2018 году компании исполнилось 130 лет. В 1921–1925 годах первой в СССР построила шахтный ствол методом замораживания пород — на Верхнекамском месторождении калийно-магниевых солей в Соликамске. Стоит отметить, что этот ствол работает до сих пор.
В 1960-х годах у компании было достаточно много проектов в реализации, и доходило до того, что организация одновременно вела строительство до 15 шахтных стволов в разных местах. В 2006-м появляется еще один проект в России — по возведению двух шахтных стволов для «Уралкалия».
В 2017 году, параллельно со строительством многих других объектов, которое ведут в разных странах мира, REDPATH DEILMANN GmbH начинает возведение двух шахтных стволов методом замораживания пород с использованием уникальных шахтопроходческих комплексов SBR для «Славкалия» в Беларуси. Такой проект реализуется впервые на территории не только Европы, но и всей Евразии.
На сегодняшний день Redpath Mining как шахтостроительный холдинг имеет представительства по всему миру, на всех континентах. REDPATH DEILMANN GmbH имеет дочерние предприятия в России, Беларуси и Сербии. Количество сотрудников, работающих на всех площадках компании Redpath Mining, насчитывает около 7 800 человек, общий годовой оборот (по примеру 2019 года) составляет 1,1 млрд канадских долларов.
Способ замораживания пород — принцип остается неизменным
При проходке шахтных стволов компания использует способ замораживания горных пород, который открыли ещё в конце 19-го века. Его суть в том, что через пробуренную скважину подаётся носитель, который замораживает вокруг себя породу, насыщенную влагой.
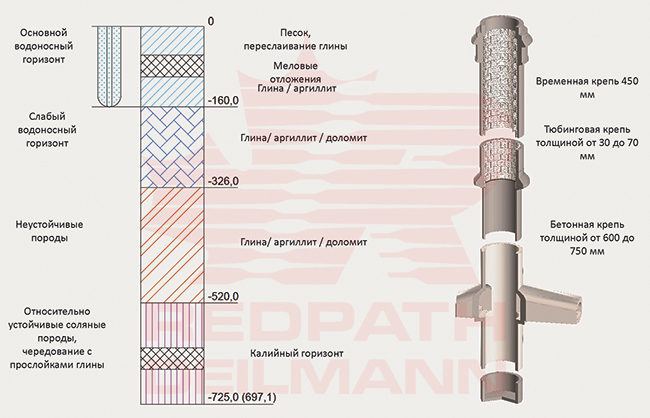
За годы с первого применения технологии, конечно, изменилось многое. Стали другими инструменты, которые теперь позволяют производить работы более точно, более эффективно и быстро формировать ограждение и контролировать его на протяжении всего срока проходки стволов. Появились новые технологии, благодаря которым можно безопасно изолировать крепь, что особенно важно в калийных рудниках, чтобы избежать негативных явлений, связанных с подтоплением. Конечно, появились и новые системы мониторинга, контроля, с их помощью и с учетом моделирования можно выполнить достаточно точный прогноз результата, оптоволоконные датчики, которые позволяют непрерывно контролировать температуру по всему телу ограждения. Безусловно, изменилась техника — замораживающие компрессоры, насосное оборудование и т. д.
— Естественно, за этот более чем вековой период произошел значительный технический прогресс. И наша компания обладает всеми техническими и технологическими новинками, появляющимися в мире, позволяющими выполнить работы по замораживанию пород любой сложности, — комментирует Денис Иголка.
Вместо буровзрывного — механизированный
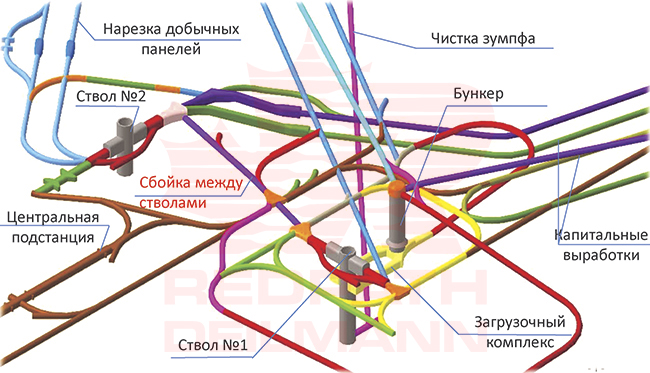
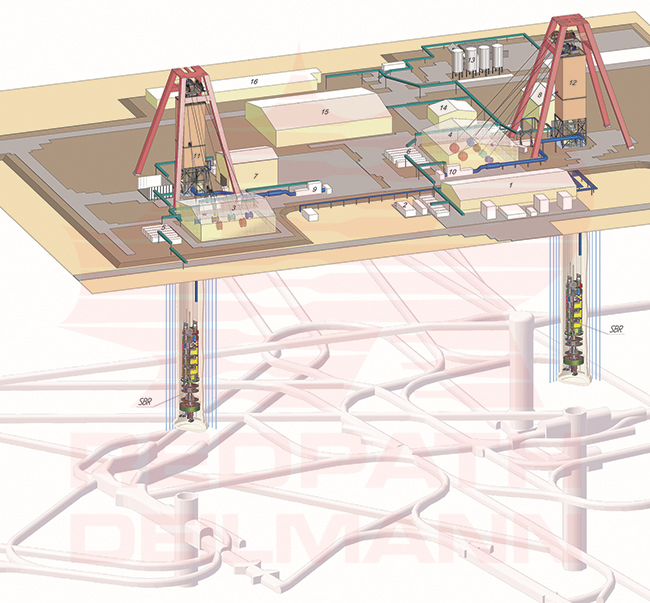
В 2017 году компания начала реализацию крупного и уникального проекта в Республике Беларусь.
Дело в том, что традиционно шахтные стволы проходят буровзрывным способом. И по всему миру его продолжают считать стандартом. Тем временем в Беларуси REDPATH DEILMANN GmbH применили особенную технологию механизированной проходки. Наряду с замораживанием шахтные стволы диаметром 8 м проходят с использованием проходческого комплекса SBR, произведённого компанией Herrenknecht. Как говорит Денис Иголка, применение данной технологии открыло новую веху в истории шахтного
строительства. Она используется всего лишь второй раз в мире и первый раз в Евразии. Впервые машины были применены в Канаде, но после этого инженеры компании Herrenknecht и REDPATH DEILMANN GmbH приложили максимум совместных усилий и значительно модернизировали комплекс, что позволило серьёзно увеличить темпы проходки.
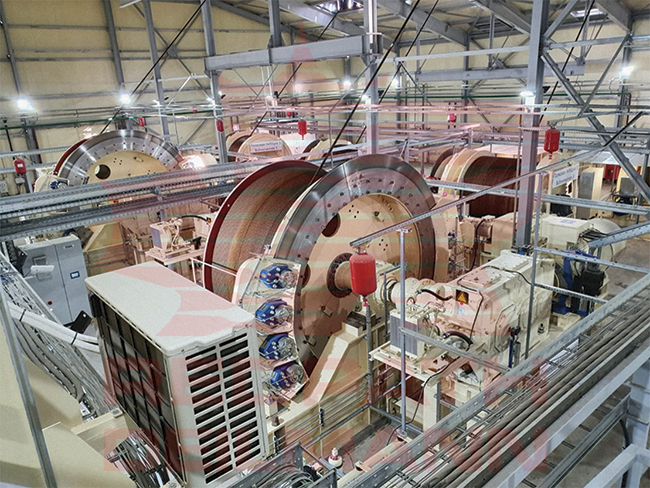
Так вот, за счёт увеличения темпа на этом проекте комплекс показал рекордные результаты. В феврале 2018-го здесь запустили замораживание пород, после чего традиционным способом выполнили собственными силами проходку двух технологических отходов глубиной 53 м, в начале 2019-го смонтировали и запустили проходческие машины, т. е. за год выполнили полное оснащение с доставкой двух 400-тонных SBR, для которых потребовался отдельный логистический проект. После этого всего за полтора года прошли ствол длиной в 700 м. На данном этапе в стволе № 1 специалисты дошли до отметки 715 м, до плана осталось всего 10 м. А на стволе № 2 машина SBR уже демонтирована и выдана «на-гора», а специалисты уже приступили к её консервации.
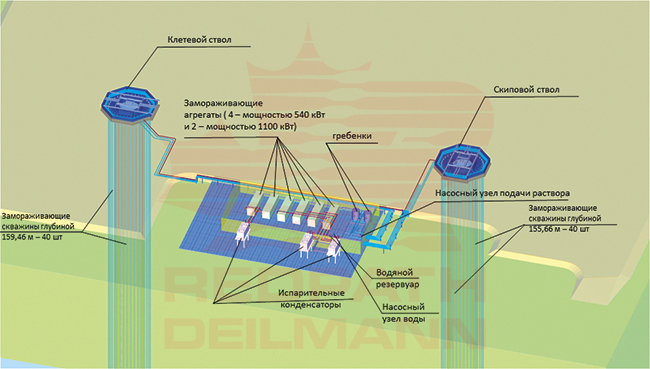
О темпах проходки в цифрах: в отдельные дни здесь достигали скорости проходки до 7,5 м в сутки. Максимальная производительность зафиксирована в апреле 2020 года на отметках глубже 500 м, где ровно за один месяц было пройдено и закреплено 144 м готового ствола. Для сравнения: при традиционном способе 40–60 м в месяц считается хорошим темпом.
— Впереди нам предстоят работы по армировке стволов, что считается достаточно несложным, но очень ответственным этапом для работы будущего шахтного подъёма. После этого мы по контракту обязаны выполнить определённый объем горно-капитальных работ и пройти подземные горные выработки околоствольного двора в объёме 90 тыс. куб. м общей протяжённостью около 10 км. Также на глубине 700 м необходимо построить подземный загрузочный комплекс грузового ствола № 1 с подземным бункером накопителем высотой около 40 м и диаметром «в свету» 8 м. Это делается для того, чтобы ввести в эксплуатацию первую очередь рудника, что называется, вдохнуть в него жизнь. В данный момент ведём активную фазу подготовки к проведению данных горно-капитальных работ и планируем, что уже летом 2022 года мы выполним все свои контрактные обязательства перед заказчиком, — комментирует технический директор проекта.
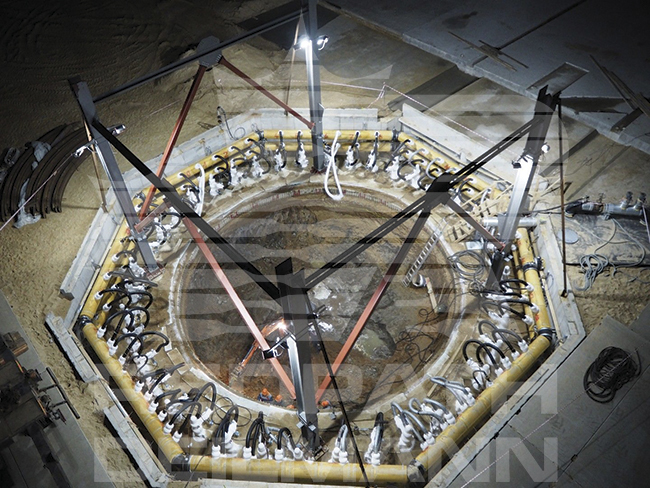
Надо сказать, что работам по большому счету не помешала даже пандемия. Хотя опасения насчет того, что эпидемиологическая ситуация скажется на темпах, все же были. Тем не менее из ситуации удалось выйти достаточно лаконично, и в апреле-мае, когда в Европе наблюдался пик подъема заболеваемости, на площадках компании ставили рекорды по скорости проходки шахтных стволов с учетом максимально возможных мер предосторожности.
Преимущества технологии механизированной проходки шахтных стволов
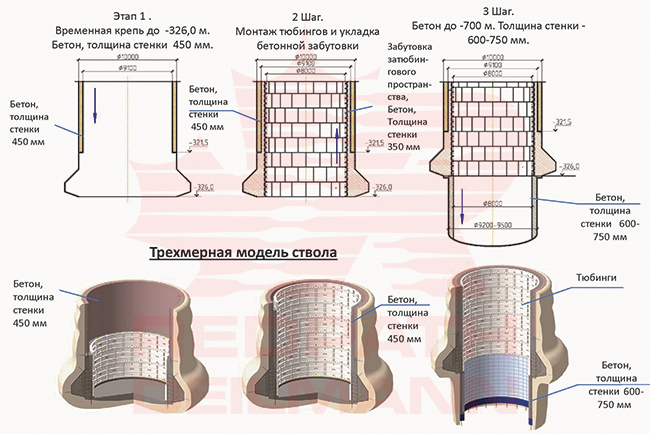
• Высокие темпы работы. Как уже было отмечено выше, машина способна проходить по номинальным параметрам 5 м готового ствола в сутки. Аналогов по скорости в мире на сегодняшний день нет.
• Экономика. И этот фактор является решающим. Проходка шахтных стволов — самый долго-строящийся и дорогостоящий этап, который лежит на критическом пути ввода в эксплуатацию того или иного комбината. Соответственно, быстрые темпы проходки шахтных стволов при нужной подготовке на поверхности — строительстве надземного комплекса — позволяют выходить на рынок окончательной продукции намного быстрее. А более ранний ввод в эксплуатацию предприятия, соответственно, позволяет экономить колоссальные суммы за счет снижения стоимости заемных средств, ускорения сроков окупаемости инвестиций и более раннего выхода на рынок готовой продукции.
• Безопасность. Технология механизированной проходки позволяет эксплуатировать проходческий механизм без людей в забое — машина управляется оператором дистанционно из помещения с необходимой шумоизоляцией. Соответственно, риск для сотрудников, связанный с обрушениями и другими подобными ЧП, случающимися во время такой деятельности, полностью исключается. Да и отсутствие горновзрывных работ, которые всегда сопряжены с определенной степенью риска, уже является определенного рода обеспечением безопасности. Также механизированный способ позволяет закрепить выработку так, чтобы была гарантия безо-пасной дальнейшей эксплуатации.
• Экологическая безопасность. Надо сказать, этому тоже в компании также уделяется должное внимание, и при производстве данных работ в том числе. Механизированная проходка снижает загрязнение атмосферы: нет пылевой и вибрационной нагрузки, как при буровзрывных работах, а ликвидировать и утилизировать взрывчатые вещества после отработки не нужно.
— За этой технологией будущее. И в ближайшей перспективе мы будем видеть все больший и больший переход на механизированный способ проходки шахт и отказ от традиционного буро-взрывного метода. Конечно, каждый проект индивидуален, и многое зависит, скажем, от прочности, устойчивости пород, глубины залегания залежи, гидрогеологических условий и многих других факторов. Но и мы работаем с каждым из наших заказчиков эксклюзивно. И проходческие машины совершенствуем и адаптируем под конкретные параметры, с последующим тюнингом уже на объекте, а также постоянно проводим разработки и испытания, для того чтобы применять новые эффективные технологии в различных, даже самых сложных условиях, — говорит Денис Александрович.
Каждый новый объект — это челлендж, требующий дополнительных решений
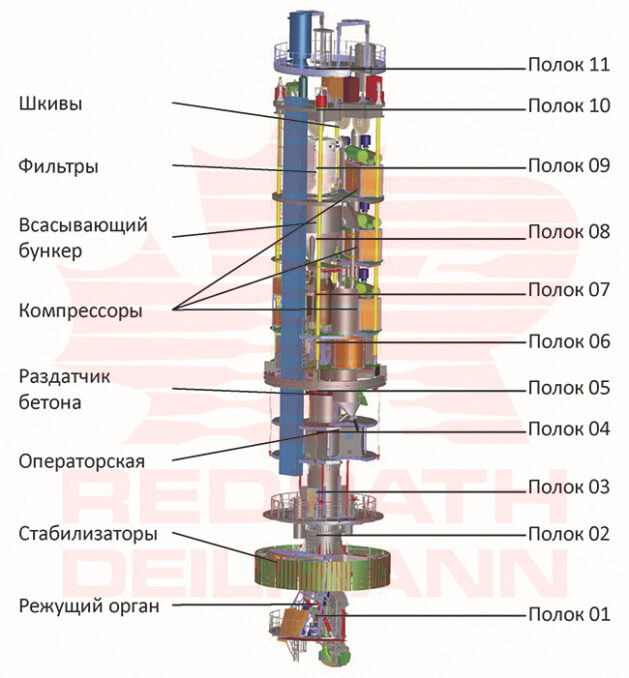
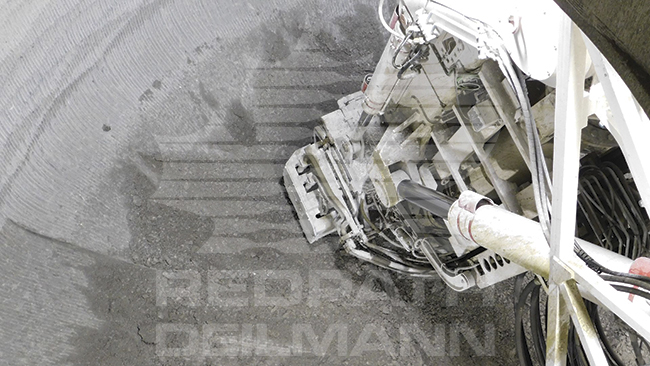
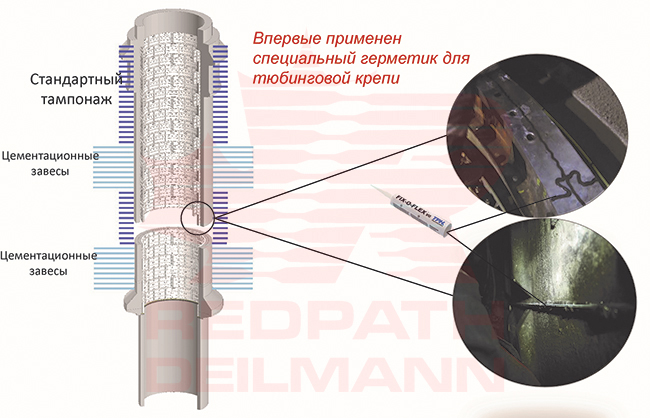
Надо сказать, что при применении SBR в рамках белорусского проекта возникали и сложности, решение которых специалистами REDPATH DEILMANN GmbH хотелось бы особо отметить.
В частности, когда осуществляли проходку по породам невысокой прочности, ниже уровня замораживания, в силу высокого отставания крепи от забоя наблюдались обрушения породных стенок в забойной камере ниже рабочих полков. Из-за этого были трудности с возведением крепи на определенном интервале. В связи с чем на 3–4 недели пришлось приостановить проходку на одном из стволов и буквально на ходу выполнять модернизацию и адаптацию комплекса, чтобы стабилизировать породную стенку. Таким образом, ведение бетонных работ за счет переноса опалубки ближе к забою обеспечило продолжение проходки шахтных стволов теми же высокими темпами.
Но и это ещё не все
— Конечно, и механизм, и его инфраструктура на первоначальном этапе потребовали определённого вмешательства и модернизации в соответствии с реальными условиями забоя, в которых нужно было работать. Так, основная технология связана с тем, что породы, разрушаемые режущим органом, всасываются мощными компрессорами на высоту около 24 м по трубному ставу со скоростью потока более 100 км/ч, потом перегружаются в бадью и поднимаются на поверхность. Трубный став в таких условиях претерпевал очень большой износ, что было ожидаемо, однако особенные сложности составили участки при подъёме песчаных замороженных пород.
Это потребовало дополнительных оперативных экспертиз и технических решений по замене части трубопровода с иным материалом и нанесению специальных покрытий на данные элементы системы. Также появлялись породы, которые трудно поддавались всасыванию, и транспортировка тоже оказалась небольшим челленджем из-за налипания пород на режущий орган и систему всасывания. Чтобы его преодолеть, всасывающий став и приёмный бункер-циклон оснастили дополнительными инъекционными установками, которые позволяли промывать с применением дополнительных присадок всю транспортную систему, чтобы она работала без сбоев, — комментирует Денис Иголка.
И проходка сопряжений шахтных стволов была связана, так скажем, с вынужденным использованием инноваций. Специалисты компании впервые при шахтном строительстве возвели сопряжение стволов, да и весь ствол полностью механизированным способом без применения даже грамма взрывчатки.
— Мы спустили и смонтировали комбайн избирательного действия прямо в шахтном стволе под стволопроходческой машиной и осуществили проходку сопряжения также комбайновым способом. Проходил процесс достаточно эффективно, и затраченные усилия на данную технологию полностью себя оправдали. Процесс осуществили абсолютно безопасно, без перерубки породы и перерасхода материала, а также обеспечили дополнительную устойчивость данного сопряжения за счёт снижения искусственной трещиноватости пород при буро-взрывном способе, — комментирует Иголка.
Здесь хотелось бы сделать небольшую ремарку: данное решение было своего рода планом В. Его приберегали на случай невозможности поставки взрывчатых материалов. Поставки сорвались из-за пандемии, а план В сработал.
Если ещё говорить об инновациях, то стоит отметить, как на данном проекте возвели тюбинговую колонну. Само по себе это не является чем-то новым. Но здесь использовали специальные герметики, которые разработали для применения в вертикальных шахтных стволах. Это позволило обеспечить полную водонепроницаемость тюбинговой колонны без особых дополнительных трудозатратных мер.
Гарантия результата
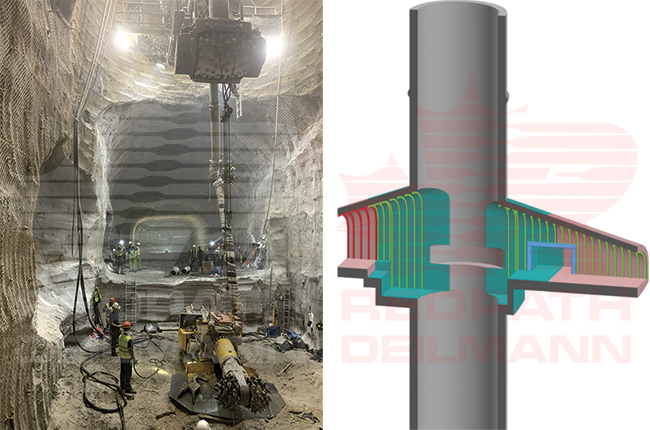
Redpath Deilmann как компания, занимающаяся проходкой стволов и всем, что с этим связано, гарантирует качественный результат своей работы. И заказчика никогда не оставляют и не оставят с какой-то возникшей проблемой один на один.
— Мы всегда готовы вернуться и помочь с тем, что уже введено в эксплуатацию. Более того, если говорить о машинах, механизмах, кадрах при вводе рудников в эксплуатацию, мы на первых этапах развития проекта можем помочь и обеспечивать введение в эксплуатацию шахтного подъёма, вести эксплуатацию и наблюдение за оборудованием и т. д. Для этого у нас, конечно же, есть специально обученный персонал, начиная от операторов подъёмных машин и заканчивая квалифицированными электромеханиками, которые всегда ведут оборудование по тем требованиям, которые предъявляют поставщики в соответствии с современными стандартами, — отмечает Денис Александрович.
Слаженная команда и люди — это гордость
Совместная работа специалистов Redpath Deilman, Herrenknecht и служб заказчика в лице «Славкалия» даёт хороший результат при проходке стволов в Беларуси, так как команды сформированы из профессионалов, знающих своё дело, в том числе умеющих наладить командную работу и эффективные коммуникации.
Кадровая политика компании — тема отдельная. Здесь не скрывают: работающие во всех представительствах люди — это корпоративная гордость. Реализуя какой-то проект, компания не просто выполняет договорные обязательства перед заказчиком, но и частично обеспечивает рабочими местами территорию присутствия. В том числе обучая местных специалистов, если это необходимо. А если человек хорошо зарекомендовал себя на каком-либо проекте, его вполне могут приглашать и на другие объекты.
Взять тот же проект, который реализуется сейчас на территории Республики Беларусь. Здесь, на этой площадке, постоянно работают порядка 400 человек. Около 50 человек — немецкие специалисты и проходчики. Ещё около 40 человек — сотрудники, с которыми компания знакома давно: приглашённые с других объектов, выполняемых фирмой. Остальные 310 человек — местные жители, которых обучили до необходимого уровня для работы на современном оборудовании с использованием технологии SBR. При этом стоит отметить, что многие уже обладали достаточно хорошими навыками, а та часть людей, которая поступила к нам на обучение, продемонстрировала отличный результат, в особенности операторы SBR и подъёмных машин.
— По обучению специалистов проделана огромная работа нашим инженерным составом из Германии. И те люди, которые смогли здесь многому научиться, они, бесспорно, получили не только новые профессии, но и уникальный опыт работы. Они всегда могут остаться на предприятии, которое заработает после окончания нашего проекта и запуска комбината, а также могут остаться с нами для реализации наших следующих объектов в других территориях по всему миру, — говорит технический директор проекта.
При этом на площадке в коллективе абсолютно дружественная атмосфера и очень хорошие взаимоотношения между сотрудниками. В этом, конечно же, есть заслуга руководителей, находящихся на объекте, но все-таки сами люди играют здесь ключевую роль.
Тут же стоит особо отметить роль заказчика в лице руководства компании «Славкалий» и сотрудников, участвующих в строительстве рудника, благодаря которым выстроены хорошие коммуникации между специалистами на разных уровнях, включая работу с проектными компаниями и надзорно-контролирующими органами.
С соблюдением всех местных требований — обязательно!
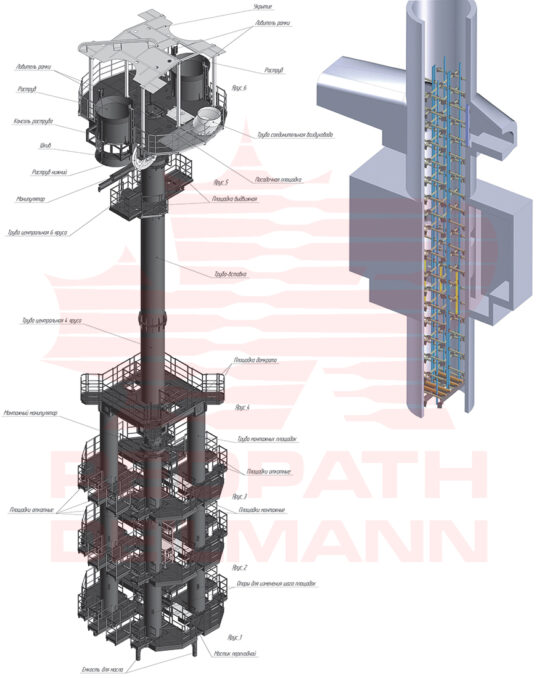
Многие подрядчики, работающие на рынке шахтного строительства, часто сталкиваются с бюрократией и с некорректными, на их взгляд, требованиями местных технических стандартов, где приходится осуществлять деятельность. В данной ситуации важно отметить, что в этом конкретном случае это относится именно к шахтному строительству, так как технический прогресс в данной области опережает содержание ряда строительных норм в области проходки стволов и подземных выработок.
С исполнением стандартов иногда возникают сложности, конечно, серьёзно мешающие основной работе и приёмке результатов работ.
Когда Redpath Deilmann заходит на очередной объект, её сотрудники с максимальным вниманием относятся к соблюдению норм и требований (безопасности, экологическим и прочим) региона и страны, где нужно будет работать в ближайшие годы.
Да, в компании имеются собственные корпоративные требования. И зачастую они даже строже, чем нормы, которые предъявляют к таким видам производств в некоторых странах. Но подходы могут отличаться.
— Мы к этому относимся очень трепетно. И соотнесение с местными нормами, полное их безукоризненное исполнение — один из принципов компании. На каждом объекте мы практически с нуля выстраиваем полную систему управления, связанную с получением всех необходимых допусков и разрешений, сертификатов, лицензий по части ведения, безопасности работ и т. д. При этом при возникновении сложностей, связанных с отклонением от действующих норм, можно всегда обратиться в соответствующие надзорные органы за дополнительными разъяснениями и в случае необходимости организовать совместные дополнительные экспертизы для новых технических решений с целью их последующего согласования. В том числе и поэтому с приёмкой работ на объектах надзорными органами не возникает особых проблем, — комментирует Денис Александрович.
Отвечать на современные вызовы
Компания ни дня не стоит на месте, постоянно занимаясь новыми разработками и поиском новых вариантов сотрудничества.
— Как правило, если говорить чисто технически, мы постоянно движемся как минимум в двух направлениях в работе по нашему развитию. Мы постоянно совершенствуем способы ведения работ с применением новых технологий и постоянно работаем над совершенствованием конструкций материалов крепления стволов и выработок. Мы чётко представляем, какие в современных условиях предъявляются требования к конструкциям крепи и способам их возведения. Большой объем работ проделывается в части модернизации конструкций крепи стволов, по полной их водонепроницаемости — это очень важно для многих рудников, в особенности для соляных и калийных. Плотно работаем над развитием технологий по возведению сталебетонных композитных крепей со специальными заполнителями, закладками и т. д. Есть надежда на то, что такие проекты мы в ближайшее время реализуем и в Российской Федерации. И, конечно, в части технологии проходки мы смотрим с перспективой на рынок механизированного способа. Поэтому сейчас, например, разрабатывается принципиально новая технология, она будет называться машиной нового поколения механизированной проходки по крепким и очень крепким породам. С её помощью можно будет реализовать механизированную проходку высокими темпами по породам высокой прочности. Думаю, что о результатах этих разработок и испытаний будет более подробно сообщено в ближайшее время, — резюмирует Иголка.
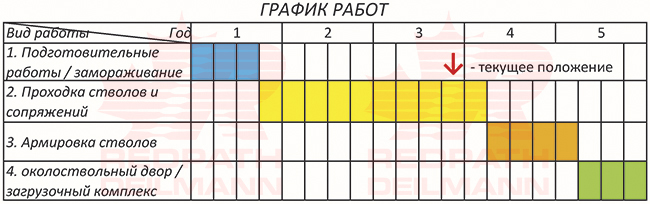
В части традиционных способов проходки специалисты компании также реализуют различные инновационные идеи для улучшения данной технологии. Ведь тех запасов, которые залегали, что называется, в комфортных условиях, становится все меньше. И у недропользователей возникают более сложные вызовы, появляется необходимость проходки шахт на больших глубинах, в сложных геологических условиях и т. д. Понимая эти вызовы, в компании занимаются новыми разработками, чтобы решать задачи заказчиков как можно более эффективно.
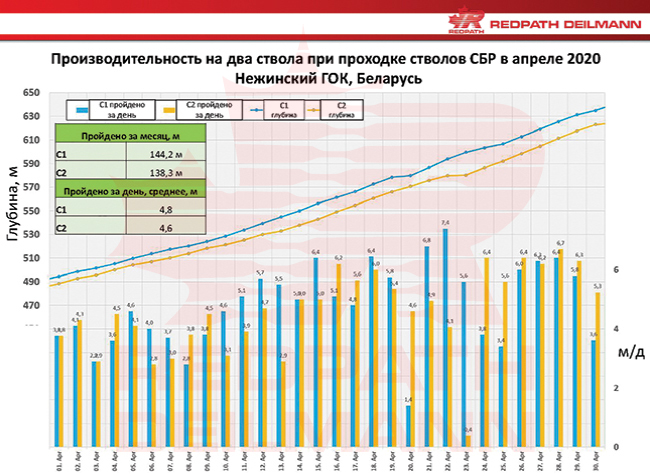
Haustenbecke 1 44319
Dortmund/Germany
Tel +49 231 2891 396
infogermany@redpathmining.com
Хаустенбеке 1 44319
Дортмунд/Германия
Teл: +49 231 2891 396
infogermany@redpathmining.com