Dr. Felix Heinicke (соответствующий автор), Köppern Aufbereitungstechnik GmbH & Co. KG, Agricolastr. 24, 09599 Freiberg, contact@koeppern.com / russia@koeppern.com
Dr. Harald Günter, Köppern Aufbereitungstechnik GmbH & Co. KG, Agricolastr. 24, 09599 Freiberg
Prof. Dr. Holger Lieberwirth, Institute for Mineral Processing Machines, Lampadiusstr. 4, 09599 Freiberg
В последние годы во всем мире наметилась тенденция к использованию валковых прессов высокого давления (ВПВД) для измельчения [1]. Эта практика измельчения стала известна в 1980-х годах благодаря исследованиям немецкого профессора Шенерта. Хотя технология имеет гораздо более глубокие корни [2]. Компания Köppern, как один из производителей ВПВД, уже более 120 лет работает над валковыми прессами, начиная с прессов для производства угольных брикетов. Впоследствии появились другие области применения, например для грануляции удобрений. Первые решения по применению ВПВД для измельчения были использованы в цементной промышленности, где ввиду стоимости продукта экономия энергии была приоритетом.
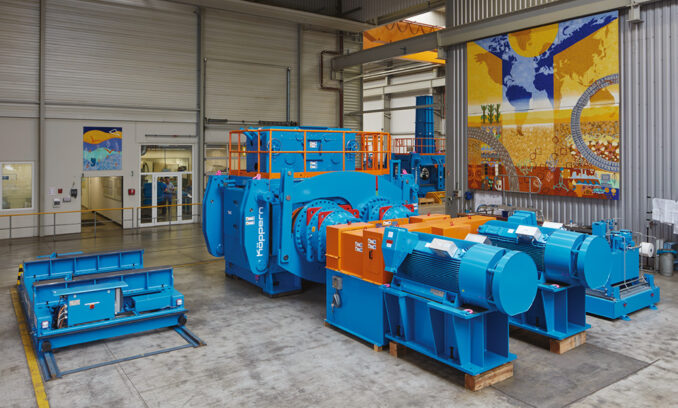
Тем не менее было трудно перенести этот принцип измельчения на применение в минеральном сырье из-за гораздо большего износа, вызванного абразивностью материала. Первое применение началось в измельчении железорудного концентрата. Были оптимизированы поверхности валков и созданы ВПВД для твердых пород. Предпочтительной системой поверхности валков для руды является система штыревой футеровки, которая широко используется в настоящее время.
Валковые прессы высокого давления выпускаются в широком диапазоне типоразмеров. В зависимости от требуемой производительности установки и чтобы предсказать эксплуатационные параметры машины для определенного материала, необходимо провести испытания на измельчение. Наиболее важными параметрами являются удельная пропускная способность и удельный расход энергии, что позволяет подобрать типоразмер ВПВД для требуемой тонкости и дальнейшей переработки продукта, такой как флотация, магнитная сепарация или окомкование, и зависит от характеристик руды. В зависимости от сложности получаемой технологической схемы (однопроходная, многопроходная или с возвратом краевого продукта) испытания на ВПВД требуют наличия материала в необходимом количестве. Количество тестового материала может быть уменьшено с применением имитационных моделей.
После установки ВПВД в реальных условиях технологическая схема и размеры фиксированы, но требуется оптимизация процесса, поскольку рудное тело месторождения обычно меняется в течение срока эксплуатации. Опять же имитационные модели могут быть использованы для прогнозирования работы технологической схемы и сокращения времени на практические шаги по улучшению процесса.
Определение типоразмера
На рисунке 1 показан современный валковый пресс высокого давления производства Köppern. Так как условия работы пресса всегда индивидуальны в отношении производительности, энергии и тонкости продукта, используется набор стандартизированных масштабных значений. Эти значения очень зависят от свойств руды. Поэтому лабораторные испытания проводятся на предприятиях поставщиков. Расчеты значений с использованием результатов таких испытаний приведены ниже.
Удельная пропускная способность
Удельная пропускная способность mdot в единицах (t∙s)/(h∙m³) определяется как:
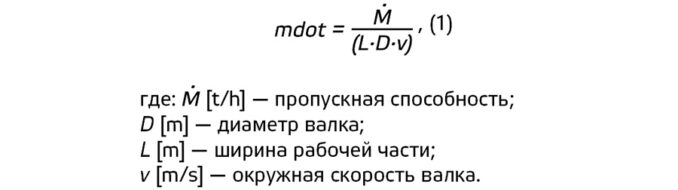
, (1)
Удельная производительность характеризует пропускную способность ВПВД при заданном удельном усилии прессования, исходном материале и типе поверхности валков. Это нормированное значение дает производительность машины с диаметром валков 1 м и шириной валков 1 м при окружной скорости 1 м/с. Коэффициенты масштабирования затем используются для определения размеров машин от лабораторного до промышленного масштаба.
Удельное энергопотребление
Удельное энергопотребление ESp, net, в единицах кВт∙ч/т, является показателем, рассчитанным по норме массы и характеризующим количество энергии, переданной материалу за один проход прессования.
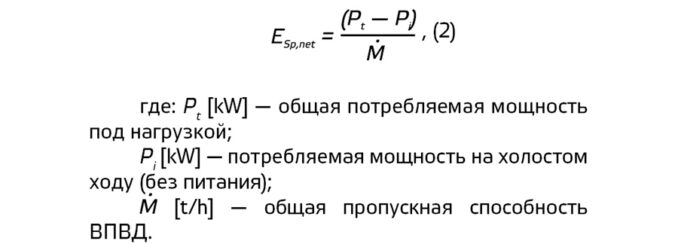
, (2)
Удельное энергопотребление используется для определения типоразмеров привода для машин промышленного типа. Он также является параметром, определяющим необходимое количество энергии, передаваемой материалу для достижения определенного результата измельчения. Удельное энергопотребление обычно хорошо коррелирует с удельным усилием прессования. На рисунке 2 показан один пример из серии испытаний с гранодиоритом.
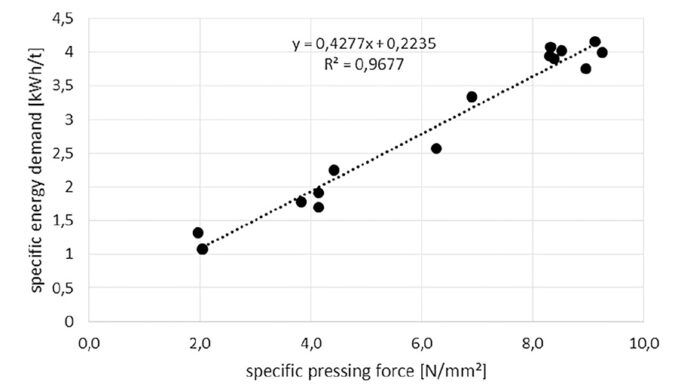
Тонкость помола
Существует множество вариантов определения крупности сырья и продукта. Согласно теории Бонда [3], для описания гранулометрического состава с одной-единственной точкой отсчета можно использовать показатель P80 (80 % массы продукта, прошедшего определенный размер сита). Это значение может быть получено с помощью мокрого [5] или сухого ситового анализа [6] для обычных процессов переработки руд гранулометрическим составом до 80 мм. Для более тонких помолов измельчения < 0,300 мм было установлено использование лазерного дифрактометра [4], но также используются интегральные значения, такие как измерение удельной поверхности по методу Блейна [7].
Важно отметить, что гранулометрический состав продуктов ВПВД отличается от продукта, измельченного в шаровой мельнице. Гранулометрический состав не только смещается вдоль горизонтальной оси диаграммы распределения размеров, но и искривляется в сторону увеличения количества мелких частиц. На рисунке 3 представлены два примера измельчения гранодиорита с помощью ВПВД в верхнем диапазоне размеров 22 мм и 2 мм.
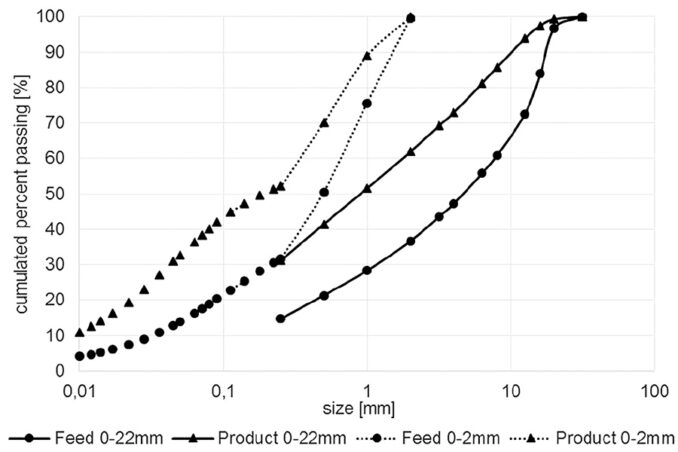
Таблица потоков
В последние десятилетия были опубликованы различные работы, касающиеся нескольких вариантов технологической схемы с использованием ВПВД [примеры 8–12]. В данной статье подробно рассматриваются следующие варианты технологических схем:
В один проход
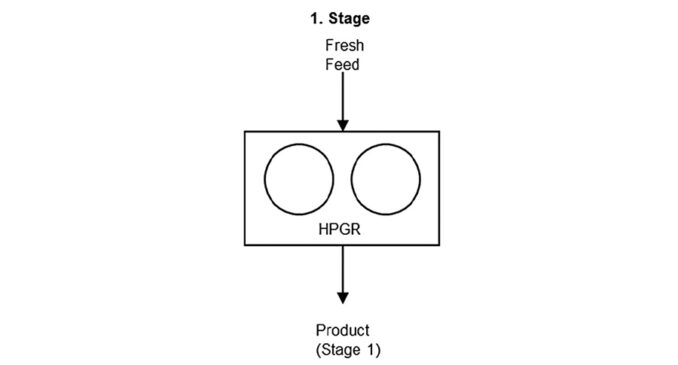
Схема «в один проход» является наиболее простой с использованием ВПВД. Материал подается в пресс сверху, сжимается и измельчается в машине. Затем поступает непосредственно на последующие процессы, такие как шаровое измельчение, в случае если ВПВД применяется для предварительного измельчения, или окомкование, если ВПВД применяется для доизмельчения концентрата и получения железорудных окатышей.
При измельчении «в один проход» валковый пресс высокого давления может влиять на тонкость продукта путем изменения усилия прессования. На рисунке 5 показано влияние удельного усилия прессования на тонкость продукта.
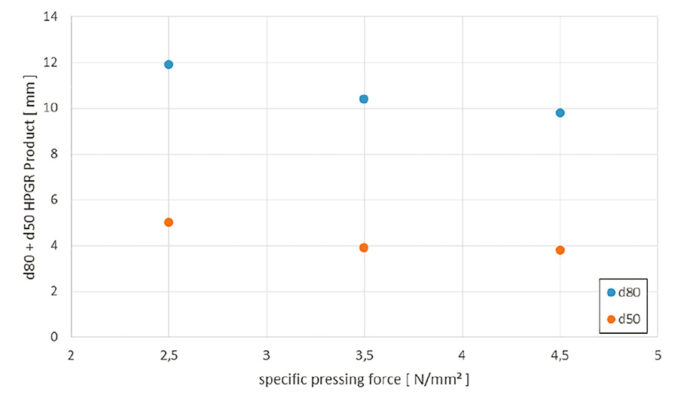
Для определения влияния удельного усилия прессования на тонкость продукта требуется 600–800 кг материала.
Последовательное измельчение
Если, например, для материала, согласно рисунку 5, требуется D50 2 мм, то влияние удельного усилия прессования на тонкость слишком мало для достижения этой требуемой тонкости продукта. Более высокие усилия технически возможны, но это сильно увеличит OPEX машины. В технологической схеме возможно последовательное включение нескольких машин (рис. 6). Таким образом, наибольшее влияние на тонкость будет наблюдаться между первым и вторым последовательно установленными прессами (рис. 7).
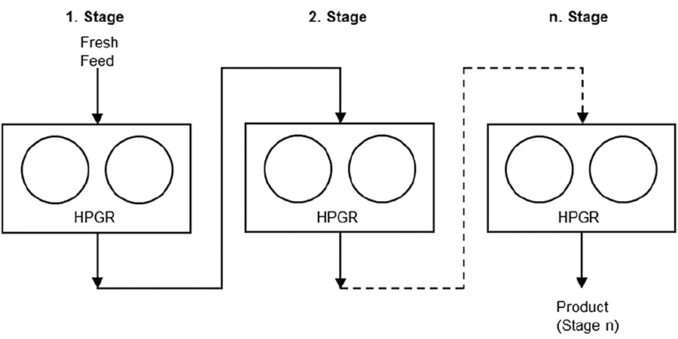
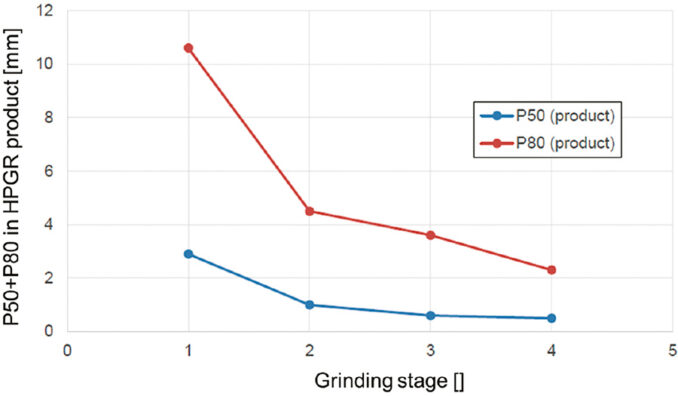
Необходимое количество материала для показанного выше поэтапного измельчения составляет около 250 кг, поскольку продукт может быть использован в качестве нового сырья для следующего этапа измельчения, при этом исключается количество образцов.
Рециркуляция краевого продукта
Поскольку установка нескольких машин для варианта многократного прохода приводит к более высоким CAPEX, также устанавливается система рециркуляции краевого продукта (рис. 8). Таким образом, часть материала перерабатывается и подается на тот же ВПВД вместе с питанием. Таким образом, увеличивается тонкость подачи материала в пресс и, следовательно, получается более тонкий продукт. Поскольку общая пропускная способность систем измельчения остается одинаковой, размер HPGR должен быть увеличен, чтобы он мог переработать как свежий материал, так и рецикл.
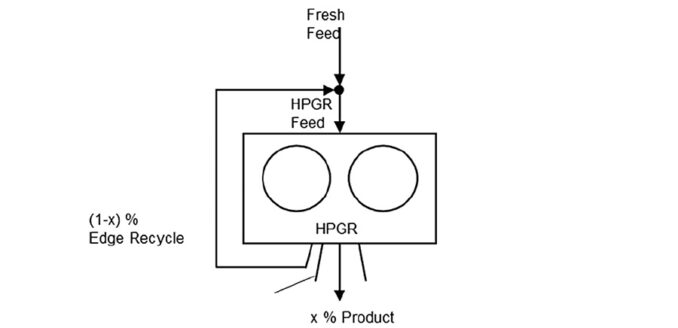
Тонкость измельчения вдоль продольной оси валков имеет определенный градиент в соответствии с рисунком 9. Причины этого связаны с физическим сжатием материала в центральной зоне валков и ограниченной возможностью подачи материала на край валков [13]. Поэтому целесообразно перерабатывать более грубый краевой продукт, так как в центре будет содержаться наибольшее количество тонкого материала. Этот эффект выше для узких валков, чем для широких.
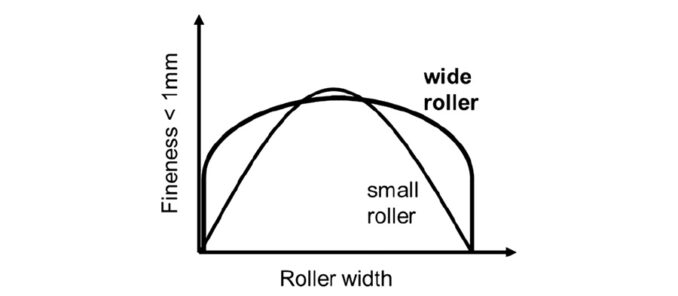
Количество тестового материала для такой серии испытаний составляет около 1 000 кг, так как необходима определенная стабилизация связанной серии испытаний на периодичность и смешивание. Это значительное количество для месторождений стадии разведки, где материал является керном бурения. Одной из целей подхода, основанного на моделировании, является сокращение вышеупомянутых объемов испытаний.
Моделирование и результаты
Результат тонкости рециркуляции краевого продукта располагается вдоль ряда многократного измельчения. Например, типичный результат с возвратом краевого продукта, полученный в промышленности для материала, согласно рисунку 7, будет иметь P50 около 2 мм, что находится между первой и второй ступенью измельчения. Поскольку серия испытаний с использованием нескольких ВПВД не потребляет много материала, она должна использоваться для прогнозирования производительности, удельной энергии и тонкости продукта для массового испытания на рециркуляцию краев. Основная идея заключается в том, чтобы определить, какой объемный процент сырья проходит через зону измельчения во время краевого рецикла (рис. 10 для 50-процентного разделения).
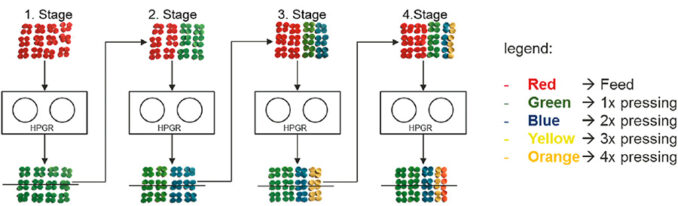
При разделении краевого продукта на 50 % объема после второй стадии будут следующими:
50 % — измельчен в один раз,
50 % — измельчен в два раза,
тогда как 50 % обеих фракций будут извлечены в качестве продукта, а остальное будет переработано. Модель основана на предположении, что при объединении свежего материала и рецикла образуется идеальная смесь. Это приводит к одинаковой статистической вероятности того, что каждая частица может упасть вдоль всей продольной оси валков независимо от прежнего количества циклов.
После четвертого этапа это будет выглядеть следующим образом:
50 % — измельчен в один раз,
25 % — измельчен в два раза,
12,5 % — измельчен в три раза,
12,5 % — измельчен в четыре раза.
Это приводит для всех значений соотношения «центр/край» (количество массы/объем, подлежащий переработке) к следующему математическому ряду:
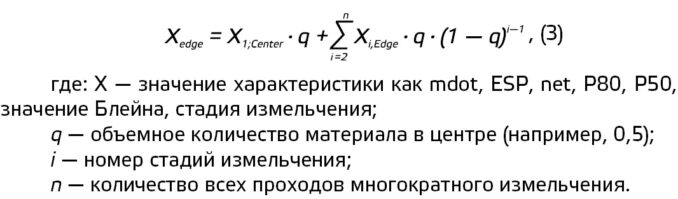
, (3)
Определение шагов измельчения (количество теоретических проходов через машину) затем рассчитывается для 60/40 % разделения «центр/край» следующим образом:

, (4)
В результате практических ограничений во время проведения испытаний прогрессивные шаги измельчения были прерваны после четырех. Таким образом, математический баланс был закрыт на 100 % после четвертого этапа. В следующей таблице показано результирующее влияние на этапы измельчения (табл. 1).
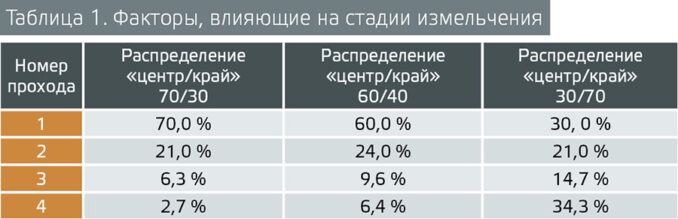
Теоретический расчет прохода измельчения в соответствии с формулой (4) для соотношения «центр/кромка» сводится к следующему:
70/30 — число проходов 1,4;
60/40 — число проходов 1,6;
30/70 — число проходов 2,5.
На рисунке 11 показаны результаты последовательного измельчения гранодиорита и значения тонкости на рассчитанных шагах измельчения. Ряды многократного помола показывают очень хорошую корреляцию с квадратичными формулами в рассматриваемом диапазоне. Эти формулы были использованы для интерполяции и прогнозирования тонкости для переработки краевого продукта. В таблице 2 показаны результаты измеренных и рассчитанных значений для нескольких соотношений «центр/край», а также различной тонкости подаваемого материала.
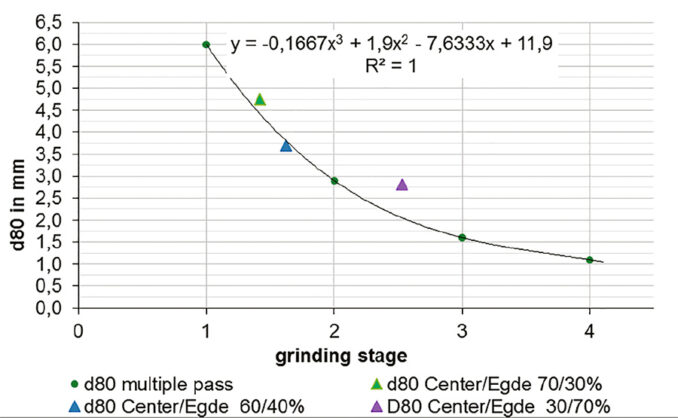
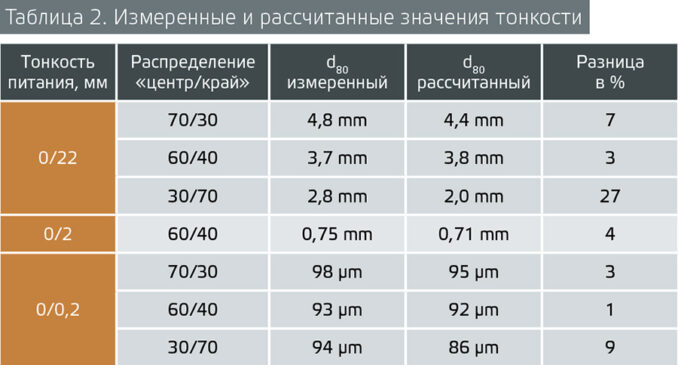
В таблице 3 и таблице 4 приведены результаты для удельной пропускной способности и удельной энергии.
Модель прогнозирует рабочие характеристики удельной пропускной способности, тонкости и удельной энергии в хорошем диапазоне для большого количества материала в центре, но вводит в заблуждение, если количество краевого продукта очень велико (например, 27 % разница при разделении 30/70 %). Одной из причин может быть то, что предполагаемое идеальное смешивание питания и продукта не обеспечивается при таком высоком соотношении. Необходимо провести дальнейшие исследования на эту тему.
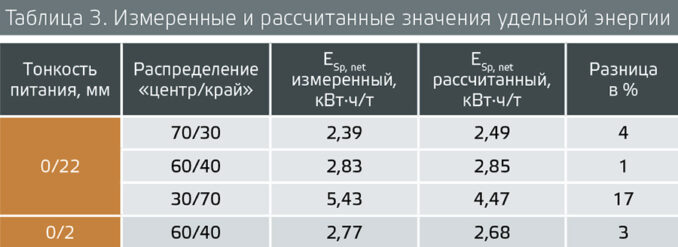
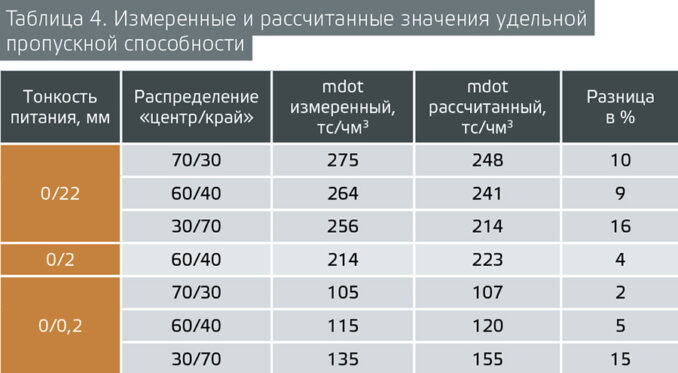
Прогноз тонкости продукта является более точным, чем удельная производительность и удельная энергия. Тем не менее следует отметить, что неточность больше 10 % может легко привести к увеличению типоразмера машины во время предварительного подбора. Поэтому данный метод экономии тестового материала может быть использован только на стадии предварительного обоснования и в дальнейшем должен быть подтвержден реальными испытаниями по переработке краевого продукта.
После определения типоразмера машины выбирается определенное соотношение «центр/край» и механически регулируется. После измерения изменения тонкости можно сделать прогноз для других результатов краевого продукта до того, как будут проведены трудоемкие работы по перенастройке. Кроме того, модель предлагает новую интересную возможность проверки данных на точность, поскольку она обеспечивает независимый результат тонкости от измеренного значения рециркуляции краевого продукта.
Выводы
В данной статье рассматривается работа по моделированию валкового пресса высокого давления для прогнозирования производительности, затрат удельной энергии и получаемой тонкости продукта для схем рециклинга краевого продукта. После определения необходимых параметров модель может оценить тонкость продукта, схемы рециклинга краевого продукта в приемлемом диапазоне, используя в качестве основы результаты многократных проходов. Удельная производительность и удельная энергия менее точны. Из-за отсутствия стопроцентной точности модель все еще нуждается в контроле инженера при использовании ее для определения типоразмеров машины. Однако это не противоречит основной функциональности данной модели.
Благодарность
Эта статья подводит итог работы над магистерской диссертацией Себастьяна Преусса в Техническом университете Bergakademie Freiberg [14]. Эта работа финансировалась компанией Köppern. Авторы хотели бы поблагодарить Себастьяна Преусса за огромный объем практической работы и хороший теоретический вклад, а также компанию Köppern за право публикации данной статьи.
Список литературы:
[1] Klymowsky, R. u.a.: Selection and sizing of High Pressure Grinding Rolls. SME Handbook 2002, S. 1–40.
[2] Schönert, K.: Einzelkorn-Druckzerkleinerung und Zerkleinerungskinetik. Untersuchungen an Kalkstein-, Quarz-, und Zementklinkerkörnern des Größenbereiches 0,1–0,3 mm. Dissertation. TH Karlsruhe, 1966.
[3] Bond, F. C.: The third theory of comminution. Mining engineering (1952), S. 484–494.
[4] n.N.: Particle size analysis — laser diffraction methods. ISO 13320, 2009.
[5] n.N.: Prüfverfahren für Gesteinskörnungen — Bestimmung der Korngrößenverteilung durch Nasssiebung. DIN 52098, 2005.
[6] n.N.: Siebanalyse. DIN 66165, 1987.
[7] n.N.: Bestimmung der spezifischen Oberfläche disperser Feststoffe mit Durchströmungsverfahren. DIN 66126, 1989.
[8] Gruendken, A. u.a.: Flowsheet considerations for optimal use of high pressure grinding rolls. Proceedings of Comminution08 in Falmouth (2008), S. 1–37.
[9] Schönert, K.: A first survey of grinding with high-compression roller mills. International Journal of Mineral Processing 22 (1988), S. 401–412.
[10] Feik, H.J. und McClaskey, J.D.: Gutbettwalzenmühlen für die Zerkleinerung von Erzen und Mineralien — Eine Übersicht über jüngste Veröffentlichungen. Aufbereitung-stechnik 44 (2003), Nr. 11–12, S. 53–67.
[11] Morley, C.: The case for High Pressure Grinding Rolls. Randol Conference (1995), S. 1–16.
[12] Morley, C.: Flowsheets for HPGR. SAG Conference (2006), S. IV172–IV189.
[13] Heinicke, F.: Beitrag zur Modellierung der Zerkleinerung in Gutbettwalzenmühlen. Dissertation. Rheinisch-Westfälische Technische Hochschule Aachen, 2012.
[14] Preuss, S., Studies on multiple-scale grinding in High Pressure Grinding Rollers, Master Thesis, TU Bergakademie Freiberg, 2015.