Афанасова Алена, Плотников Денис; фото: Афанасова Алена
На обогатительной фабрике Кольской ГМК искусственный интеллект учится контролировать флотацию. ИИ при помощи машинного зрения оценивает состояние технологического процесса, прогнозирует, каким он будет через 20–40 минут, и дает советы по его улучшению.
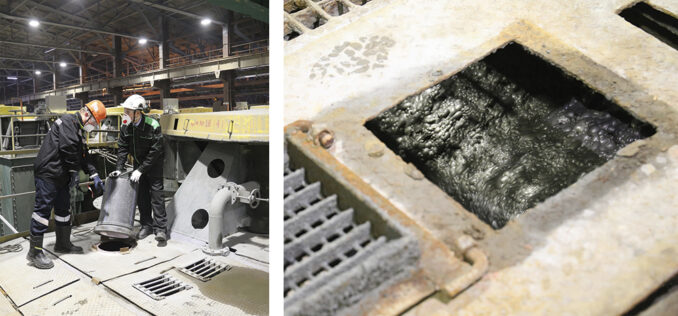
Сложный путь превращения руды в металл
Производственные и технологические процессы Кольской ГМК — это сложный путь превращения руды в металл. Обогатительная фабрика Кольской ГМК — одно из важнейших звеньев производственной цепочки получения цветных металлов. Здесь добытая горняками рудника «Северный» руда сначала проходит дробление, несколько стадий измельчения, а после отправляется на участок флотации. В больших аппаратах с помощью специальных машин и реагентов частички, содержащие металлы, поднимаются вверх в виде пузырьков и отправляются на дальнейшую переработку, а пустая порода в виде осадка выводится из технологического процесса.
На этом контуре флотации и начали проводить испытание искусственного интеллекта, который с помощью прогнозных моделей и машинного зрения оценивает состояние технологического процесса и предсказывает, каким он будет через 20–40 минут. Исходя из этого он оценивает, какие действия требуются для улучшения процесса, сам подбирает необходимые параметры: дозировку реагентов, уровни во флотомашинах, расход воздуха — и позволяет маленькими шагами двигаться к оптимальным значениям благодаря тому, что непосредственное управление алгоритмом осуществляют автоматизированные системы управления технологическим процессом — АСУ ТП. В интерфейсе платформы выводится вся информация, необходимая оператору, даются рекомендации, в панели также можно изменить настройки под конкретный агрегат.
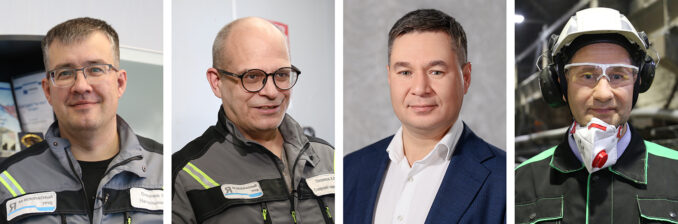
— Команда ПАО ГМК и Кольская ГМК пилотируют собственный проект по машинному зрению, по распознаванию пенного продукта флотации. Задача данного проекта — получить информацию от видеокамеры по пенному продукту, сделать обработку нейронной сетью, выделить основные параметры: скорость пеносъема, как пена движется по флотомашине, размер пузырьков, стабильность пены. Одно из направлений — это цветность пены. Данную информацию мы хотим использовать для дальнейшей оптимизации флотации. Это изменение состава реагентики, это изменение уровня пульпы, изменение уровня воздуха, которые повысят извлечение на флотомашине и выход концентрата, — рассказал главный менеджер департамента инноваций и цифровых технологий КГМК Евгений Батц.
Звучит просто, но на деле — сложное цифровое решение: применение искусственного интеллекта в промышленности
В отделении флотации установлены камеры видеонаблюдения, которые передают данные на сервер интеллектуальной видеоаналитики, а далее этот видеопоток уже использует искусственный интеллект для повышения эффективности управления процессом флотации.
Звучит просто, но на деле это очень сложное цифровое решение. Особенность системы в том, что искусственный интеллект не только оценивает состояние технологического процесса в каждом отделении, но и прогнозирует, каким оно будет через 20–40 минут, а исходя из полученных данных оценивает, какие действия требуются для улучшения процесса.
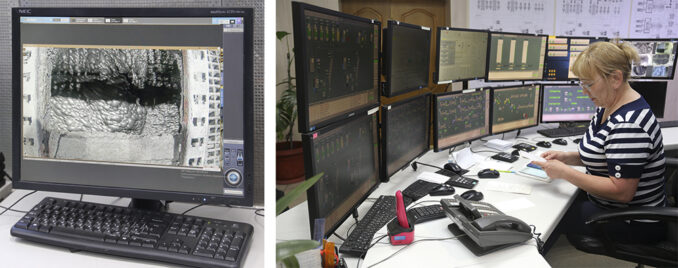
Задача — получить информацию с видеокамер по пенному продукту флотопотока, обработать данные с помощью нейронных сетей и выделить основные параметры: скорость пеносъема, как пена движется по флотомашине, размер пузырьков, стабильность пены.
Далее компьютерное зрение при помощи специального алгоритма обрабатывает видеопоток и определяет характеристики пены в автоматическом режиме. При определении формы и размера пузырьков используется метод сегментации изображений, полученных с видеокамер.
Дальше дело за малым: данные обрабатываются, затем в интерфейсе платформы выводится вся информация, необходимая оператору, и даются рекомендации, при этом оператор может задавать настройки в системе под конкретный агрегат.
Доверие нужно заслужить
Диспетчерская обогатительной фабрики — здесь за технологическими параметрами: эффективность измельчения, каких и сколько реагентов нужно добавить во флотомашину, качество пульпы — пузырьков, содержащих нужный металл, — следит человек.
— Вот на данный момент мы запустили мельницу. Выходит сигнализация, что нужно открыть реагенты. То есть сейчас у меня пойдет переработка, и, соответственно, я открою реагенты. Это для нас цифровая помощь, — поделилась оператор пульта управления обогатительной фабрики КГМК Фания Каменева.
Сегодня за процессом оператору уже помогают следить многочисленные приборы и датчики, выводящие показания и рекомендации на экраны мониторов. Поэтому к дальнейшей автоматизации здесь морально готовы. Но в диспетчерской постоянно раздаются и телефонные звонки. Это флотаторы — люди, работающие на местах, — докладывают обстановку.
— Готовы, но все равно, наверное, без человека в таких объемах не обойтись, — отметила Фания Каменева.
Искусственный интеллект еще должен заслужить доверие оператора, шутят на фабрике. Но совместная работа должна не только повысить извлечение концентрата, богатого металлами, но и обезопасить технологический процесс от так называемого человеческого фактора. А значит, повысить надежность и бесперебойность всей производственной цепочки горно-металлургической компании.
В постоянном поиске новых решений по внедрению искусственного интеллекта в промышленность
Для запуска прототипа использовали цифровую платформу, на которую можно ставить различные решения и приложения для определенной очереди флотации. Саму платформу с приложениями можно сравнить с конструктором «Лего»: как из его деталей собирают разные объекты, так и с помощью приложений создают различные решения для той или иной флотомашины.
— Данная концепция искусственного интеллекта отличается от того, что мы использовали ранее, здесь применили алгоритм нашей собственной разработки по управлению техническим процессом, — поведал главный технолог обогатительной фабрики Артур Шориков. — Возможно, будем между собой увязывать системы, чтобы принцип работы нашего алгоритма дополнялся принципами работы разработанной оптимизационной модели, и это будет совместный продукт, который учитывает опыт непосредственно технологов-производственников, программистов, математиков и айтишников.
Опытно-промышленные испытания новой цифровой платформы с применением машинного зрения проходили на двух машинах первой секции флотации обогатительной фабрики.
— Результаты прошедших испытаний достаточно позитивные для нас, если учесть всю специфику процесса. При автоматическом режиме работы фабрика выигрывает более 0,5 % извлечения металлов в сравнении с ручным. Обогатительная фабрика у нас достаточно автоматизированная, но процесс автоматизации идет постоянно. Нельзя остановиться, потому что технологии шагнули вперед, и надо за ними успевать, поэтому этот процесс будет бесконечным. Для нас автоматизация — хороший повод улучшить свои показатели, параметры по производству, мы постоянно в поиске новых решений и проектов для всей фабрики, — рассказал начальник обогатительной фабрики Владимир Баранов.
Применение ИИ в промышленности: инновации на то и инновации
— Во всем «Норникеле» никто системно к вопросу внедрения решений на базе искусственного интеллекта не подходил, когда мы с вами начали этим заниматься. Еще в 2019 году мы начинали анализировать данные и строить систему-советчика. Мы поняли, что необходимо развивать системы с автоматическим принятием решений, где алгоритм будет сам давать сотни тысяч решений и помогать оператору управлять процессом. Этот проект стал отправной точкой цифровой эволюции. Благодаря ему мы создали свой центр компетенций, у нас в компании уже появились новые штатные единицы — дата-инженеры, Data Scientist, которые уже сегодня реализуют уникальные проекты на площадке в Мончегорске, — поведал директор департамента инноваций и цифровых технологий КГМК Дмитрий Санников. Кроме того, Дмитрий Санников отметил, что такие специалисты начинают разрабатывать собственные алгоритмы и внедрять их на других объектах компании.
— Такая эффективная командная работа, где искусственный интеллект выступает в роли цифрового помощника, позволяет увеличивать показатели качества извлечения металлов. Компания не останавливается на достигнутом значении извлечения металлов более 0,5 %. Уже сформирована программа по повышению данного показателя за счет развития алгоритма управления качеством на машинах и секциях, балансировки потоков и работы с реагентами под изменяющиеся виды руды. Сейчас проходят опытно-промышленные испытания аптаймом работы решения в автоматическом режиме, равном 98 %, — отметил Дмитрий Санников.
— Совершенствование процессов возможно лишь благодаря слаженной работе, когда многолетний опыт, навыки сотрудников и их умение мыслить вне шаблона объединяются с высокой скоростью и точностью обработки данных искусственным интеллектом. Ведь инновации на то и инновации, что должны живо и оперативно открывать новые и расширять существующие горизонты использования современных инструментов и подходов для совершенствования работы в компании, — подытожил Дмитрий Санников.