Бодуэн А. Я., Поперечникова О. Ю., Залесов М. В., Григорьева В. А.
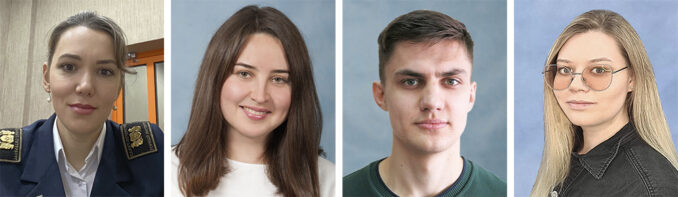
Для коренных месторождений золотоносных руд характерно разнообразие химического и минералогического состава. Поиск рентабельного способа переработки золотосодержащих руд неразрывно связан с комплексом предварительных исследований, направленных на изучение состава руды, форм нахождения полезных компонентов, а также оценку влияния примесных элементов и физических характеристик руды на процесс прямого извлечения золота либо обогащения руды.
Помимо гравитационного и флотационного обогащения, активное применение в промышленности нашли технологии предварительной подготовки сырья перед цианированием, включающие в себя операции сверхтонкого измельчения, окислительного обжига, бактериального и автоклавного окисления, а также комбинирования этих операций.
Для оценки эффективности применения различных методов подготовки сырья перед цианированием в качестве предмета исследования рассматривался упорный золотосодержащий флотационный концентрат, полученный из пирит-арсенопиритной руды.
Ряд исследований, направленных на поиск рациональных параметров цианирования флотоконцентрата, позволил получить извлечение золота из концентрата на уровне 45 %. Дальнейшие исследования по предварительной обработке флотоконцентрата и последующему цианированию позволили получить следующие показатели извлечения золота:
— 44,95 % — при цианировании флотоконцентрата исходной крупности;
— 56 % — при цианировании флотоконцентрата после ультратонкого измельчения;
— применение окислительного обжига позволило увеличить извлечение золота до 85 %;
— автоклавное окислительное выщелачивание (POX) обеспечило извлечение золота на уровне 92,8–94,5 %.
Показатель извлечения золота является главным, но не единственным критерием выбора технологии переработки золотосодержащих руд и концентратов. Следует учитывать эксплуатационные и капитальные затраты, запасы сырья, географию района, наличие развитой инфраструктуры и квалифицированных кадров. Для каждого конкретного золоторудного месторождения необходимо проводить технологические исследования и технико-экономическое обоснование разработанной технологии.
Ключевые слова: упорный золотосодержащий концентрат, автоклавное окисление, ультратонкое измельчение, обжиг, извлечение, степень окисления, цианирование.
Введение
Тенденция истощения запасов легкоцианируемого сырья вынуждает золотопромышленников вовлекать в переработку руды сложного состава так называемые упорные руды [1]. Для упорных руд характерно наличие тонковкрапленного в пустую породу золота, в том числе ассоциированного с сульфидными минералами [2]. Помимо перечисленного, некоторые руды также содержат «активный» углерод, сорбирующий золото на стадии цианирования (явление прег-роббинга) [2], высокая сорбционная активность рассеянного углеродистого материала существенно влияет на технологию переработки
руд и концентратов как флотационным, так и пиро- и гидрометаллургическим методами [3]. Коллективы авторов [4, 5] отмечают, что за последние 20 лет содержание золота в рудах снизилось в 1,2–1,5 раза, доля труднообогатимых руд в общей массе сырья, поступающего на обогащение, возросла с 15 до 40 %. Увеличение доли переработки труднообогатимых золотых и комплексных золотосодержащих руд может обеспечить значительный прирост добычи золота в мире [6]. Традиционные технологии извлечения золота из упорных руд включают в себя флотационное обогащение, обжиг и последующее цианирование огарка. Однако ужесточение норм по выбросам в атмосферу, в частности по компонентам, входящим в состав отходящих газов обжига мышьяксодержащего сырья, и дороговизна установок, позволяющих очистить газовый поток от токсичных примесей, способствуют переходу от пирометаллургических к гидрометаллургическим способам подготовки сырья, содержащего металлоиды в своем составе. Из-за отсутствия газовых выбросов соединений высокотоксичного мышьяка и серы, более высокого извлечения золота по сравнению с другими методами наибольшее предпочтение отдают гидрометаллургическим автоклавным технологиям [7–10].
Несмотря на высокие капитальные затраты, автоклавное окислительное выщелачивание имеет ряд преимуществ по сравнению с технологией обжига:
• более высокое извлечение золота;
• отсутствие газовых выбросов соединений мышьяка и серы;
• вывод мышьяка в виде малотоксичного арсената железа, сброс которого возможен в обычное хвостохранилище.
В ряде случаев, при переработке упорного сырья с высоким содержанием сульфидной серы, наиболее эффективным является совместное применение технологий автоклавного и бактериального выщелачивания — «BIOX-POX-процесс» [11]. Комбинированная технология позволяет значительно сократить продолжительность и объемы оборудования биовыщелачивания за счет неполного окисления сульфидов и увеличить извлечение золота [12].
В данной статье отражены результаты опытов по прямому цианированию высокосернистого флотоконцентрата и четыре варианта технологии переработки упорного золотосодержащего концентрата.
Характеристика объекта исследования
Изучение химико-минералогического состава концентрата проводилось с использованием современных методов физико-химического анализа. Химический состав флотационного концентрата представлен в таблице 1.
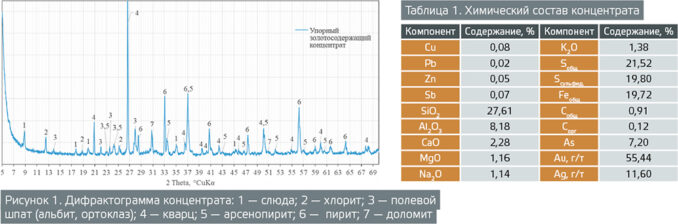
Минеральный состав концентрата, определенный рентгенофазовым методом анализа, представлен на рисунке 1. Пробы концентрата на 50,2 % состоят из сульфидных минералов: пирита (35,5 %) и арсенопирита (14,7 %). Микроанализ пиритов показал наличие мышьяковистых разновидностей с содержанием As в них от 0,7 до 5,1 %. Нерудные минералы (49,8 %) представлены кварцем (19,3 %), полевыми шпатами (10,5 %), тонкозернистой слюдой — серицитом (9,5 %), доломитом (4,5 %) и хлоритами (5,0 %).
Для изучения золота и сульфидных минералов произведено разделение пробы в тяжелой жидкости (М-45, ρ = 3 г/см3).
В тяжелой фракции частицы золота наблюдаются в виде крупных свободных зерен (рис. 2, 3), а также в сростках с сульфидами. Размер свободных золотин варьируется от 20 до 150 мкм. В сростках с сульфидами, как правило, размер золотин не превышает 20 мкм [13]. Самородное золото содержит примеси серебра от 10 до 13 % масс. При микроскопическом исследовании выявлено наличие тонкодисперсного золота на границах срастания пирита и арсенопирита. Золото в таких сростках имеет каплевидную форму размером не более 2–3 мкм.
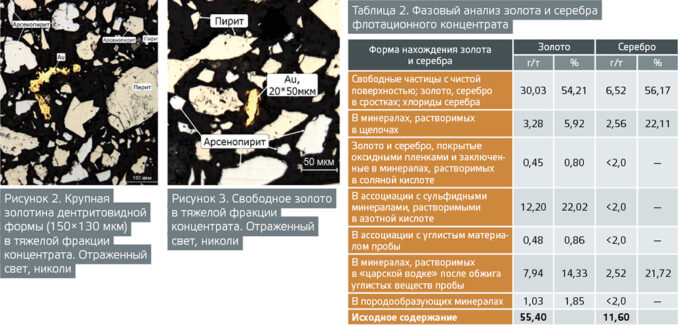
Результаты фазового анализа, отражающие нахождение золота и серебра в флотационном концентрате, приведены в таблице 2.
Исследование различных способов подготовки флотоконцентрата к последующему извлечению золота цианированием
Стоит отметить, что значительная часть золота во флотоконцентрате (22 %) заключена в сульфидной матрице (главным образом Au ассоциировано с пиритом и арсенопиритом), препятствующей доступу выщелачивающего компонента (NaCN) к благороднометалльной составляющей концентрата, в результате для процесса прямого цианирования характерны низкие показатели извлечения золота. Данный факт является предпосылкой к разработке технологии предварительной подготовки материала к цианированию, заключающейся в окислении сульфидов.
Схема исследований по подготовке концентрата к извлечению золота цианированием представлена на рисунке 4.
Для экспериментов по цианидному выщелачиванию (рис. 5), независимо от операции подготовки концентрата, были выбраны следующие параметры: плотность пульпы по твердому — 20 % масс, концентрация цианида натрия — 1,0 г/л, время процесса — 24 часа, рН — 10,5–11,0.
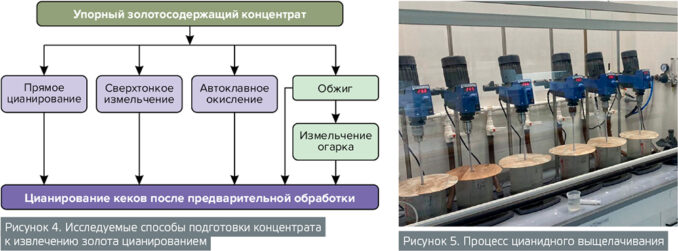
Исследование влияния гранулометрического состава флотоконцентрата на извлечение золота при цианировании
Исследование влияния гранулометрического состава на показатели процесса цианирования проводили на флотоконцентрате исходной крупности (66 % класса -0,071 мм) и на концентрате, подвергнутом измельчению в планетарной мельнице Fritsch (рис. 6) до крупности 100 % класса -0,020 мм. Результаты исследований сведены в таблицу 3.
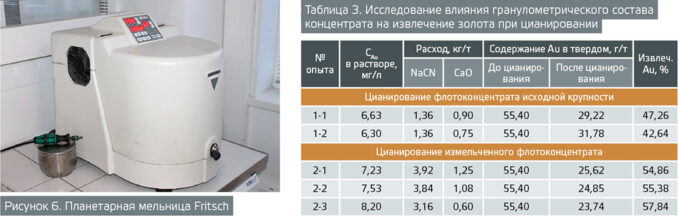
В результате цианирования концентрата исходной крупности удалось достичь извлечения Au в раствор в диапазоне 42,64–47,26 %. Предварительное измельчение концентрата позволило улучшить показатели цианирования и перевести в раствор до 54,86–57,84 % золота. Ультратонкий помол обеспечивает дополнительное раскрытие минералов, заключающих золото, однако не приводит
к значительному повышению уровня извлечения (абсолютный прирост составляет 11,08 %). Увеличение расхода реагентов на проведение процесса связано с протеканием побочных реакций.
Ни один из опробованных способов не дал удовлетворительных показателей извлечения золота, что свидетельствует о необходимости исследования других технологий подготовки упорного золотосодержащего сырья.
Исследование влияния предварительного обжига флотоконцентрата на извлечение золота в раствор при последующем цианировании
Основными преимуществами обжигового метода являются простота и освоенность, материал после обжига приобретает пористую, хорошо проницаемую структуру, которая способствует повышению уровня извлечения ценных компонентов и скорости процесса цианирования. Данный способ до сих пор имеет промышленное применение в ряде стран — Канаде, ЮАР, Австралии и др.
Однако высокие температуры, используемые во время обжига, позволяют большей части мышьяка улетучиваться в виде As2O3, выбросы которых в атмосферу строго ограничены во всем мире [12].
Отходящие газы обжиговой печи содержат SO2 и другие летучие соединения, а также частицы пыли, в связи с чем требуются дорогостоящие операции очистки [14] перед сбросом в атмосферу, а именно: охлаждение с помощью теплообменника, удаление пыли, твердых частиц в электрофильтре, обработка в скруббере. Помимо перечисленного, подготовка сырья к цианированию путем окислительного обжига неразрывно связана с проблемой потерь золота с пылегазовой фазой от 3 до 25 %, т. е. появляется необходимость проведения процесса доизвлечения золота из продуктов системы пылеулавливания. Обжиг зачастую позволяет удалить природное углистое вещество, вызывающее эффект «прег-роббинга». Однако существуют и примеры активации ранее неактивного угля (следствие добавки угля с целью повышения температуры в агрегате).
В процессе обжига материал может частично оплавляться за счет более низких температур плавления отдельных минералов, входящих в состав материала, в сравнении с температурой проведения процесса. Вследствие этого происходит инкапсуляция золотин пленкой оксидов железа, препятствующей доступу выщелачивателя, что влечет за собой повышенные потери золота с хвостами цианирования [15]. Проблему образования пленок можно решить путем механоактивации огарка. Принимая во внимание данный факт, обожженный материал был разделен на несколько навесок для проведения опытов по цианированию огарка и образцов, подвергнутых механоактивации (измельчению) в планетарной мельнице Fritsch.
Параметры обжига: продолжительность — 3 часа, температура — 650–700 ºС, параметры цианирования аналогичны предыдущим экспериментам. При данных условиях степень окисления сульфидной серы составила 95 %, степень деарсенизации — 92 %.
В таблице 4 отражен химический состав огарка.
Основными минеральными фазами (рисунок 7) огарка являются гидроокислы железа, кварц, полевые шпаты, слоистые алюмосиликаты (слюды, хлориты) и барит. Сульфидные минералы при оптическом и электронно-микроскопическом исследовании наблюдаются лишь в качестве реликтовых зерен, практически нацело замещенные оксидами железа и мышьяка.
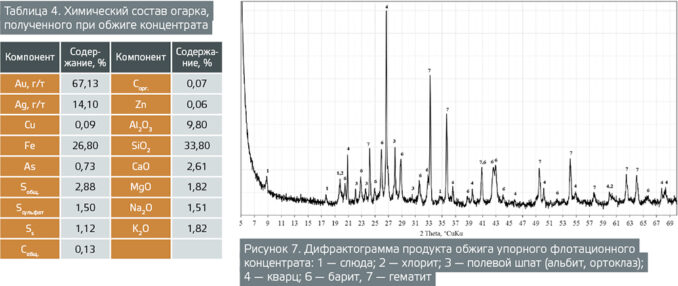
Далее приведены микрофотографии зерен оксидов (рисунок 8б) и гидроксидов железа, образовавшихся при обжиге, а также тонкое золото, связанное с этими агрегатами (рисунок 9).
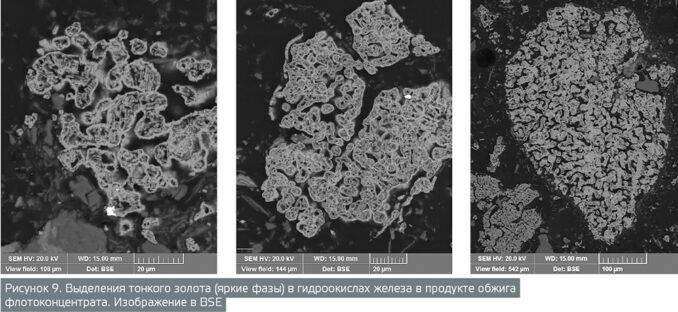
В таблице 5 представлены результаты выщелачивания золота из огарка.
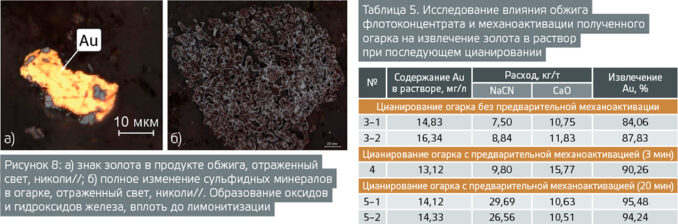
Операция обжига перед цианированием, несмотря на увеличение показателя извлечения золота на 41 %, приводит к повышенному расходу реагентов в сравнении с базовым опытом по прямому цианированию ввиду протекания вторичных реакций, что объясняется высокой пористостью огарка и наличием окисленных форм железа.
Механоактивация материала в течение 20 минут приводит к переизмельчению огарка: увеличивается площадь реакционной поверхности и удельный расход реагентов, затрачиваемых в основном на взаимодействие с раскрытыми в ходе измельчения минералами. Средний удельный расход цианида возрастает в 3,6 раза по сравнению с опытом с механоактивацией огарка в течение трех минут.
Анализ результатов исследований:
— обжиг флотационного концентрата позволил повысить извлечение золота цианированием с 44,95 % до 85,95 %;
— измельчение огарка в течение трех минут обеспечивает прирост извлечения золота на 4,31 %, при механоактивации в течение 20 минут — на 8,91 %.
Исследование влияния автоклавного окисления флотоконцентрата на извлечение золота в раствор при последующем цианировании
Автоклавные методы основаны на окислении сульфидов, содержащихся в сырье и концентратах обогащения, кислородом при повышенных температуре и давлении [6]. Ассоциированное с сульфидами субмикроскопическое и труднорастворимое золото освобождается и становится доступным для выщелачивания цианистым раствором.
Методика проведения исследований автоклавного окисления
Исходный концентрат подвергали декарбонизации в серной кислоте, а затем разбавляли необходимым количеством дистиллированной воды, полученную пульпу загружали в титановый автоклав (рис. 10). Массу навески и отношение (Ж:Т) в питании автоклава рассчитывали на основании данных по содержанию сульфидной серы в концентрате по формуле 1.
Содержание твердого в пульпе, % масс. = (0,295·CS2-+ 0,825)-1 ·100 (1), где CS2- — содержание сульфидной серы в твердой фазе, %.
Согласно данным статьи авторов [16], формула 1 позволяет обеспечить автогенный режим выщелачивания за счет тепла, выделяющегося при окислении сульфидной серы.
Автоклавное окисление осуществлялось при постоянных значениях давления и температуры за счет автоматических датчиков фирмы Bronkhorst.
Результаты опытов по автоклавному окислению концентрата представлены в таблице 6.
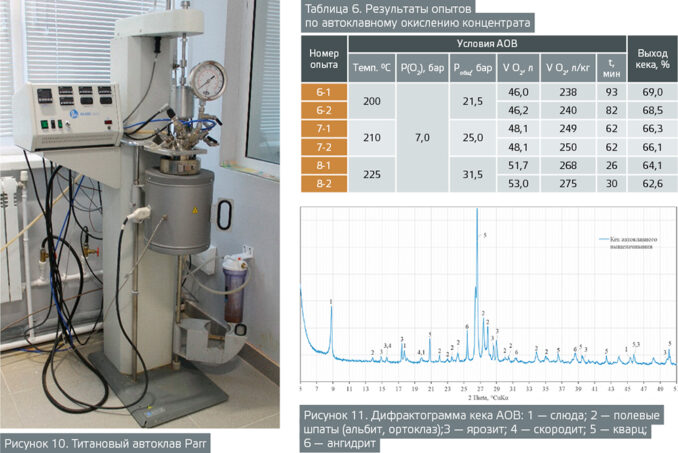
Особенностью автоклавного окисления высокосернистого концентрата является образование повышенного количества основных сульфатов железа и ярозитов, что является причиной повышенного расхода реагентов на операциях нейтрализации и цианирования [17]. Фазовый анализ кека автоклавного окисления показал, что доля цианируемого золота увеличилась до 96,08 % против 54,21 % для неокисленного флотоконцентрата. Основные минеральные формы кека АОВ отражены на дифрактограмме (рис. 11). Четких пиков, определяющих сульфидные минералы, а именно пирит и арсенопирит, ввиду низких содержаний на дифрактограммах не выявлено.
Для более подробного изучения сульфидной фракции и морфологии золота была выделена тяжелая фракция из обесшламленного продукта с последующим анализом Au в шламовой и легкой фракции. Золото в тяжелой фракции встречено в основном в свободной форме со средним размером золотин 50–70 мкм (рис. 12). В качестве единичных знаков встречены тонкие золотины в «рубашке» гидроокислов (рис. 13).
Результаты цианирования кеков автоклавного выщелачивания представлены в таблице 7.
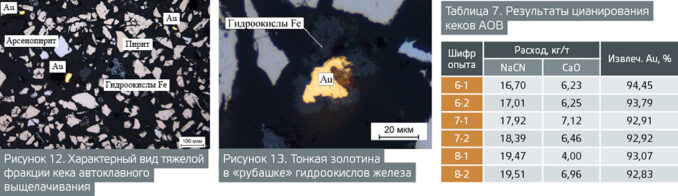
Минимальный расход цианида натрия соответствует выщелачиванию золота из кека АОВ, полученного при температуре 200 ºС, однако при этих условиях продолжительность процесса составляет 90 минут, а при температуре 225 ºС — 30 минут.
Значительное снижение температуры АОВ ниже 200 ºС не рекомендуется ввиду формирования серы в элементарном виде и серо-сульфидных гранул в диапазоне температур от 0 до 180 ºС [18]. Присутствие элементной серы ведет к повышенному расходу цианида, а также может привести к сбоям в работе автоклавного передела.
Заключение
Золотосодержащий концентрат, исследованный в рамках данной работы, относится к категории упорных материалов. Извлечение золота затруднено в связи с его ассоциацией с сульфидами. Базовым тестом, необходимым для оценки эффективности применения каждого из способов предварительной обработки, выступало прямое цианирование флотоконцентрата исходной крупности (66 % класса -0,071 мм), извлечение при котором составило 45 %. Для выбора рациональной технологии переработки упорного золотосодержащего концентрата было осуществлено опробование существующих способов подготовки сульфидных концентратов с последующей оценкой извлечения золота цианированием: обжиг, механоактивация, автоклавное окислительное выщелачивание.
Извлечение золота при цианировании доизмельченного флотоконцентрата до крупности 100 % класса -0,020 мм составляет 56 %. Более полное раскрытие минеральных зерен влечет за собой прирост извлечения на 11,08 % в сравнении с базовым тестом и, как следствие, увеличение удельного расхода цианида в 2,68 раза.
Обжиг флотационного концентрата перед цианированием позволяет окислить 95 % входящей в состав сульфидной серы и, как результат, раскрыть тонко диспергированное золото в сульфидных минералах. Достигается извлечение Au в раствор на 85,95 % при расходе NaCN 8,17 кг/т. Механоактивация огарка в течение трех минут позволяет увеличить извлечение в сравнении с опытом без механоактивации на 4,31 % (расход NaCN cоставил 9,80 кг/т). Извлечение золота в опыте с механоактивацией огарка в течение 20 минут составило 94,86 %, однако переизмельчение материала привело и к значительному росту расхода (до 28,13 кг/т).
Опыты по автоклавному вскрытию сырья показывают стабильно высокое извлечение золота (на уровне 92,83–94,45 %) при цианировании кеков АО. Увеличение удельных расходов реагентов при увеличении температуры (в диапазоне 200–225 ºС) проведения автоклавного вскрытия сырья обосновывается более полным раскрытием минералов.
Проведенные экспериментальные исследования показали, что применение автоклавного процесса для переработки упорного золотосодержащего сырья обеспечивает высокую интенсивность окисления и полноту извлечения золота при последующем цианировании. В автоклавной технологии не образуется токсичных газообразных выбросов, что определяет ее экологическую привлекательность. Однако для окончательного выбора технологии переработки необходимо выполнить технико-экономическое обоснование, оценить географическое местоположение месторождения, удаленность от основных промышленных районов, наличие существующих производственных мощностей, доступность квалифицированной рабочей силы и др.
Список литературы
1. А. И. Иванов, А. И. Черных, Е. А. Наумов, А. Г. Волчков, Д. А. Куликов, В. Н. Хасанов, Я. В. Алексеев, К. М. Минькин, А. С. Тарасов, И. В. Попов. Геолого-разведочные работы на благородные металлы за средства федерального бюджета в ХХI веке — результаты и перспективы.
2. Лодейщиков В. В. Технология извлечения золота и серебра из упорных руд // Иркутск, ОАО «Иргиредмет». 1999. Том. 2. С. 452.
3. Aleksandrova, Tatyana N., Heide, Gerhard, Afanasova, Anastasiya V. (2019) Assessment of refractory gold-bearing ores based of interpretation of thermal analysis data. Journal of Mining Institute, vol. 235, pp. 30–37. DOI: 10.31897/PMI.2019.1.30.
4. Федотов П. К., Сенченко А. Е., Федотов К. В., Бурдонов А. Е. (2020). Исследования обогатимости сульфидных и окисленных руд золоторудных месторождений Алданского щита. Записки Горного института, 242, 218. https://doi.org/10.31897/pmi.2020.2.218
5. Гильмутдинова Р. А., Мичурин С. В., Ковтуненко С. В., Елизарьева Е. Н. / К вопросу об использовании и переработке отходов горно-обогатительных комбинатов Южного Урала // Успехи современного естествознания. — 2017. — № 2 — С. 68–73.
6. Фокина С. Б., Сизяков В. М., Маркелов А. В., Иваник С. А./Поведение мышьяка при нейтрализации растворов после автоклавного окисления пирит-арсенопиритных концентратов // Естественные и технические науки. — 2012. — № 1 (57). С. 376–381.
7. Иваник С. А., Илюхин Д. А. (2020). Флотационное выделение элементарной серы из золотосодержащих кеков. Записки Горного института, 242, 202. https://doi.org/10.31897/pmi.2020.2.202
8. Adams M.D. Advances in gold ore processing. Elsevier, 2005. Vol. 15. 1076 p.
9. Сопоставительная оценка вариантов переработки упорных флотоконцентратов. Емельянов Ю. Е., Богородский А. В., Баликов С. В., Епифоров А. В. Цветные металлы. — 2012. — № 8. — С. 10–12.
10. Богинская А. С., Маркелов А. В., Шнеерсон Я. М., Петров Г. В. /Применение метода математического моделирования для расчета процесса автоклавного окисления упорного сульфидного золотосодержащего флотоконцентрата// Фундаментальные исследования. — 2014. — № 3 (часть 4) — С. 706–710.
11. Седельникова Г. В. Сравнение автоклавного и бактериального выщелачивания // Золото и технологии. 2014. № 2 (24). С. 110–115.
12. Санакулов К. С., Мустакимов О. М., Эргашев У. А., Ахатов Н. А. О целесообразности применения комбинированных технологий для переработки особо упорных золотосульфидных руд / Цветные металлы. — 2016. — № 2. — С. 9–15.
13. Меретуков М. А. Золото: химия, минералогия, металлургия // М. Издательский дом «Руда и металлы». 2008. С. 528.
14. Баликов С. В., Дементьев В. Е., Минеев Г. Г. Обжиг золотосодержащих концентратов. Иргиредмет: Иркутск, 2002. С. 416.
15. Луганов В. А., Чепуштанова Т. А., Гусейнова и др. Технологические исследования переработки золото-мышьяково-угольных концентратов // Материалы Международной научно-практической конференции «Эффективные технологии производства цветных, редких и благородных металлов», Алматы, 2018.
16. JOM, September 1990, Michael H. Conway and Donald C. Gale, Sulfur’s Impact on the Size of Pressure Oxidation Autoclaves.
17. Сизяков В. М., Иваник С. А., Богинская А. С., Битков Г. А. Обезвоживание пульп после автоклавного выщелачивания тонкоизмельченных сульфидных концентратов // Естественные и технические науки. 2012. — № 1 (57). — С. 369–375.
18. Набойченко С. С. и др. Автоклавная гидрометаллургия цветных металлов. Екатеринбург: ГОУ ВПО УГТУ-УПИ, 2009. — Т. 1, с. 376. Т. 2, с. 612.
(1) — Санкт-Петербургский горный университет, кафедра металлургии, г. Санкт-Петербург, Россия; (2) — АО «НПО «РИВС», г. Санкт-Петербург, Россия