С. М. Ефимов, ООО «Бижур Делимон»
Задача автоматического нанесения смазки на рельсы и стрелочные переводы остается на сегодняшний день нерешенной или решается частично и не комплексно.
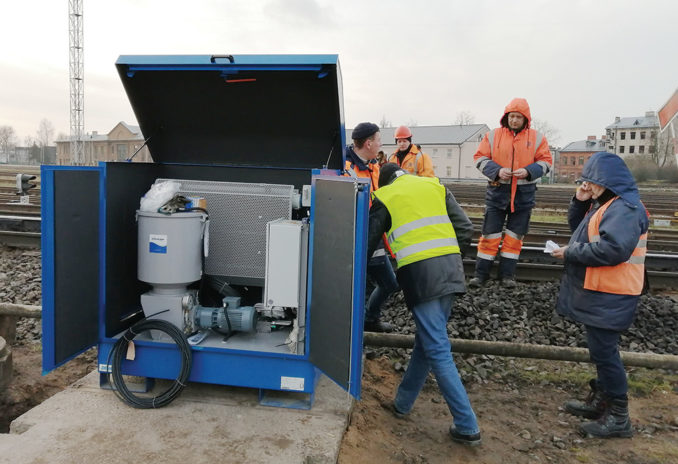
Практически с момента появления служб обслуживания путей одной из задач обходчиков и персонала был и остается контроль за состоянием путей, оценка уровня их износа, а также нанесение смазки. Нанесение смазки осуществлялось да и осуществляется по сей день в основном вручную, с использованием отработанного машинного масла или подручного смазочного материала. Данный процесс требует специально обученного персонала, соблюдения графиков обхода. Участок обслуживания ограничен физическими возможностями персонала, примитивным инструментарием, весом емкостей, загруженностью магистралей. Используемые смазочные материалы не имеют чаще всего достаточной адгезии и необходимого физико-химического состава. Все это не обеспечивает надежное и длительное удержание слоя смазки на головке рельса и не создает смазочную пленку необходимой толщины.
Как результат — низкая эффективность этой процедуры, а порой и ее опасность, если принять во внимание тот факт, что смазка может быть случайно нанесена на поверхность катания колеса, а это может привести к удлинению тормозного пути составов на данном участке. Человеческий фактор в этом процессе занимает ведущее место. Ведь происходит непосредственный контакт смазки и человека.
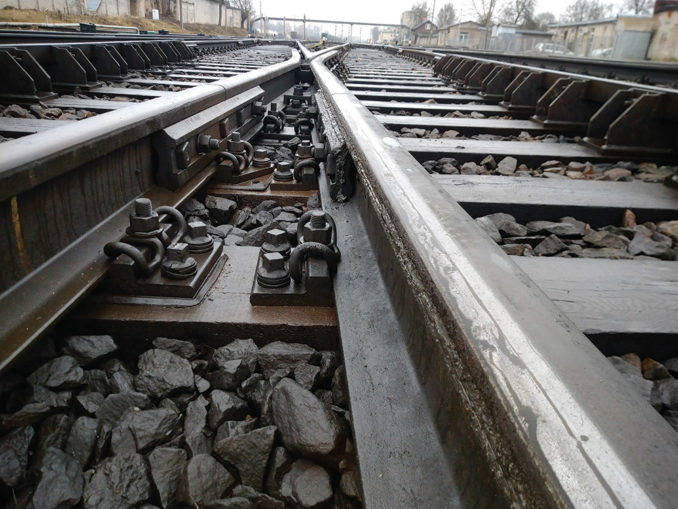
Несмотря на заметный скачок в развитии технологий производства рельс и колес, технология нанесения смазки не претерпела существенных изменений. Стереотипы и инертность обслуживающего персонала, а также скудные финансовые возможности железнодорожных хозяйств ограничивают и тормозят внедрение новых технологий в отрасли.
Тем не менее к настоящему времени существует уже достаточно технологий для проведения таких работ без участия человека в качестве исполнителя. Нанесение смазки на рельсы возможно как с применением мобильных систем (RailJet), установленных на подвижной состав, так и стационарных систем (StaTrack), привязанных к определенному месту или участку путей. Мобильные системы имеют невысокую стоимость и значительно большую зону покрытия по сравнению со стационарными системами.
Нанесение смазки на рельсы в такой системе осуществляется косвенно через колесо, которое первым принимает дозу смазки на гребень. Это повышает степень направленности процедуры на снижение износа колесных пар.
Стационарные же системы имеют более интенсивное и устойчивое покрытие рельс на определенном участке дистанции. В данном случае смазка выдавливается на боковые поверхности рельс, а разнос смазки осуществляется посредством накопления смазочного материала на смазочных шинах, подхвата его колесами и разносом этой смазки в зоны контакта рельс — колесо — рельс — колесо и т. д. Кроме этого, в стационарных системах применяют достаточно консистентные (густые) смазки класса вязкости от NLGI1 и выше для более интенсивного накапливания ее в зонах контакта и «четкого» прилипания ее к гребням колес.
Опыт прорывов в данной сфере начинается, как правило, с самого простого — встречи, обмена мнениями, изучения фотографий, отчетов, поиска в интернете. Даже в случае наличия обоюдной заинтересованности и опыта применения чаще всего сотрудничество начинается с испытаний и технико-экономического обоснования.
Одним из характерных примеров такого взаимодействия можно считать успешную реализацию проекта StaTrack компании BIJUR DELIMON International. В его реализации участвовало четыре стороны: Delimon GmbH (Германия), Vlavi Rail (Латвия), VAS Latvijas dzelzceļš (Латвийские железные дороги), ООО «Бижур Делимон» (Россия). Местом установки системы выбран участок сортировочной под Даугавпилсом.
Система смазки рельс типа StaTrack включает в себя насосную станцию с установленной в ней предохранительной, распределительной и контрольно-измерительной аппаратурой. Станция оснащена усиленным подогревом, позволяющим эксплуатировать станцию при низких температурах, до минус 40 градусов Цельсия.
Система управления включает:
— датчик температуры воздуха в шкафу с термостатом,
— датчик давления в напорной магистрали для контроля давления в системе,
— датчик уровня смазки в баке насоса,
— внешний датчик осадков для управления периодичностью работы системы,
— внешний датчик колес для оптимизации расхода смазки в зависимости от загруженности обслуживаемого участка железных дорог,
— датчик несанкционированного доступа в шкаф станции,
— датчик работы дозирующего смазочного распределителя для контроля и диагностики работы распределительные аппаратуры.
Отличительная особенность системы — все оборудование находится в одном защищенном, безопасном и доступном для обслуживания месте. Кроме того, в систему управления было внедрено удаленное управление и диагностика работы системы смазки с использованием мобильной связи стандарта GSM. Процесс обмена информацией осуществляется с помощью SMS в обе стороны: прием оповещающих сигналов от станции и отправка подтверждающих/управляющих сигналов от персонала, ответственного за работу системы.
Устройства нанесения смазки представляют собой смазочные шины, которые имеют простую и надежную конструкцию, обеспечивающую равномерное распределение и долгое удержание смазочного материала в зоне проката (погружения) колес.
После месяца эксплуатации системы смазка обнаруживается на расстоянии более 1 000 м от места установки смазочных шин. Масляная пленка имеет толщину 1–2 мм в зонах контакта. Четко виден перенос смазки от колеса к рельсу даже на стрелочных переводах.
На слух оценивается существенное снижение характерного высокочастотного шума: снижение уровня в этом диапазоне и сдвиг в средние и низкие частоты, что говорит о снижении коэффициента трения в контактной зоне. После 3–6 месяцев эксплуатации будет собрана статистика износа рельс и стрелочных переводов, о чем будет рассказано в следующей статье.
Москва, +7 (495) 637-36-06
Екатеринбург, +7 (985) 969-11-47
syefimov@bijurdelimon.com
www.bijur-delimon.ru