Плотников Денис, фото Кристины Коняхиной, пресс-службы Кольской ГМК
Реверс-инжиниринг, или обратное проектирование, — процесс разработки технической документации для уже готового изделия. С помощью 3D-сканеров инженеры создают цифровую модель, по которой можно подготовить документы к любым запчастям, электронным компонентам и оборудованию для производства их аналогов.
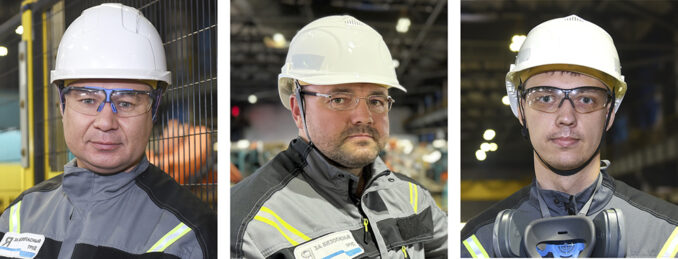
Практические шаги
Технология реверс-инжиниринга активно развивается в Кольском дивизионе «Норникеля». Это процесс разработки конструкторской документации и последующего изготовления оборудования или его компонентов на основе собранной информации и 3D-сканирования уже готового изделия.
— Уже есть практические шаги и первые результаты. Речь идёт о конструктивно сложных изделиях и электронных компонентах. Созданное по технологии реверс-инжиниринга оборудование уже применяется на руднике «Северный», — рассказал директор департамента по инновациям и цифровым технологиям Кольской ГМК Дмитрий Санников.
Речь идёт об элементах буровых машин, которые эксплуатируются на руднике «Северный». Для них разработали конструкторскую документацию на датчик углового положения, после чего была произведена партия из десяти штук.
— На сегодняшний день данное оборудование, созданное благодаря обратному проектированию, находится в непрерывной работе уже более 9 месяцев, что превышает срок службы оригинальных запчастей, — пояснил начальник управления автоматизации Кольской ГМК Валерий Горчаков. — Также разработаны линейный датчик и датчик наклона конструкции, которые сейчас проходят опытную эксплуатацию на буровой машине в условиях шахты.
Реверс-инжиниринг позволяет не просто «копировать» деталь, но ещё и усовершенствовать её за счёт замены материала, повышения его износостойкости.
— Например, при реверс-инжиниринге печатных плат возникала необходимость замены элементной базы, а также изменения расположения самих элементов на плате, — отметил кандидат технических наук, доцент Высшей аттестационной комиссии по специальности «Электрооборудование», главный менеджер управления автоматизации Кольской ГМК Сергей Карелин. Кроме того, эксперт отметил, что данные модификации были обусловлены замечаниями к работе оригинальных плат со стороны эксплуатирующих служб. — Именно поэтому при восстановлении вышедших из строя многослойных печатных плат мы учитывали многолетний опыт и рекомендации коллег, которые непосредственно эксплуатировали данное оборудование, — подытожил Сергей Карелин.
Ещё одним практическим применением технологии реверс-инжиниринга является работа по созданию конструкторской документации для насосов Munsch-200 и Munsch-400 в цехе электролиза никеля.
— Большое количество элементов, которые компания получила с помощью реверс-инжиниринга, применяются в цехе электролиза никеля или тестируются. В компании это уже выстроенный процесс. Раньше мы смотрели, что мы можем восстановить, более оперативно поставить, чтобы технологический процесс не прерывался или срок эксплуатации изделия был длительным. А сегодня это уже целая выстроенная процедура, которая включает в себя огромное количество заинтересованных сторон, и все участники между собой синхронизированы, — подчеркнул Дмитрий Санников.
Процесс обратного проектирования и реверс-инжиниринга
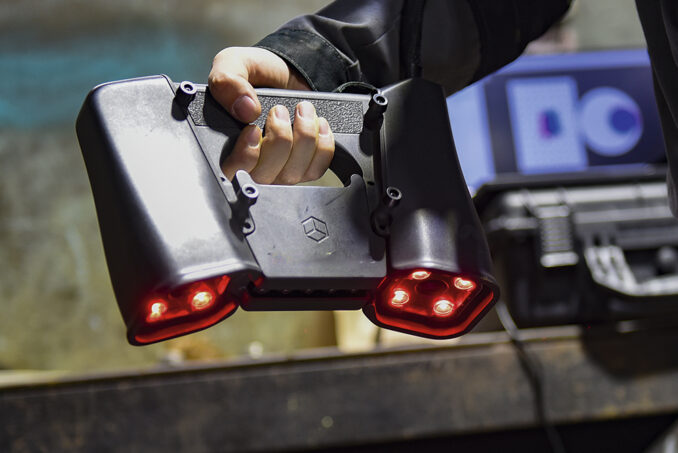
В среднем процесс получения конструкторской документации, например, для насосов Munsch-200 и Munsch-400 занимает порядка двух недель. Процесс начинается с разборки и последующей очистки всех деталей и узлов оборудования. Для сбора информации и создания «облака точек» на узлы и компоненты оборудования наклеивают специальные метки. Только на один насос ушло порядка 2,5 тысячи таких меток.
Затем при помощи сканера считывают метки и создают поле координат, которое автоматически передаётся на компьютер, где система формирует облако точек. Специальная программа «накладывает» на них сетку, создавая так называемую триангуляцию (измерение одного и того же показателя с помощью не менее чем трёх методов с целью независимого подтверждения результатов).
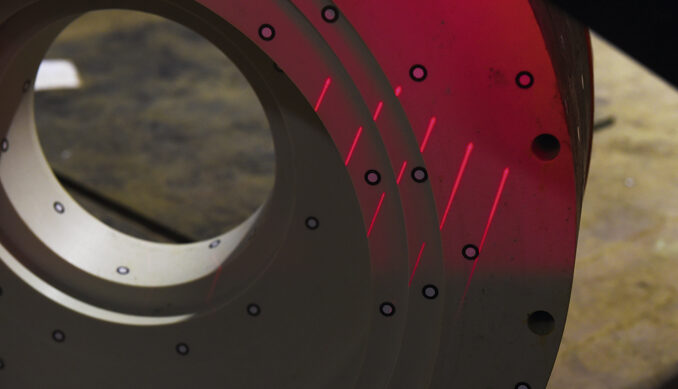
Полученный «чертёж» передаётся конструктору, который анализирует всю модель на предмет неточностей и отклонений. Любая ошибка или несоответствие могут сказаться на работе всего изделия.
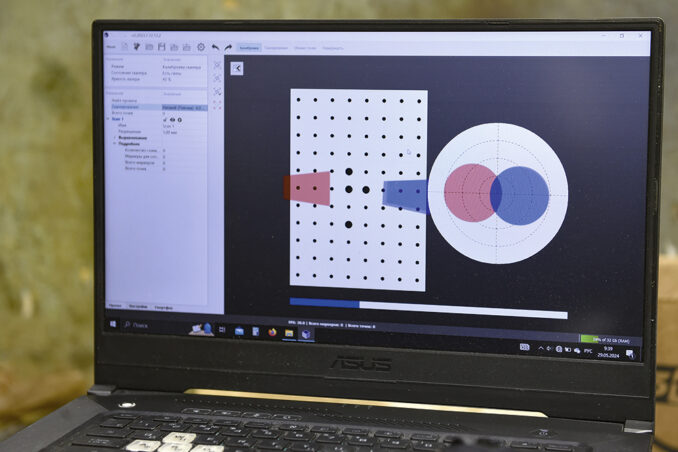
Отечественное производство
Среди основных преимуществ технологии — сокращение сроков и стоимости изготовления, а главное — возможность импортозамещения.
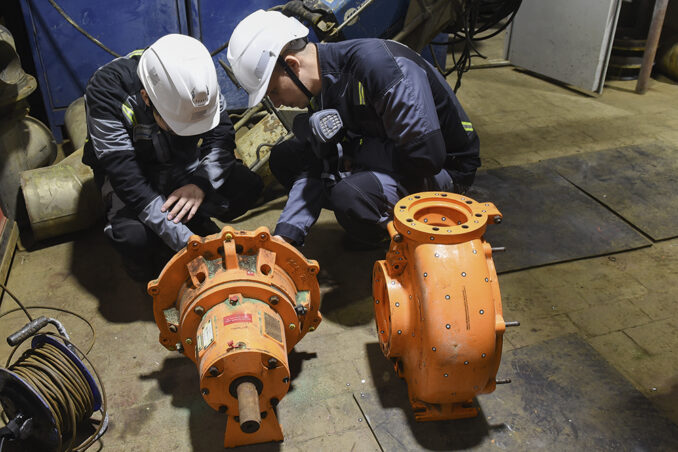
— Для Кольской ГМК особенно важно применять реверс-инжиниринг с учётом того, что многие компании, которые поставляли нам ранее оборудование, покинули российский рынок. На сегодняшний день это достаточно совершенный метод, где используется современное оборудование, — отметил исполняющий обязанности главного механика — начальника управления главного механика КГМК Евгений Абрашкин.
Главный менеджер департамента технологических инноваций «Норникель Спутник» Сергей Севагин рассказывает, что технология 3D-сканирования — инструмент для реверс-инжиниринга, который помогает ускорить процесс выпуска конструкторской документации, а впоследствии произвести запасные части.
— Она уже применяется в Заполярном филиале «Норникеля», Кольской ГМК, горнорудной компании «Быстринское». Сейчас импортозамещение развивается в нашей стране, и, соответственно, наша компания идет в ногу со временем. Преимущество в том, что благодаря созданным конструкторским документам мы передаём запасные части на отечественное производство, — рассказал Сергей Севагин.
По мнению директора департамента инноваций и цифровых технологий, любую деталь можно усовершенствовать, зная методы и технологии.
— Для изделий, которые контактируют непосредственно с рабочей средой, проводятся испытания в научно-техническом центре, определяется, из какого материала лучше их изготовить. Специальная комиссия оценивает, можно ли добиться лучших характеристик за счёт изменения химического состава, структуры и свойств материала, из которого изготавливается изделие, — пояснил Дмитрий Санников. — В «Норникеле» есть центр компетенций, эксперты которого чётко знают, с помощью каких методов и технологий можно усовершенствовать или изготовить абсолютно уникальную деталь, которая необходима именно для нашего производства.
Начальник механослужбы цеха электролиза никеля Андрей Труханов считает, что направление выбрано правильно.
— Сейчас коллеги используют технологию, чтобы оборудование в том числе модернизировать. Для компании это очень актуально. Мы заказываем тысячи запасных частей в год, объёмы огромные, — поделился Андрей Труханов.
Перспективы есть
На сегодняшний день в Кольском дивизионе «Норникеля» 3D-сканированием занимается подрядная организация, но в будущем эти функции смогут выполнять сотрудники компании.
— Мы планируем развивать собственный центр компетенций на базе проектно-конструкторского центра Кольского дивизиона. Руководитель центра совместно с группой экспертов уже не первый год участвуют в нашей совместной работе по выстраиванию нового системного подхода в развитии реверс-инжиниринга, применения аддитивных технологий и 3D-моделирования, — отметил Дмитрий Санников.
В прошлом году уже были определены конкретные изделия из полиамидов и пластикатов, на которых можно будет сосредоточить усилия специалистов.
— Для этого закупается профессиональное оборудование. Мы прорабатываем вопрос по развитию современного механообрабатывающего центра внутри Кольского дивизиона, — заявил Дмитрий Санников.
Технология реверс-инжиниринга позволит удовлетворить потребности в прототипировании импортных деталей, которые будут изготовлены на отечественном производстве. Особенно важно, что в «Норникеле» появится единая база конструкторской документации 3D-моделей запчастей, чтобы пользоваться ей могли все предприятия группы компаний. Таким образом, можно с уверенностью сказать, что будущее производства будет связано с более гибкими и адаптивными процессами.