Одним из широких направлений работы методологии «Производство мирового класса» является устранение причин поломок оборудования. Для этого существуют различные классические подходы по поиску и решению проблем. В современных методологиях бережливого производства в массе используются Кайзены, причинно-следственные диаграммы, анализы Ишикава и многие другие инструменты. В этой статье мы хотим поделиться с особенно объёмной и сложной методикой, называемой «Проект нулевых поломок» (Zero break downs project), а поможет нам разобраться со всеми идеями, заложенными в этот подход, Денис Панюшев — мастер механослужбы ЛПЦ-1.
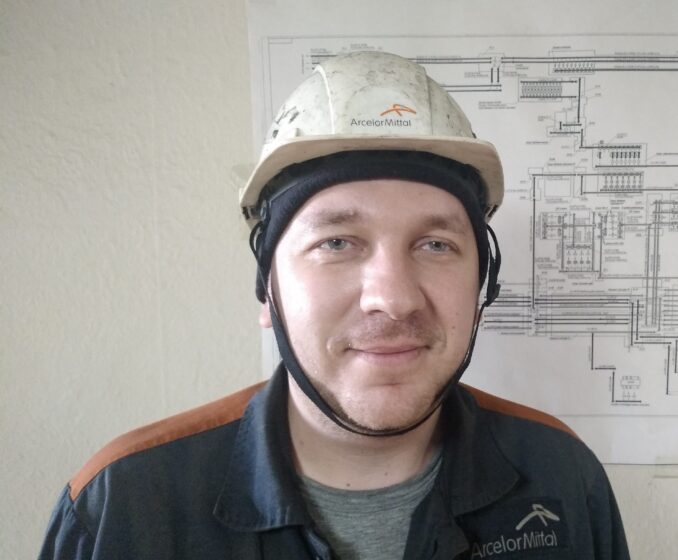
— Денис, расскажите нам, каким образом вы познакомились с методологией разработки проектов нулевых поломок?
— Несомненно, на каждом производстве мы ежедневно решаем задачи по предотвращению выхода из строя оборудования, сокращения скорости ремонтов и повышения качества обслуживания. Но редко кто из нас всерьёз задумывается о причине поломки и, что самое главное, о предотвращении данных событий в дальнейшем. Мы всегда воспринимаем как должное тот факт, что оборудование выходит из строя. Но если попытаться сформулировать иначе, то оно выходит из строя, потому что мы не понимаем, как определить ту критическую точку невозврата, когда оборудование, или узел, перестанет выполнять свою функцию. И вот однажды, собравшись с коллегами и сформулировав данную задачу в отношении шестерённых клетей чистовой группы, мы поняли, что предотвратить проблему, имея необходимые инструменты, это очень интересное мероприятие. Так и получается, что родился проект нулевых поломок, за который мы взялись с целью предотвращения поломок в дальнейшем.
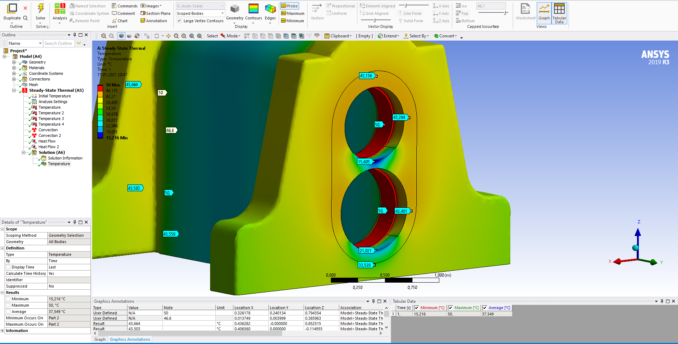
— То есть Вы говорите о способах диагностики и предвосхищения выхода оборудования из строя? Расскажите про проект, какие способы определения проблем на ранней стадии вы нашли?
— Речь идёт не только об инструментальных способах определения неисправностей. В любой ситуации имеются некоторые правила по недопущению, например, аварийных перегрузок, нормы складирования и хранения, консервации запасных частей, наконец. Но если по порядку, то перед нами встал вопрос о нулевых аварийных простоях шестерённых клетей по причине выхода из строя подшипниковых узлов.
Подшипников в клетях по 4 штуки. Мы подняли всю имеющуюся у нас информацию по ремонтам из агрегатных журналов и простоям из базы данных, нанесли для полного понимания картины на карту узлов агрегата и проанализировали данную информацию. Поскольку случаи единичные и происходят достаточно редко, лишь данный подход позволил нам увидеть, что подшипниковые узлы выходят из строя не равномерно по всему агрегату, а, преимущественно, с одной стороны. Это было важным замечанием, которое помогло нам в принятии дальнейших решений в процессе анализа уже реализованных технических решений от производителя оборудования.
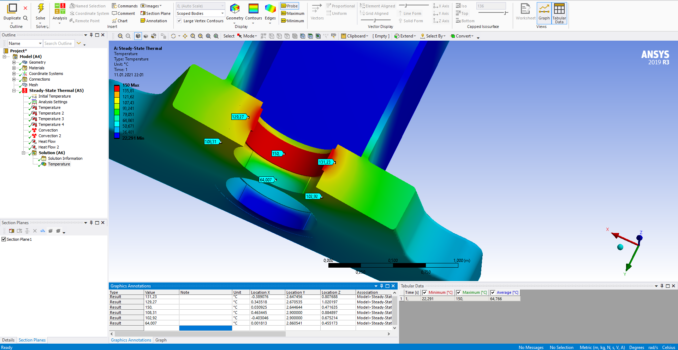
Следующим шагом мы построили диаграмму причинно-следственных связей выхода подшипников из строя. Конечно, нам пришлось изучить, насколько возможно полно, всю сопроводительную документацию по подшипникам, начиная от государственных стандартов и заканчивая расчётами эксплуатационных параметров подшипниковых узлов, вспомогательных систем смазки и охлаждения, и прочие вещи. Когда мы начали работать с цифрами, мы поняли, что общепринятые причины выхода из строя подшипников не работают, поскольку практически все условия, на основании наших вычислений, показывали, что существует более чем 5-ти кратный запас по тем или иным параметрам.
Пришлось детально заниматься инжинирингом, сравнивать оригинальные узлы по проекту и эксплуатируемые сейчас.
— Учитывая, что проект движется дальше, можно сделать вывод, что Вы нашли такие вещи, Денис? Расскажите.
— Ещё бы. Когда дело доходит до понимания причин выхода из строя, когда ты видишь их на чертежах, мне, как механику, становится очень занятно.
Мы обнаружили, что в самый критичный по количеству поломок узел смазка поступает неправильно. В оригинале, когда разрабатывался проект, охлаждение подшипников выполнялось подачей масла сбоку в подушку подшипника. Мимо подшипника, проще говоря. И охлаждение происходило в момент нахождения подшипника в масляной ванне. Но прошло много лет, и мы уже давно используем подшипники с проточкой в середине, другой марки и производителя. Эти подшипники подразумевают подачу масла в проточку и масляной ванны им не хватает для эффективного охлаждения. Было решено пересмотреть чертежи подушек для изготовления других проточек масляных подводов.
Также была поставлена задача диагностировать температуру подшипников во время работы, поскольку режимы работы меняются в широком диапазоне, и мы не имеем представления о реальных условиях эксплуатации данных узлов. Когда же происходит поломка — уже поздно куда-то смотреть. Обратились к термографии — да не тут-то было. Сам агрегат очень массивный и поверхностные температуры не показывают достоверно температуры в охлаждаемых узлах. Нам пришлось прибегнуть к моделированию, статическому термоанализу — модулю ANSYS. Стало понятно, что поверхностно мы увидим изменение температуры очень поздно. Но мы с лёгкостью определили точки, куда легко и с минимальными усилиями мы можем поставить термопары, чтобы оперативно и достоверно получать информацию по температурам подшипников. Сейчас мы планируем закупку приборов КИП и организацию установки данных элементов.
Но самое интересное то, что мы нашли способ определять осевые усилия, действующие на шестерённые клети. Эта тема заслуживает особого внимания, поскольку кроме радиальных нагрузок в редукторе, ему передаются осевые нагрузки с других узлов. И мерить их нечем. Мы связались с фирмой-производителем тензодатчиков KELK и запросили у них рассмотреть возможность изготовления кольцевого тензодатчика, который мы поставим вместо упорного кольца подшипников. В этом узле собирается вся осевая нагрузка с любых осей и, измеряя её, мы сможем диагностировать не только осевое давление на редуктор, но и сигнализировать о неисправностях рабочих клетей, которые приводят к данным последствиям.
Также, пока разрабатывался проект, мы пересмотрели многие другие нормы: складирование, консервация, эксплуатация, очистка перед установкой, контроль давления масла в системе охлаждения и смазки и многие другие вещи. На данном этапе все, кто занимается по данному проекту, имеют настолько богатое представление о данном оборудовании, какого до начала и близко не было.
— Если подытожить, с точки зрения специалиста, как мы понимаем, получилось неплохо?
— Получилось продуктивно. Знаете, когда оцениваешь с одной стороны количество времени, которое мы потратили на ремонты за все эти годы в любую погоду и время суток, а с другой — время, потраченное на решение этой задачи в проекте нулевых поломок, приходишь к выводу, что можно было упростить себе же работу и раньше. Это важно запускать такие проекты и не жалеть время на них, чем потом в десять раз больше проводить на площадке.