«Мы не просто делаем гидроциклоны и сепараторы. Мы выполняем технологические расчеты, чтобы понять, как использовать оборудование максимально эффективно, какие параметры для этого необходимы. Это позволяет нашим заказчикам достигать наилучших результатов», — говорит директор ООО «Русмайн Инжиниринг» Андрей Сергеевич Бучатский.
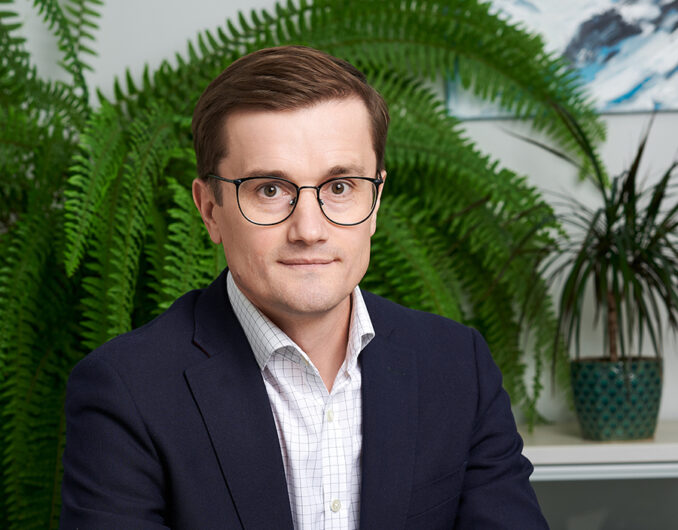
Rusmine Engineering/«Русмайн Инжиниринг» создана в 2003 году под названием «САТЕЛЛИТ» и до 2014-го занималась поставками зарубежного оборудования для горнодобывающей промышленности.
В 2014-м на предприятии разработана первая батарея гидроциклонов, а в 2016-м выпущена первая партия сепараторов MAGNIS. Из чисто коммерческой организация трансформировалась в производственную. Именно это ее руководители считают главным достижением за 18 лет работы.
В 2021 году компания переименована в «Русмайн Инжиниринг» (Rusmine Engineering).
— Андрей Сергеевич, почему в компании было принято решение о запуске собственного производства?
— Думаю, это просто новый этап эволюции предприятия. К 2014-му мы успели накопить достаточно опыта, чтобы разрабатывать оборудование самостоятельно.
Была сформирована команда специалистов, способных эффективно решать различные задачи в сфере обогащения полезных ископаемых. У нас работает известный специалист в сфере обогащения угля Александр Данилович Полулях, доктор наук, профессор. Он руководит отделом разработки технологий обогащения, где трудится его сын, Данил Александрович Полулях, кандидат технических наук, — отличный технолог и тоже признанный профессионал в своей сфере. Из 30 сотрудников «Русмайн Инжиниринг» большая часть входит в конструкторскую группу, которая занимается расчетами обогатительного оборудования и разработкой документации для производства.
Мощным внешним стимулом к организации собственного производства стал экономический кризис 2014 года. Дело в том, что в начале своей работы мы пытались сотрудничать с российскими производителями обогатительного оборудования. Но это оказалось крайне сложно: люди срывали сроки, получали деньги и пропадали. Это заставило нас обратить внимание на китайский рынок. И здесь мы нашли взаимопонимание: заказы выполнялись в срок, на хорошем уровне.
В 2014-м из-за падения рубля по отношению к доллару стоимость оборудования, которое закупалось в Китае, для нас просто удвоилась. А поскольку мы не могли отменять обязательства перед своими заказчиками, приходилось работать в убыток.
«Русмайн Инжиниринг» — единственная компания, выпускающая комплексы для магнитной рудоразборки. Аналогов такого оборудования у других производителей нет — ни в России, ни за рубежом
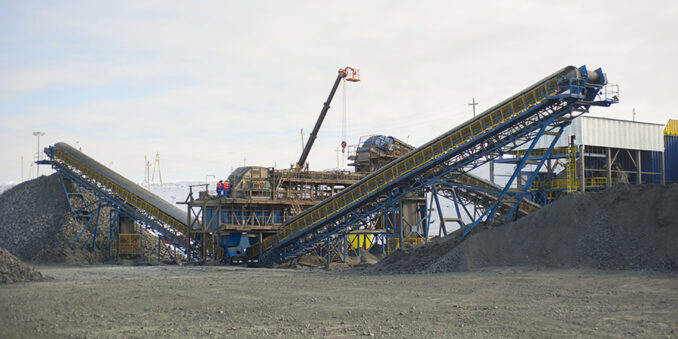
Кризис показал, что такая зависимость от зарубежных поставок очень опасна. Есть риски, которые мы контролировать не можем. Тогда и было принято решение производить оборудование самостоятельно — разрабатывать и выпускать его в России.
В 2014 году компания стала резидентом промышленного парка «Северный». И в 2016-м запустила свой производственный цех. В 2018-м мы построили здесь же офис и переехали в него.
— С какими проблемами пришлось столкнуться при организации производства горно-обогатительного оборудования? Как они решались?
— Само создание горно-обогатительного оборудования очень сложный процесс. Необходимо учитывать множество факторов: технологические параметры, гранулометрический состав материала и другие. На проведение расчетов уходит много времени, сил. Очень высок уровень ответственности за точность этих расчетов, которая подтверждается в дальнейшем при эксплуатации оборудования в реальных условиях на фабрике.
Другая сложность заключается в том, что производство несерийное. Руда и уголь на разных месторождениях настолько отличаются, что постоянно требуется вносить изменения, подстраивать конструкцию под требования фабрики. Каждый проект индивидуален.
Кроме того, данное оборудование эксплуатируется в очень жестких условиях, со значительным абразивным износом. Поверхности очень быстро изнашиваются. Важно обеспечить надежную защиту. Для этого мы используем современные дорогостоящие материалы — футеровку из самосвязанного карбида кремния и плитку из оксида алюминия. Подгоняем их без зазоров, ведь в малейшую щель сразу же проникают абразивные частицы перерабатываемых минералов — оборудование приходит в негодность. И мы успешно справляемся с этой задачей.
— Какое оборудование сегодня производит «Русмайн Инжиниринг»?
— В углеобогащении мы предлагаем ключевое оборудование для обогащения угля в тяжелых средах. Это гидроциклоны — сердце углеобогатительной фабрики.
Обогатительные и классификационные гидроциклоны производятся под нашей собственной маркой Wermax, зарегистрированной в 2018 году. Под этой же маркой выпускаются износостойкий компаунд WERMAX PROTECT, шнеки к фильтрующим центрифугам Н-900 под маркой WERMAX SCROLL.
Другое предложение — магнитные сепараторы для регенерации тяжелой среды под маркой MAGNIS. Они применяются для регенерации железорудного концентрата при обогащении в тяжелых средах и позволяют свести потери дорогостоящего компонента практически к нулю.
Еще один наш продукт — оборудование для сухой магнитной сепарации железной руды. Сепараторы MAGNIS способны перерабатывать до 1 000 тонн руды в час.
— Предлагает ли ваша компания оборудование, которого нет у других производителей?
— Наша компания на сегодняшний день единственная, выпускающая комплексы для механизированной магнитной рудоразборки. Аналогов такого оборудования у других производителей нет — ни в России, ни за рубежом.
Оно устанавливается прямо в карьере, где добывается железная руда. И позволяет уже на этом этапе отделять пустую породу от содержащей железо руды. Пустая порода остается в карьере. Соответственно, исключаются затраты на ее транспортировку вместе с рудой на обогатительную фабрику, уменьшается износ оборудования, сокращается объем отходов. Все это позволяет экономить сотни миллионов рублей в год и положительно сказывается на рентабельности производства.
Два комплекса магнитной рудоразборки работают в «Северстали». Есть договоренность о поставке третьего. Еще два комплекса установлены на Кимкано-Сутарском ГОКе на месторождении компании «Петропавловск ЧМ».
Что касается гидроциклонов для угольной промышленности, то, если сравнивать с другими российскими компаниями, мы не просто делаем гидроциклон. Мы выполняем технологические расчеты, чтобы понять, как использовать его максимально эффективно, какие параметры для этого необходимы. Это позволяет нашим заказчикам достигать наилучших результатов.
Такой комплексный подход ставит нас на уровень западных производителей. Но по сравнению с ними наша продукция стоит в два-три раза дешевле.
— Какие выгоды, кроме более низкой стоимости оборудования, получили ваши постоянные заказчики от запуска компанией собственного производства?
— Приобретать оборудование, произведенное в России, надежнее, чем в других странах. Например, сейчас, в ситуации пандемии, всегда присутствует вероятность, что закроют границу с Китаем или другими государствами.
У нас же есть все необходимые комплектующие в достаточном объеме, чтобы продолжать изготавливать оборудование, не нарушая сроков поставок. Мы постоянно заботимся о пополнении запасов, покупаем комплектующие заранее. Даже если границы России закроют, мы сможем работать в прежнем режиме.
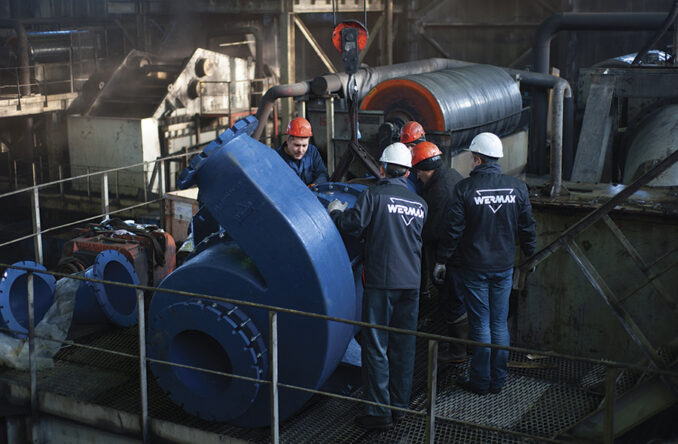
— Кроме изготовления и продажи оборудования, «Русмайн Инжиниринг» предлагает также широкий спектр инжиниринговых услуг. Что включает этот перечень?
— Мы разрабатываем технологические регламенты обогащения по проектной документации. Выполняем аудит технологии углеобогатительных фабрик и сопутствующего производства. Предоставляем услуги по автоматизации оборудования для обогащения.
Проводим комплексное обследование регенерации магнетита на углеобогатительных фабриках: мы в этом хорошо разбираемся. На фабрику выезжает группа специалистов, выявляет, где происходят потери, и разрабатывает методику устранения.
Инжиниринговое направление в компании сейчас активно развивается. В 2020 году подписан контракт на разработку технологии сухого магнитного обогащения железной руды для подразделения «Северстали». До конца 2021-го проект будет завершен, оборудование будет запущено.
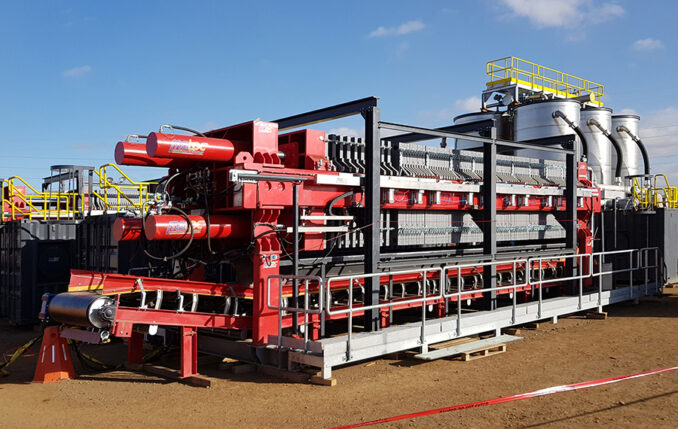
— В 2020 году компания стала дилером итальянского завода – изготовителя камерных фильтр-прессов MATEC. Какие возможности это дает вашим заказчикам?
— Мы решили расширить линейку оборудования для обогатительных производств за счет камерных фильтр-прессов. Сегодня это один из самых эффективных способов обезвоживания.
Долго и тщательно выбирали партнера и остановились на итальянской компании MATEC. На наш взгляд, сегодня это наиболее эффективное оборудование на рынке. Италия — один из признанных лидеров в области фильтрации. В этой стране тысячи лет обрабатывают мрамор и хорошо научились очищать воду от мраморной крошки и пыли.
По соглашению с MATEC в декабре 2020 года мы привезли в Россию лабораторный фильтр-пресс. По параметрам работы он абсолютно идентичен промышленной установке, но в десятки раз меньше по размеру. Для получения кека достаточно 5 кг шлама. Это дает возможность провести полноценные испытания, чтобы подобрать оптимальный вариант оборудования для обезвоживания конкретного продукта.
Лабораторный фильтр-пресс можно легко транспортировать, перемещая его на обогатительную фабрику. Здесь он устанавливается в технологический процесс и подключается. Клиент может своими глазами увидеть, что получит, применяя фильтр-пресс MATEC.
Такую работу мы уже провели на одном из предприятий в России, сейчас испытания идут на другой фабрике.
— Какие предприятия входят в пул ваших постоянных заказчиков?
— Все лидеры горнодобывающей отрасли России. Свою первую сделку мы заключили с «Северсталью», и сейчас эта компания остается одним из наших ключевых клиентов. Вот уже 18 лет мы работаем бок о бок.
В числе наших заказчиков «Мечел» (все производственные подразделения этой компании), «Евраз», СУЭК, СДС и другие крупные горнодобывающие предприятия.
Основное направление нашей работы — обогащение угля. Но во время прошлогоднего кризиса в этой сфере мы значительно расширили свои возможности: получили новых заказчиков среди железорудных производств.
— Как резкий спад в угольной промышленности из-за снижения цен на уголь в 2020-м отразился на вашей компании?
— Количество заказов резко сократилось. Но мы работаем с 2003 года и уже проходили кризисы 2008-го и 2014-го. Это дало нам понимание, что, раз заказов немного, нужно сосредоточиться на повышении эффективности собственной деятельности, навести порядок внутри компании. Этим мы успешно занимались в прошлом году.
— Какие планы у компании на 2021 год и ближайшую перспективу?
— Сейчас мы ощущаем рост спроса на рынке добычи и переработки полезных ископаемых. И готовы его удовлетворить. Горнодобывающие компании вернулись к проектам, замороженным в прошлом году, и запускают много новых.
В 2021 году планируем работать по уже имеющимся заказам, брать новые и начать выпуск нового оборудования для переработки полезных ископаемых. Максимальные усилия направим на развитие конструирования и производства.
В 2022-м намерены вывести на рынок принципиально новое оборудование, о котором будет повод поговорить в следующем году.
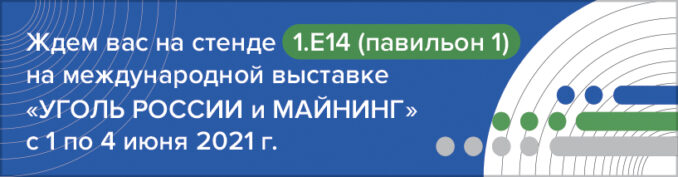
308010, Белгородская область, Белгородский район, пос. Северный, ул. Березовая, зд. 3, стр. 3
Тел.: +7 (4722) 20-55-30,
e-mail: info@rusmine.com