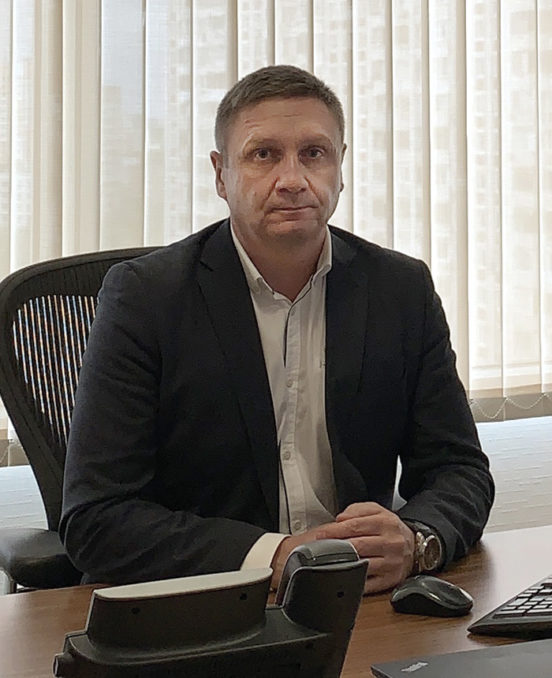
Оператором проекта освоения Удоканского месторождения меди является ООО «БГК», входящее в многопрофильную группу компаний USM. Проект реализуется в соответствии с требованиями лицензии, выданной в 2008 году. Участок недр находится в Каларском районе Забайкальского края, является крупнейшим в России и одним из крупнейших в мире неразработанным месторождением меди.
Финансирование проекта осуществляется за счет собственных средств учредителей компании и кредитных средств.
Настоящая статья основана на материалах проектной документации, получившей положительные заключения государственных экспертиз (государственной и государственной экологической), то есть прошедшая всесторонний анализ экспертами ФГУ «Главгосэкспертиза России» и Росприроднадзора. Кроме того, проектные решения апробированы в рамках многочисленных лабораторных исследований и промышленных испытаний, защищены в Центральной комиссии по разработке месторождений твердых полезных ископаемых, а также рассматривались рядом признанных в мире консалтинговых компаний и коммерческих банков.
Горно-геологические особенности
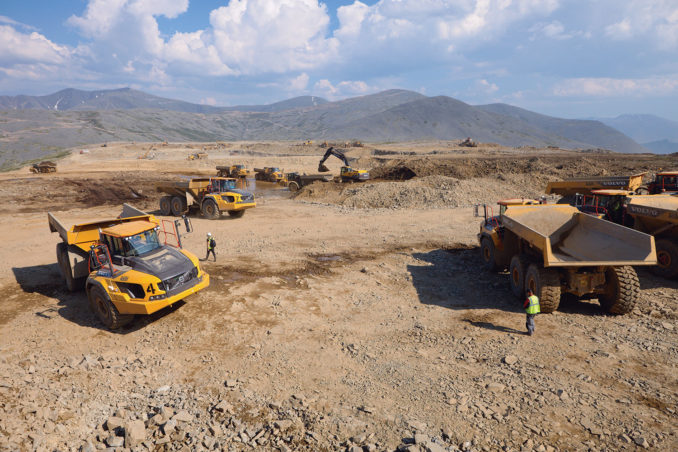
По геологическим особенностям и характеру распределения полезных компонентов Удоканское месторождение меди отнесено ко II группе сложности строения в соответствии с классификацией запасов месторождений твердых полезных ископаемых (протокол ГКЗ СССР № 4489 от 30.12.64).
Территория характеризуется резко континентальным климатом, сложным рельефом, развитой речной сетью, высокой сейсмической активностью и активной неотектоникой, сплошным распространением многолетней мерзлоты значительной мощности, сложными условиями обводненности.
Удоканское месторождение меди является стратиформным, образовано медистыми песчаниками и сланцами, включает участки с богатыми (> 2 % Cu) и бедными (<1 % Cu) рудами.
По преобладанию минеральных форм меди на Удоканском месторождении выделены три основных природных разновидности руд: халькозин-борнитовая, брошантит-малахитовая, халькопирит-пиритовая.
Руды характеризуются преимущественно средней степенью окисления, причем среди окисленных минералов преобладают трудноизвлекаемые гидроксил-сульфаты, что является уникальной особенностью Удоканского месторождения. К таким минералам, в частности, относится брошантит.
Характер минерализации по участкам месторождения свидетельствует о крайней неравномерности содержания меди и ее окисленности в толще оруденения. В результате тектонических явлений и большой сейсмичности распределение окисленных руд крайне неравномерно как по глубине, так и по простиранию рудных тел месторождения: фиксируются все технологические сорта руд, от чисто сульфидных до полностью окисленных. Постепенных переходов не отмечается, наоборот, переходы от сульфидных руд к окисленным резкие (см. табл. 1).
Анализ горно-геологических и горнотехнических условий залегания рудных тел, выход рудных тел на дневную поверхность, повышенная устойчивость руды и вмещающих пород, а также значительная глубина минерализации предопределяют применение комбинированного (открыто-подземного) способа разработки месторождения.
С учетом сложных геологических, географических условий, оценки рынка сырья ООО «БГК» был определен порядок освоения Удоканского месторождения, который предусматривает выделение I очереди разработки месторождения с объемом переработки 12 млн т руды в год.
I очередь предполагает разработку Удоканского месторождения в пределах Западного карьера — основного эксплуатационного участка, обеспечивающего до 70–80 % производительности по добыче руды.
Технологическая схема
Результаты ранее проведенных исследований

Технологические исследования по обогащению руд Удоканского месторождения были начаты в 1952 году и проводились многими научно-исследовательскими институтами. С 1952 по 1988 год, кроме геологических проб, были выполнены исследования на более чем 500 малых технологических пробах, 56 лабораторных технологических пробах массой по 1 000 кг и 12 полупромышленных пробах массой по 300–500 т каждая. Кроме лабораторных, укрупненно-лабораторных исследований проводились и полупромышленные испытания.
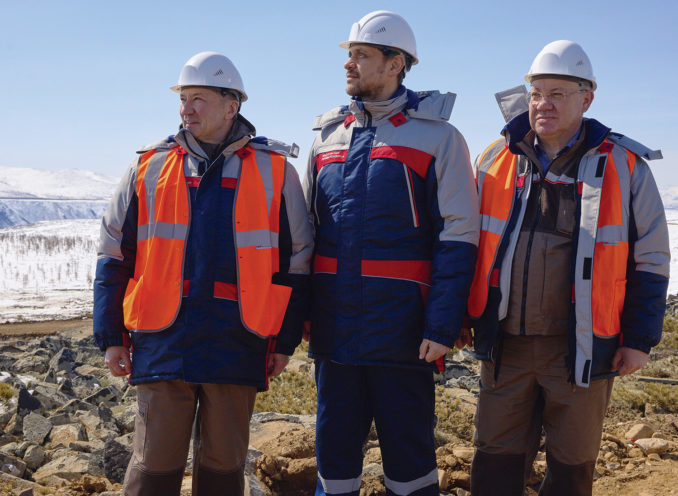
Исследования обогатимости проб руды Удоканского месторождения проводились ведущими научно-исследовательскими институтами: Механобр, Гинцветмет, ЦНИГРИ, Иргиредмет.
В конце 70-х годов институтом «Механобр» была выполнена комплексная программа испытаний руды Удоканского месторождения, как лабораторных испытаний в периодическом режиме, так и опытно-промышленных. Все испытания проводились с использованием флотационной технологии. В ходе исследований, выполненных Механобром, были проведены тесты на пробах, отобранных с разных участков, с различной степенью окисления минералов меди.
Однако только флотационными методами не удавалось достичь высоких результатов при обогащении смешанных и окисленных руд.
С 1980 по 1985 год в институте «Гинцветмет» проводились полупромышленные испытания по сернокислотному выщелачиванию меди из труднофлотируемых, с повышенным содержанием окисленных минералов руд Удоканского месторождения с выделением меди из растворов сорбцией или экстракцией.
В 1984 году институтом «Гинцветмет» была изучена возможность переработки медного концентрата гидрометаллургическими методами. Коллективный концентрат подвергался атмосферному выщелачиванию, после чего кек выщелачивания подвергался флотационному обогащению с получением товарного сульфидного концентрата.
Проведенные исследования подтвердили возможность применения атмосферного выщелачивания коллективных концентратов, извлечение окисленной меди из которых составляло 97–98 %.
В 1995 году компаниями «Минпрок» (Австралия), «Институт «Гипроцветмет» (Россия) и АООТ «Институт Механобр» (Россия) подготовлено технико-экономическое обоснование строительства горно-металлургического комбината на производительность 7,5 млн т/год.
В технологической схеме, принятой в ТЭО в 1995 году, было предусмотрено выщелачивание коллективного концентрата, кек выщелачивания подвергался нейтрализации, после чего из этого кека путем флотации получали сульфидный концентрат с содержанием 30 %. Из раствора выщелачивания методами жидкостной экстракции и электроэкстракции получали катодную медь.
В рамках программы испытаний, выполненной в МИСиС в 2000–2001 годах, были выполнены исследования по прямому выщелачиванию исходной руды. Технологическая схема, разработанная МИСиС, преду-сматривала дробление руды до крупности 100 % -3 мм, выщелачивание тонкодробленой руды с последующей экстракцией и электроэкстракцией (SX-EW) для получения катодной меди, нейтрализацию и доизмельчение кека с последующим получением сульфидного флотационного концентрата с содержанием меди 30 %. На основе технологического регламента МИСиС институтами «Гипроцветмет» и «Механобр» в 2001 году разработано технико-экономическое обоснование строительства горно-металлургического комбината на производительность 9,0 млн т/год. Разработанная технология была испытана в лабораторном масштабе.
В 2006 году по проекту институтов «Гипроцветмет» и АООТ «Механобр инжиниринг» была введена в эксплуатацию опытно-промышленная фабрика в п. Удокан производительностью 1,5 т/час по исходной руде, что позволило выполнить большой объем полупромышленных и лабораторных исследований. На опытно-промышленной фабрике предусматривалась возможность проведения исследований как по флотации, гидрометаллургической переработке концентратов, так и опыты по прямому выщелачиванию исходной руды, кучному выщелачиванию, гравитационному обогащению.
На ОПК были проведены испытания технологии как прямого выщелачивания исходной руды с последующей флотацией сульфидных минералов, так и технологии флотационного обогащения с последующим выщелачиванием коллективного концентрата, а также их модификаций в полупромышленном масштабе. Многочисленные попытки проведения полномасштабных испытаний по технологии прямого выщелачивания тонкодробленой руды не были успешными из-за аппаратурных проблем: нестабильная работа каскада выщелачивания руды, плохая работа узла фильтрации пульпы после выщелачивания.
С целью разработки оптимальной технологии переработки руд Удоканского месторождения ООО «БГК» был выполнен большой объем дополнительных исследований:
2009 год — исследования по определению индексов работы дробления и шарового измельчения, опыты по флотации руды с включением операции скоростной флотации, с применением различных видов собирателей и сульфидизаторов;
2010 год — опытно-промышленные испытания по селективной флотации сульфидных и окисленных минералов. В рамках испытаний наработано более 30 т сульфидного и окисленного концентратов для после-дующих исследований;
2011 год — опытно-промышленные испытания гидрометаллургических процессов переработки концентратов Удоканского месторождения;
2011 год — исследования по определению возможности предварительного крупнокускового обогащения руд Удоканского месторождения;
2011–2013 годы — программа лабораторных исследований с целью выбора оптимальной технологической схемы для последующего проектирования. В рамках программы проведены исследования по дроблению и измельчению руды, флотации, атмосферному и автоклавному выщелачиванию, сгущению и фильтрации. Выполнено технологическое картирование на 503 пробах;
2011–2013 годы — испытания по кучному выщелачиванию. В рамках испытаний переработано около 70 т руды;
2012 год — технологические исследования по возможности применения атмосферного выщелачивания сульфидного концентрата;
2012 год — оценка контрастности гравитационных свойств двух проб руды Удоканского месторождения меди с целью обоснования гравитационного концентрирования минералов меди и железа;
2012 год — компанией Bateman был выпущен отчет по обоснованию проекта освоения Удоканского месторождения по гидрометаллургической — флотационной схеме;
2012–2013 годы — работы по оценке возможности переработки концентратов Удоканского месторождения пирометаллургическими способами;
2012–2013 годы — исследования по гидрометаллургическому извлечению серебра из сульфидных концентратов Удоканского месторождения;
2013 год — компанией Flour был выполнен технико-экономический расчет «Сравнение технологических схем производства катодной меди и концентратов» по оценке существующих технологических схем переработки руды;
2014 год — на основании сводных данных, полученных по результатам лабораторных и полупромышленных испытаний, был разработан технологический регламент переработки руд Удоканского месторождения Институтом ТОМС.
Основные заключения по результатам ранее проведенных исследований
Руды Удоканского месторождения являются уникальными по объему запасов и своим минералогическим характеристикам, поэтому ни на территории современной России, ни в других странах нет пред-приятий, которые могли бы послужить прямыми аналогами для объективной сравнительной оценки.
Указанные выше особенности руд Удоканского месторождения не позволяют применять к ним традиционные способы обогащения и металлургической переработки. Так, высокое содержание кремнезема (63–78 %) не позволяет применять пирометаллургические процессы, а присутствие в значимых количествах соединений кальция, калия и натрия делает нецелесообразным выщелачивание всего объема руды.
Традиционные схемы гравитационного обогащения также не являются достаточно эффективными, поскольку гравиообогащение ориентировано на контрастность плотностных характеристик ценных компонентов и минералов пустой породы, которой в удоканских рудах не наблюдается.
Флотационные схемы обогащения, реализованные на медных обогатительных фабриках, перерабатываю-щих сульфидные руды, также малоэффективны для переработки руд Удоканского месторождения. При использовании реагентных режимов, традиционных для флотации сульфидов, высокая доля окисленных минералов меди в удоканской руде не позволит достичь высокого извлечения меди в концентрат. Применение сульфидизации поверхности окисленных минералов также не обеспечит высокого качества медного концентрата (≥ 25 %), достаточного для его традиционной переработки на плавильных заводах.
Для переработки неординарных удоканских руд разработана нестандартная технология, которая, с одной стороны, позволяет эффективно справляться с технологическими особенностями, такими как окисленность медных минералов, а с другой — использовать присущий удоканским рудам уникальный минералогический состав.
В частности, на основании выполненных исследовательских и проектных работ для переработки руд была выбрана новая технологическая схема — флотационное обогащение руды с получением коллективного концентрата, его атмосферное выщелачивание и флотация кека выщелачивания с выделением сульфидного медного концентрата. Указанная технологическая схема запатентована ООО «Байкальская горная компания».
Данная схема в качестве головной операции предусматривает коллективную флотацию с формированием коллективного концентрата, в который на первой стадии коллективной флотации извлекаются преимущественно сульфидные минералы меди, а на второй — окисленные минералы.
Технологическая схема, сочетающая процессы флотации и атмосферного выщелачивания, обеспечивает производство катодной меди на участке жидкостной экстракции/электролиза и сульфидного концентрата с содержанием меди 45 % путем флотации кека выщелачивания.
Для подтверждения показателей переработки руды была выполнена программа исследований, в том числе опыты в замкнутом цикле и полупромышленные испытания.
В период с 2013 по 2014 год на ОПК в п. Удокан был проведен ряд лабораторных и полупромышленных испытаний, а также исследований по определению степени изменчивости технологических свойств руды (технологическое картирование).
1. Лабораторные исследования для подтверждения технологической схемы флотационного обогащения
Технологические испытания проводились на пробах, сформированных из отдельных проб с различной степенью окисленности, и представляли основные участки Удоканского месторождения.
Пробы 3 и 4 представлены рудами средней окисленности, но с различным содержанием общей меди, проба 7 представляла сульфидный сорт руды, проба 8 — окисленный сорт руды (табл. 2).
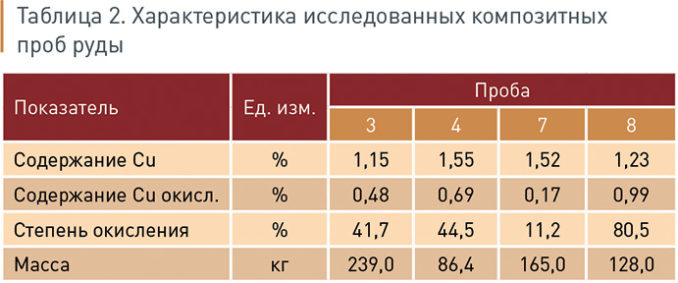
Были проведены исследования для определения оптимального выхода коллективного концентрата. Зависимость извлечения меди в коллективный концентрат от выхода коллективного концентрата представлена на рис. 1.
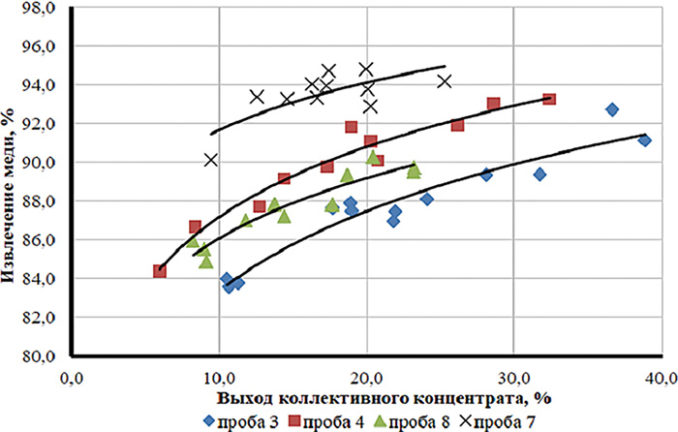
На графике видно, что с увеличением выхода коллективного концентрата растет извлечение меди. Кривые, описывающие извлечение меди, имеют практически одинаковый угол наклона. Представленные данные свидетельствуют о том, что для всех проб с увеличением выхода концентрата наблюдается практически одинаковый прирост извлечения.
Исследования показывают, что оптимальным выходом коллективного концентрата является -20 ± 5 %.
Разработанная схема коллективной флотации позволяет перерабатывать практически все технологические типы удоканских руд (сульфидные, смешанные, окисленные) с достаточно высокими показателями.
2. Лабораторные исследования по определению вариабельности технологических свойств руды (технологическое картирование)
В рамках технологического картирования было сформировано 157 проб, которые охватывали диапазон содержаний меди от 0,10 до 6,43 %, при этом степень окисления медных минералов варьировалась от 1 до 96 %. Отобранные пробы покрывали практически всю разведанную территорию месторождения.
Технологическое картирование всех 157 проб выполнено по флотационно-гидрометаллургической схеме.
Результаты выполненного технологического картирования продемонстрировали большой разброс извлечения меди в коллективный концентрат (рис. 2). С увеличением степени окисления извлечение меди снижается и увеличивается вариативность показателей.
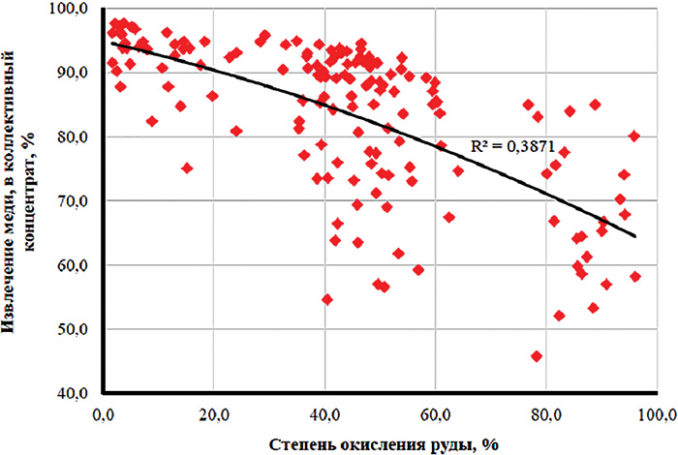
Опыты по атмосферному выщелачиванию коллективного концентрата для проб руды с содержанием окисленной меди более 0,3 % показали стабильно высокое извлечение меди в раствор при атмосферном выщелачивании (95–99 %) из коллективного концентрата вне зависимости от типа руды.
На основе результатов флотационных тестов в замкнутом цикле и оценки изменчивости техноло-гических свойств руды для трех основных типов — сульфидного, оксидного и смешанного были разработаны корреляционные зависимости извлечения меди и серебра от их содержания в руде.
3. Полупромышленные испытания
В 2013 и 2014 годах на опытно-промышленном комплексе Байкальской горной компании были проведены полупромышленные испытания технологической схемы переработки руды месторождения Удокан. Испытания 2013 года были проведены с целью получения технологических показателей флотационно-гидрометаллургической технологической схемы. В 2014 году в ходе полупромышленных испытаний проводилось подтверждение и уточнение показателей и режимных параметров.
Полупромышленные испытания флотационно-гидрометаллургической схемы проводились в непрерывном режиме при производительности по исходной руде 1,0–1,5 т/ч. Общая масса испытанных проб составила около 850 т.
Испытания проводились на пробе руды, отобранной с участка Медный, который характеризует руду за весь период отработки месторождения. Представительность отобранной пробы была установлена по следующим основным показателям: содержание меди, минеральный и химический состав — и подтверждена специалистами российских и зарубежных организаций (см. табл. 3).
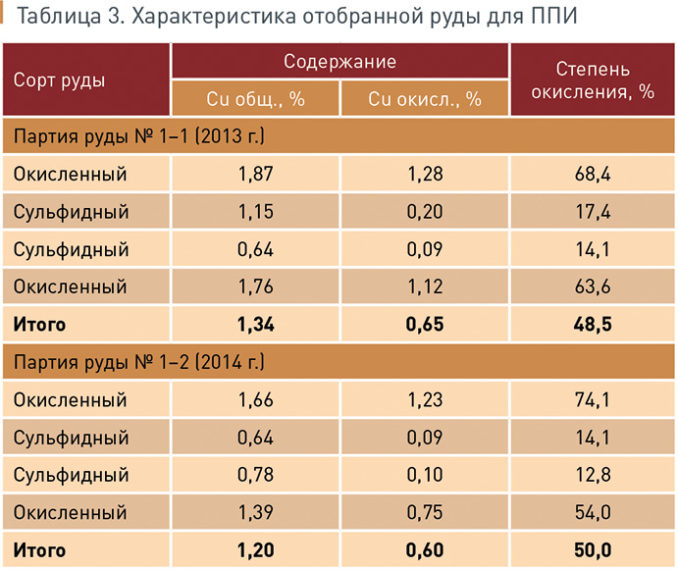
По результатам опробования технологической схемы коллективной флотации за весь период полупромышленных испытаний определена зависимость извлечения меди от выхода коллективного сульфидно-окисленного концентрата (рис. 3).
При проведении полупромышленных испытаний достигнуты стабильные показатели по степени извлечения меди в коллективный сульфидно-окисленный флотационный концентрат на уровне 88,27–89,55 % при его выходе 19–22 %.
Полученные показатели в цикле атмосферного выщелачивания коллективного концентрата подтвердили высокую эффективность сернокислотного выщелачивания окисленных минералов меди, извлекается 96,3–98,4 % окисленной меди от поступающей с коллективным концентратом.
В 2017 году в рамках договора, заключенного Байкальской горной компанией с компанией Outotec, в лаборатории «Механобр Инжиниринг» были проведены исследования по сравнению различных схем обогащения с целью подтверждения и определения возможностей улучшения технологии обогащения и гидрометаллургической переработки руды Удоканского месторождения.
Были выполнены опыты в открытом и замкнутом циклах, а также имитационное моделирование для вариантов селективной флотации сульфидных и оксидных минералов меди. Рассмотрены варианты получения «богатых» сульфидного и оксидного концентратов, а также вариант получения «богатого» сульфидного и «бедного» оксидного концентратов, был также рассмотрен вариант с удалением шламов после первой стадии измельчения и межцикловой флотацией.
В результате опытов были получены селективные сульфидный и оксидный концентраты с содержанием меди в сульфидном концентрате 35,49–36,94 %, в оксидном «богатом» концентрате — 22,51 %, в оксидном «бедном» концентрате — 4,81 % при суммарном извлечении от 87,75 до 91,92 %.
Предлагаемый Outotec технологический процесс включал получение раздельных сульфидного и оксидного концентратов, их атмосферное выщелачивание, дополнительное автоклавное выщелачивание для переработки халькопирита и производства серной кислоты, извлечение меди из растворов по технологии SX-EW.
Опыты по атмосферному выщелачиванию показали, что извлечение меди из концентратов находится на уровне 97 %, а при автоклавной переработке извлечение составляет 99 %.
В сентябре 2018 года были проведены полупромышленные испытания на опытно-промышленном комплексе в п. Удокан по проектной технологической схеме полного цикла с получением продуктов переработки катодной меди и сульфидного концентрата с целью подтверждения проектных показателей. К участию в полупромышленных испытаниях были приглашены международные поставщики оборудования и специалисты проектных и научных институтов, независимых международных консалтинговых компаний, таких как Outotec, FLSmidth, IMC Montan, «Механобр», НИПИИ ТОМС и др. Все участники подтвердили, что результаты испытаний говорят о достижимости проектных показателей технологической схемы.
Приведенный обзор результатов исследований, выполненных за последние 67 лет, показывает достаточную изученность технологических свойств руд Удоканского месторождения. Были исследованы всевозможные варианты технологии переработки сульфидных, окисленных и смешанных руд. Рассмотрены варианты как чисто флотационных методов обогащения с последующей гидрометаллургической и пирометаллургической переработкой концентратов, так и различные варианты комбинированной технологии, сочетающей флотационные методы и гидрометаллургические процессы.
Исследованы возможности кучного и бактериального выщелачивания исходной руды, возможность предварительного гравитационного обогащения.
На опытно-промышленном комплексе ООО «БГК» с 2006 года по настоящее время были отработаны различные варианты технологии переработки руд Удоканского месторождения меди и подтверждены проектные показатели.
Выполненный анализ существующих схем переработки руд Удоканского месторождения позволяет утверждать, что наибольшей степенью технической проработки на сегодняшний день обладает вариант с получением коллективного концентрата, его выщелачиванием в атмосферных условиях с получением медьсодержащего раствора и его переработкой по технологии SX-EW с производством катодной меди, флотации кека выщелачивания с формированием товарного сульфидного концентрата, содержащего 40–45 % меди.
В конце 2018 года было получено положительное заключение ФАУ «Главгосэкспертиза России» на проект «Горно-металлургический комбинат «Удокан». I очередь строительства на производительность 12,0 млн т руды в год». Расчет экономической эффективности проекта показал его привлекательность для инвестирования.
Выводы
Таким образом, ООО «Байкальская горная компания» совместно с крупнейшими проектными и научными институтами, независимыми международными консалтинговыми компаниями и поставщиками оборудования выработала в рамках проектирования технические и технологические решения, которые позволят реализовать строительство горно-металлургического комбината в значительной удаленности от крупных населенных пунктов, в сложных горно-геологических, географических и климатических условиях. При этом проект предусматривает высокую экономическую эффективность.