Токаев Александр Сергеевич, Данилов Станислав Юрьевич
В горнорудной, генерирующей, нефтегазовой промышленности в последние годы особенно остро стоит вопрос эффективной эксплуатации парка динамического оборудования, обеспечивающего технологический процесс на предприятиях. Важнейшим инструментом контроля и прогнозирования технического состояния динамического оборудования являются системы виброконтроля и вибродиагностики, позволяющие определять конкретные дефекты и степени их развития и тем самым существенно снижать издержки на аварийные остановы, техническое обслуживание и ремонт, а также объективно и автоматически оценивать качество ремонтов.
Автоматизированные системы контроля вибрации и диагностики являются специализированным подклассом автоматизированных систем (АС) в промышленности и представляют собой программно-аппаратные комплексы, состоящие из датчиков, устанавливаемых на агрегат, аппаратуры оцифровки сигналов с датчиков, серверов и программного обеспечения. Исторически функция обработки колоссального объёма информации, имеющегося в вибрационных сигналах, была распределена по локальным контроллерам, которые имеют крайне ограниченные возможности по обработке данных и в полной мере не готовы к современным задачам по внедрению нейросетевой вибродиагностики.
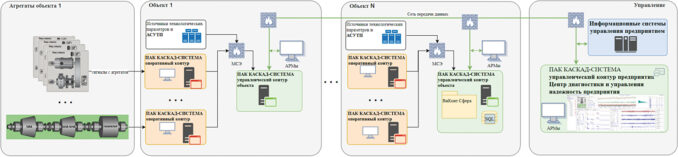
Поскольку центральным элементом таких систем являются данные и возможности системы по их обработке, в разработанной резидентом «Сколково» АСКВД (автоматизированной системе контроля вибрации и диагностики) нового поколения реализована уникальная технология разметки и обработки данных, в частности, вся обработка всех данных, в том числе и сигналов в реальном времени, реализована в программном обеспечении, располагаемом на серверах заказчика.
Почему это так важно и является ключевым элементом АСКВД? Для таких систем свойственно итеративное развитие в цикле — накопление данных, выявление в данных новых зависимостей и признаков дефектов, реализация автоматического вычисления признаков с помощью алгоритмов и/или внедрения и обучения нейросетей, обработка старых данных с учётом новых знаний, верификация результата. В решении резидента «Сколково» добавление нового функционала с учётом новых знаний на основе анализа больших данных происходит без изменения аппаратной части. Это позволяет экономически и физически эффективно развивать и масштабировать решение на предприятии.
Рассмотрим работу системы и её возможности на реальных кейсах промышленных предприятий.
Пример № 1.
Выявление развивающегося дефекта
Беспроводной вариант системы установлен на 16 агрегатах золотоизвлекающей фабрики. Агрегаты представляют собой электродвигатели, сопряжённые с насосами или перемешивающими устройствами. В оснащении предусмотрен в том числе модуль автоматической диагностики со следующим набором детектируемых дефектов, их локализацией и степенью развития:
1) дисбаланс;
2) расцентровка;
3) ослабления;
4) нарушения опирания;
5) дефекты электромагнитной
системы;
6) дефекты проточной части;
7) дефект лопастного аппарата;
8) дефект редуктора;
9) дефекты подшипников качения.
Сводная мнемосхема приведена на рис. 2.
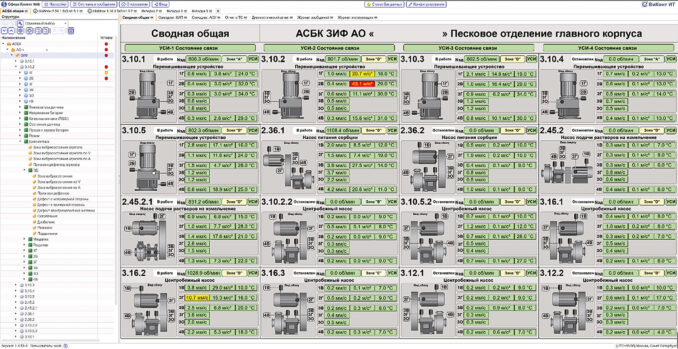
В ходе своей работы система автоматически выявила целый ряд дефектов. Остановимся на одном из типичных. Один из агрегатов при вводе системы в эксплуатацию находился в удовлетворительном состоянии, однако после очередного пуска система сигнализировала о проявлении дефекта наружного кольца подшипника электродвигателя. С течением времени дефект проявлялся всё чаще, о чём свидетельствовали сообщения и тренды системы, по которым можно было наблюдать, что ситуация ухудшается. Примеры трендов приведены на рис. 3.
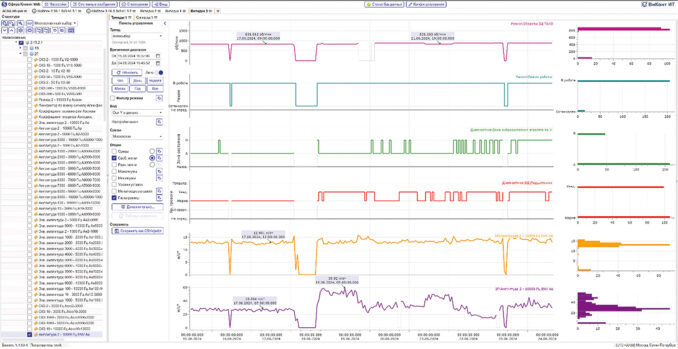
Служба вибродиагностики заказчика, эксплуатирующая систему, имела возможность с помощью штатных средств системы анализа данных (сигналов, спектров, трендов и др.) оперативно подтвердить автоматический диагноз системы, отслеживать его развитие и своевременно запланировать останов агрегата для плановой замены подшипника. Пример комбинированного представления приведён на рис. 4.
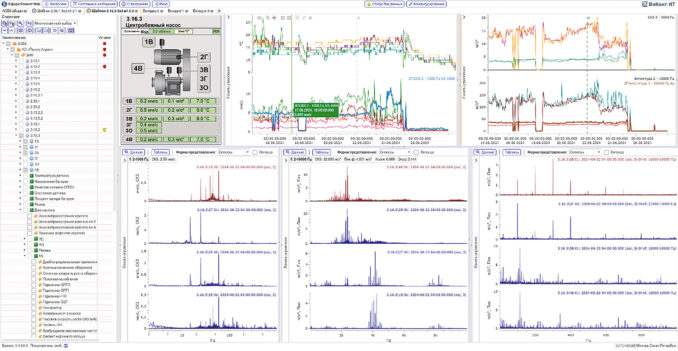
Таким образом, был выявлен развивающийся дефект, идентифицирован конкретный дефектный узел (подшипник качения), что позволило своевременно и эффективно спланировать ремонтные операции. Несвоевременное выявление такого дефекта гарантированно повлекло бы за собой необходимость внепланового ремонта, непланового переключения нагрузки на другие агрегаты технологической цепочки, которые также, в свою очередь, могли иметь дефекты, что в итоге, как правило, приводит к существенным издержкам в результате простоев.
Пример 2.
Выявление дефекта сборки агрегата на этапе пусконаладочных работ системы
Система установлена на паровую турбину мощностью 100 МВт.
В оснащении предусмотрены в том числе датчики вибрации вала (бесконтактные измерители мгновенного зазора). Они закрепляются на неподвижной части подшипника скольжения и измеряют зазор до вала агрегата. Устанавливаются по два датчика в одну плоскость, и с помощью специальной сложной обработки сигнала извлекается следующая информация:
1) средний зазор до вала — позволяет контролировать положение вала в расточке подшипника и траекторию всплытия вала;
2) орбита центра вала — позволяет контролировать нахождение вала в допустимой зоне с точки зрения геометрии подшипника, корректность работы масляного клина в подшипнике;
3) спектр виброперемещения, гармоники, амплитуды и фазы — совместный анализ с другими датчиками в этой же и других плоскостях позволяет выявлять целый ряд дефектов, таких как расцентровки, задевания, износ подшипников и другие (рис. 5, 6)
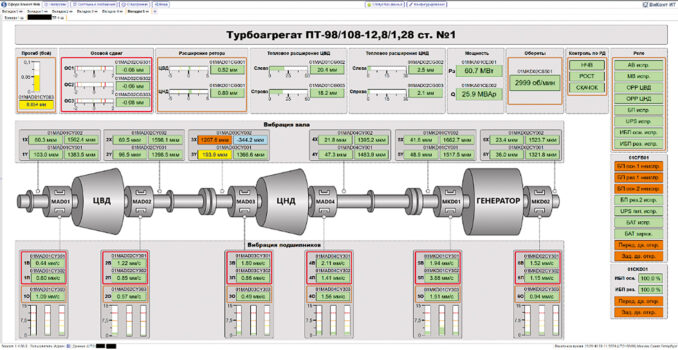
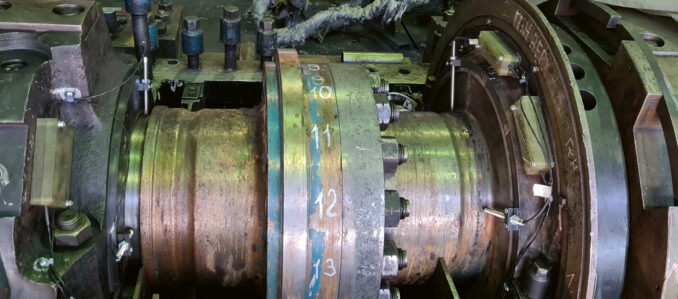
В ходе пусконаладочных работ специалистами резидента «Сколково» были установлены датчики вибрации вала в начальное положение с зазором 1 600 мкм до вала. На следующий день система просигнализировала о пониженном значении зазора на одном из подшипников.
Возможные причины: демонтаж и последующий некорректный монтаж датчиков ремонтной организацией, изменение зазора вследствие физического смещения деталей подшипника.
Тренд изменения зазора позволил однозначно установить время и характер изменения зазора, сопоставление времени с выполнявшимися в тот момент ремонтными операциями позволило выяснить, что производилась установка крышки картера подшипника, которой поджимается верхняя полусфера подшипника. В результате проверки установлено: при сборке подшипника крепёж его верхней части не был должным образом обтянут, в результате при установке крышки картера она прижала и физически сместила верхнюю часть подшипника в сторону вала, что и было зарегистрировано системой (см. рис. 7).
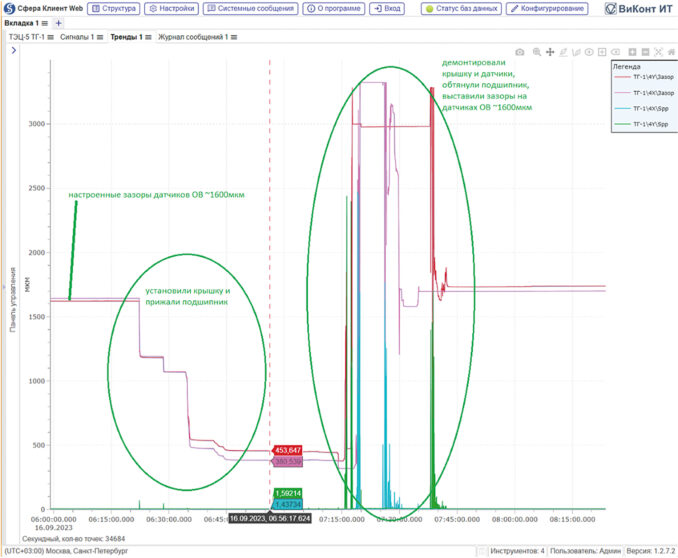
Данный дефект невозможно было выявить без установки системы. Пуск турбины с таким дефектом сборки гарантированно привёл бы к ненормативной работе подшипника и необходимости последующего внепланового останова по причине повышенной вибрации и/или температуры и к аварии с разрушением этого подшипника и повреждением других элементов турбины.
Данный случай является ярким примером того, как полноценное оснащение позволяет своевременно выявлять дефекты, понимать причины их возникновения и предотвращать аварии с первого же дня эксплуатации системы.
Пример № 3.
Выявление дефекта с неочевидной связью с режимом работы агрегата
Система установлена на паровую турбину мощностью 250 МВт.
В оснащении предусмотрен в том числе модуль автоматической диагностики со следующим набором детектируемых дефектов, их локализацией и степенью развития:
1) механический дисбаланс;
2) тепловой дисбаланс;
3) расцентровка роторов;
4) нарушения в опорной системе;
5) нарушения тепловых перемещений;
6) трещина в роторе;
7) задевания.
Системой был выявлен ряд дефектов различной степени развития. Обратим внимание на дисбаланс ротора нижнего давления — система указала на связь проявлений дисбаланса с повышенной разностью температур на выхлопе ЦНД. Система автоматически определила причины возникновения дефекта и дала рекомендации по минимизации разности температур на выхлопе ЦНД, после исполнения которых система перестала сигнализировать о дефекте. Таким образом удалось привести агрегат в надлежащее техническое состояние по данному параметру и обеспечить надёжную эксплуатацию.
На рис. 8 приведён пример трендов системы, которые позволяют подтвердить автоматически поставленный диагноз.
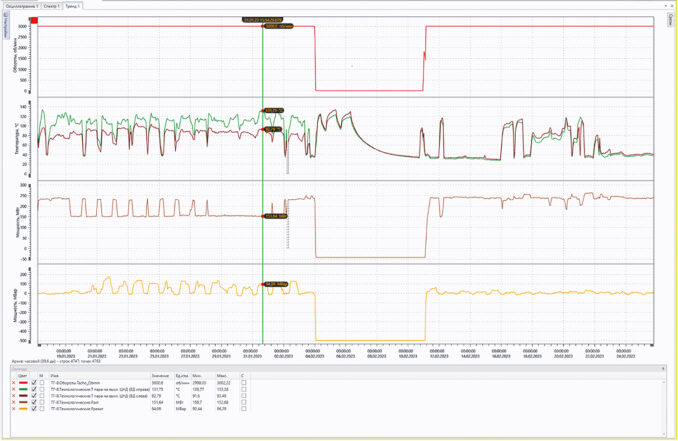
При плановом обходе не могли заметить данный дефект, так как он режимно зависимый.
Риски при эксплуатации с таким дефектом — повышение вибрации до ненормативной и ограничение на время эксплуатации, после чего пришлось бы разбираться в причине в «пожарном режиме» продолжительное время.
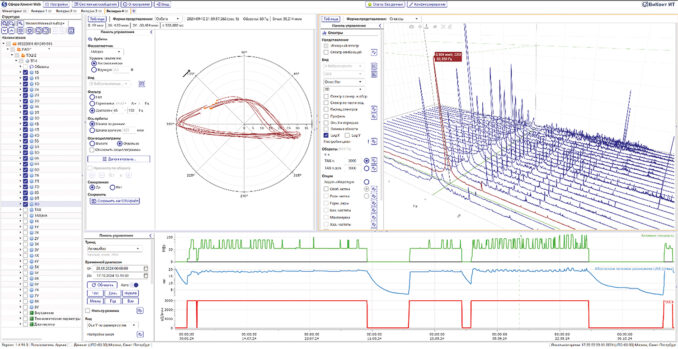
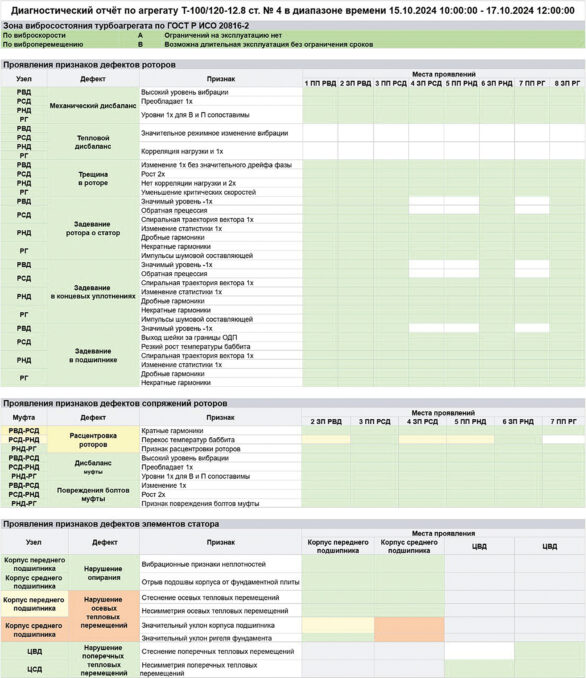
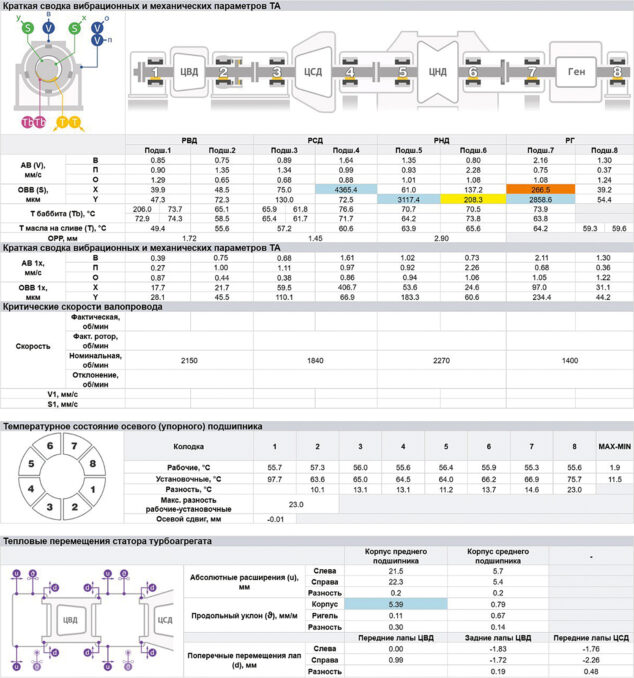
Вопросы можно задать здесь: mpolishuk@sk.ru