Анна Кислицына
В декабре 2024 года на Михайловском ГОКе им. А. В. Варичева компании «Металлоинвест» состоялся запуск второго дробильно-конвейерного комплекса (ДКК-2). Это стало завершением масштабного проекта по изменению транспортной схемы комбината и знаковым событием для всей отечественной горно-металлургической отрасли.
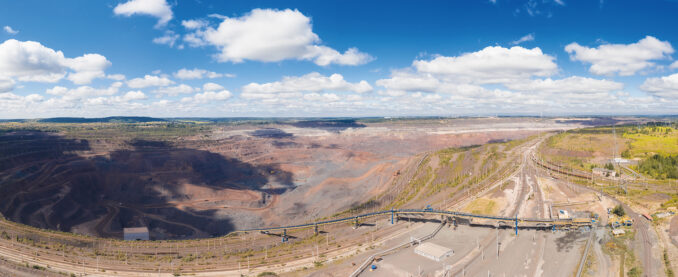
Предпосылки — индивидуальные особенности объекта на Михайловском ГОКе
Михайловский ГОК является одним из крупнейших в России и СНГ предприятий по добыче и обогащению железной руды. Месторождение здесь разрабатывается открытым способом. В начале 2000-х годов перед предприятием встал вопрос сохранения высоких объёмов добычи сырья. Для развития открытых горных работ в карьере комбината существовали определённые ограничения, обусловленные понижением горных работ при практически нулевой разноске бортов карьера. Западным бортом, в соответствии с проектными решениями, достигнуто положение выставления для долговременного стояния (более 50 лет), а к южному и восточному примыкали отвалы. Кроме этого, размещать горное оборудование внутри карьера было затруднительно — значительные территории занимала железнодорожная инфраструктура (перегоны, станции, перегрузочные пункты и др.). Основным направлением развития карьера оставалось северное. Данное направление, в связи с понижением кровли кристаллического фундамента, требовало увеличения объёмов удаления рыхлых вскрышных пород и их транспортировки в отвалы. Требовалось комплексное решение проблемы, которое позволяло отрабатывать северное направление и в то же время не увеличивать вскрышу за счёт отработки вскрытых руд внутри карьера, закрытых железнодорожной инфраструктурой.

Специалисты «Металлоинвеста» изучили мировой и отечественный опыт, чтобы найти вариант, который позволил бы и далее продолжать разработку карьера прежними темпами. Наиболее целесообразной и экономичной была признана циклично-поточная технология (ЦПТ), в составе которой ключевым звеном является дробильно-конвейерный комплекс (ДКК).
Ранее горная масса из карьера Михайловского ГОКа вывозилась автотранспортом с нижних горизонтов до перегрузочных пунктов, а далее железнодорожный транспорт вёз руду на обогатительные фабрики, а пустые породы — на отвалы. После строительства ДКК руда должна будет транспортироваться автотранспортом не на перегрузочные пункты, а к внутрикарьерным дробильным установкам. Затем дроблёная руда поднимается конвейерными линиями на поверхность, где складируется на промежуточный буферный склад, откуда отгружается экскаваторами в ж/д составы и также отправляется для дальнейшей переработки на обогатительную фабрику.
Такая технология обеспечивает поточность транспортировки руды, трасса будет значительно короче, чем маршрут железнодорожного транспорта, что также будет требовать меньше места и эксплуатационных затрат, чем цикличный ж/д транспорт.
Кроме того, в переработку вовлекаются дополнительные запасы руды с высоким содержанием железа, освобождённые от железнодорожной инфраструктуры.
Разработанный проект предусматривал строительство двух дробильно-конвейерных комплексов: на юго-восточном и северо-восточном участках карьера комбината. Шихтование рудной массы именно этих направлений позволяло обеспечить подачу на фабрику руды необходимого качества.
ДКК МГОК: нестандартные решения
Первый дробильно-конвейерный комплекс (ДКК-1) на юго-восточном борту карьера уникален для России и до сих пор не имеет аналогов по своей конфигурации: конвейер в составе комплекса — крутонаклонный, с углом в 37о. Высота подъёма при этом достигает 215 м, а длина — 700 м. Чтобы осуществлять перемещение сырья с таким углом наклона, потребовалось применение конвейера типа «сэндвич» с двумя лентами — грузонесущей и прижимной.
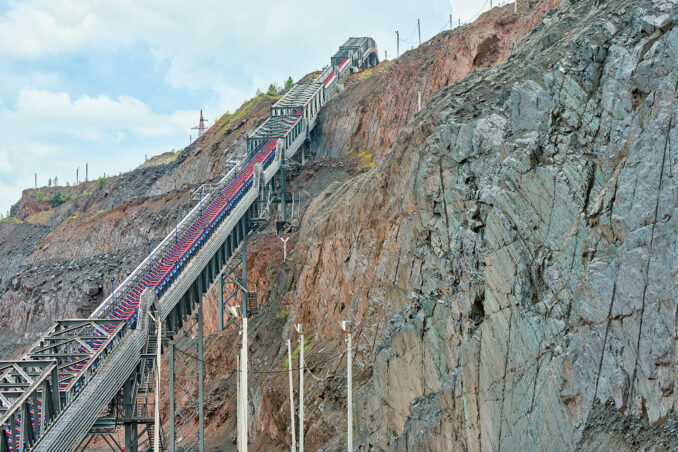
Всего в состав ДКК-1 вошли более 40 объектов. В их числе — дробильно-перегрузочная установка, бортовой крутонаклонный конвейер, промежуточный конвейер, погрузочно-складской комплекс, а также объекты инженерно-технического обеспечения. Суммарная производительность комплекса составила 15 млн тонн руды в год.
После запуска ДКК-1 в 2020 году началась активная фаза создания ДКК-2 на северо-восточном борту карьера. Уже в начале 2021 года начались проектно-изыскательские работы, а строительство стартовало осенью 2022 года. Для строительства комплекса потребовалась площадь более 158 га.
В отличие от ДКК-1, второй комплекс обладает более пологой траекторией: угол наклона на разных участках составляет от 4о до 13о. Протяжённость конвейера составила 2,4 км, а максимальная скорость ленты достигает 5,25 м/с.
Основное техоборудование для ДКК-2 было произведено на заводах ведущих отечественных машиностроительных предприятий, в т. ч. УЗТМ-КАРТЭКС (г. Екатеринбург). В состав комплекса вошли дробильно-перегрузочная установка (ДПУ), три перегрузочных узла и конвейерные эстакады, четыре ленточных конвейера, погрузочно-складской комплекс со штабелеукладчиком и рудным складом, ремонтно-механический участок и комплектная трансформаторная подстанция.
Использовались при создании комплекса и современные средства автоматизации. Так, в ДКК-2 используются электротехническое оборудование, средства связи и автоматизированная система управления технологическим процессом (АСУ ТП) от одного из отечественных разработчиков, ООО «Инжиниринг Технологии Системы». АСУ ТП отвечает за полную автоматизацию работы технологического оборудования, обеспечивает соблюдение последовательности технологического пуска и останова комплекса, выводит необходимую информацию на автоматизированное рабочее место операторов и диспетчеров, отвечает за сбор и хранение полученных данных.
Мощность ДКК-2 составила 35 млн тонн руды в год. Таким образом, после выхода комплекса на проектную мощность ежегодно по ДКК-1 и ДКК-2 будет подниматься на поверхность карьера до 50 млн тонн руды без использования ж/д транспорта.
Решение задач с помощью дробильно-конвейерного комплекса: производительность и экологичность
Реализация проекта позволила решить несколько приоритетных задач:
• увеличение производительности ж/д транспорта за счёт сокращения расстояния транспортирования, улучшения профиля движения, улучшения скоростного режима, увеличения скорости обмена и погрузки железнодорожного транспорта на погрузочно-складских комплексах (буферных складах) по сравнению с экскаваторными перегрузочными пунктами. Вследствие этого ожидается снижение количества локомотиво-составов, задействованных в транспортировке руды на обогатительную фабрику;
• снижение эксплуатационных затрат на железнодорожный транспорт за счёт сокращения затрат на ремонты и поддержание подвижного состава, железнодорожных путей в карьере; сокращения объёмов капитального строительства, которое было бы необходимо при развитии железнодорожной транспортной схемы для отработки нижних горизонтов карьера;
• высвобождение выемочного оборудования: ввод в эксплуатацию дробильно-конвейерных комплексов позволяет переориентировать работу экскаваторов, работавших на перегрузках неокисленных железистых кварцитов, на другие виды работ;
• вовлечение в отработку запасов руд высокого качества, освобождённых от размещённой на них части железнодорожной транспортной схемы, без производства дополнительных объёмов вскрышных работ;
• снижение нагрузки на стадию крупного дробления обогатительной фабрики за счёт подачи материала, уже прошедшего крупное дробление;
• снижение коэффициента вскрыши.
Таким образом, реализация этого инвестпроекта позволит сохранить текущие объёмы производства железорудного концентрата, при этом снизив его себестоимость — в том числе за счёт применения более энерго- и материалоэкономичной технологии, оптимизировать транспортную логистику в карьере ГОКа.
Отдельно стоит подчеркнуть, что снижение количества вовлекаемой в производственные процессы техники и сокращение объёмов образования и размещения отходов вскрыши повысили экологичность работ, обеспечили комплексное и бережное освоение месторождения.
Дробильно-конвейерный комплекс стал важным шагом для сохранения и укрепления лидирующих позиций компании «Металлоинвест». Эта технология считается одной из наиболее перспективных в индустрии с точки зрения наилучших доступных решений. Важно, что ключевое оборудование для комплекса произведено отечественными предприятиями.