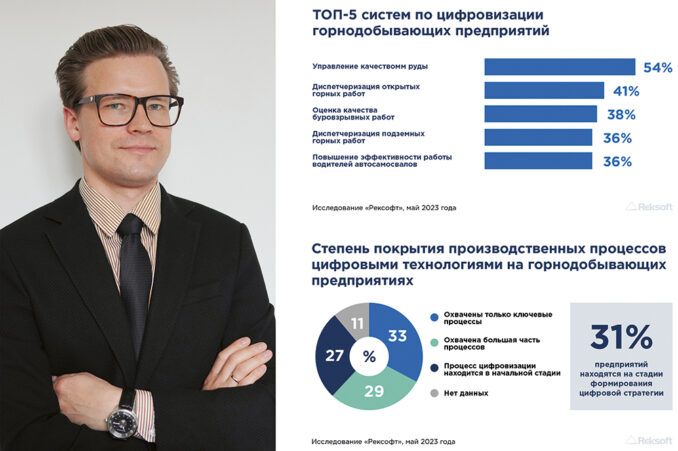
В середине мая 2023 года аналитики департамента горнодобывающих решений «Рексофт» представили результаты опроса о потребностях цифровизации российских предприятий, работающих в добывающей индустрии. В опросе приняли участие 138 руководителей ИТ и бизнес-подразделений предприятий отрасли.
Исследование выявило, что 59 % компаний горнодобывающей индустрии далеки от использования цифровых технологий в производстве: 26 % респондентов указали, что процессы цифровизации находятся в начальной стадии, а у 33 % на данный момент цифровизацией охвачены только ключевые процессы. Однако интерес к технологиям существенный: 31 % предприятий находится сейчас на стадии формирования своей цифровой стратегии.
Одной из целей исследования являлось определение областей, которые вызывают максимальный интерес предприятий с точки зрения цифровизации. В топ-5 запросов вошли:
• управление качеством руды (54 %);
• диспетчеризация открытых горных работ (41 %);
• оценка качества буровзрывных работ (38 %);
• диспетчеризация подземных горных работ (36 %);
• повышение эффективности работы водителей автосамосвалов (36 %).
«Мы видим комплексный запрос горнодобывающих предприятий на обновление как оборудования, так и автоматизированных систем управления. Это сегодня относится ко всем отраслям промышленности, не только к горной… Мы, как эксперты рынка, находимся в постоянном контакте с заказчиками и можем констатировать, что горнодобывающие предприятия подходят к задаче цифровизации комплексно и, одновременно с замещением ERP-систем и аппаратных решений, ведут работу по замене или внедрению с нуля и систем управления производственными процессами (MES). Результаты проведенного исследования подтвердили актуальность задач, по которым работает департамент горнодобывающих решений «Рексофт», и мы готовы предоставить свою экспертизу по всем категориям систем, вошедшим в топ-5», — прокомментировал итоги опроса Дмитрий Карамышев, директор департамента горнодобывающих решений компании «Рексофт».
Почему же именно эти решения сегодня вызывают наибольший интерес предприятий? Предлагаем вам последовательно рассмотреть аргументы для каждого из них.
Системы управления качеством руды
Этот запрос актуален в первую очередь для обогатительных фабрик. Буровзрывные работы не всегда могут обеспечить качественное измельчение горной породы, а это особенно важно для фабрики, поскольку стабильность химического состава полезного ископаемого и размера фракций позволяют обходиться без дополнительной перенастройки производственных мощностей и оборудования.
Системы управления качеством руды — это технологические системы, которые используются для контроля качества добычи и обогащения руды. Они обеспечивают мониторинг гранулометрического состава, контроль процессов дробления и измельчения, мониторинг химического состава и физических параметров руды в режиме реального времени. Для этого используются следующие технологии:
1) оптический анализ изображений высокого разрешения для измерений размеров и формы частиц руды (например, решение WipFrag от компании WipWare);
2) технология лазерной дифракции для анализа размера частиц руды в режиме реального времени (например, Particle Size Instrument от компании Malvern Panalytical);
3) рентгеновская флуоресцентная спектрометрия (XRF, РФА, РФС) для непрерывного и быстрого анализа химического состава руды на потоке (например, решение Courier от компании Metso Outotec);
4) автоматический отбор и подготовка проб для анализа.
Данные системы подразумевают контроль на всех этапах процесса обработки руды, включая питатели, конвейеры, дробилки, мельницы и т. д. Наблюдение за изменением размера частиц на каждом этапе позволяет в режиме реального времени анализировать данные, управлять параметрами работы дробильного и мельничного оборудования, генерировать отчеты для оперативного управления процессами и принятия решений.
Системы управления качеством руды являются ключевым инструментом для реализации концепции Mine to Mill (дословно — «от добычи до обработки»). Это интегрированный подход к оптимизации добычи и обработки руды, который основан на тесной взаимосвязи процессов и позволяет максимизировать экономическую эффективность и минимизировать затраты предприятия. В рамках этого подхода геологи, горные инженеры, металлурги и другие специалисты работают совместно, чтобы определить наиболее эффективный способ извлечения и обработки руды на каждом этапе процесса. Для оптимизации использования ресурсов и повышения прибыли учитываются различные факторы, такие как качество руды, геологические условия, экологические ограничения, параметры добычи и обогащения.
В качестве примера функциональных возможностей комплексных решений уровня Mine to Mill можно привести решение Pitram от компании Micromine:
1) управление данными: централизованное хранилище данных о геологии, добыче, обогащении и транспортировке руды, что обеспечивает полный контроль над информацией и возможность анализа;
2) отслеживание производительности: анализ производительности оборудования и персонала позволяет выявлять проблемы и определять возможности для улучшения процессов;
3) планирование и прогнозирование: предоставляет инструменты для планирования добычи и обработки руды, а также прогнозирования будущих показателей производства;
4) расчет и анализ ресурсов и резервов: позволяет проводить расчеты и анализ ресурсов и резервов месторождения на основе собранных данных, что помогает принимать обоснованные решения по разработке месторождений;
5) визуализация и мониторинг: предоставляет инструменты для визуализации и мониторинга процессов добычи и обработки руды, что позволяет оперативно реагировать на изменения в работе предприятия.
Таким образом, системы управления качеством руды играют важную роль не только в производственном цикле обогащения, но также имеют большое значение для реализации сквозного подхода к оптимизации процессов добычи и обработки руды как на этапе добычи, так и на обогатительной фабрике.
Диспетчеризация открытых и подземных горных работ
Интерес к системам этого класса вышел в топ опроса, что говорит о том, что далеко не все предприятия сегодня используют комплексные системы диспетчеризации. На многих предприятиях уже развернуты более доступные системы транспортного мониторинга, которые решают задачу геолокации техники и мониторинга уровня топлива. Однако системы этого уровня не позволяют решать такие задачи, как учет производственных показателей, расчет коэффициентов использования оборудования и других показателей эффективности производства. Для этого необходимо внедрение специализированных систем диспетчеризации и управления горнотранспортным комплексом, которые обеспечивают глубокую цифровизацию актива за счет сбора и анализа большого объема данных. Функционал системы может включать учет количества рейсов самосвалов, простоев оборудования, количества рабочих циклов экскаватора, объема перевезенной горной массы, автоматическую выдачу производственных заданий, составление рейтинга водителей с элементами соревнований, сквозной учет топлива на предприятии, и пр.
Таким образом, система диспетчеризации обладает широким функционалом и является специализированным инструментом контроля за процессами горного предприятия от мониторинга состояния ресурсов до бизнес-показателей эффективности.
Оценка качества буровзрывных работ
На многих горных предприятиях для работ по разрушению твердой породы привлекаются специализированные подрядные организации, поэтому заказчику нужен инструмент для оценки качества выполнения этих работ.
Основная цель буровзрывных работ — эффективное разрушение горной породы с минимальными затратами и минимальным негативным воздействием на окружающую среду. Для достижения этой цели важно правильно спроектировать план по обуриванию участка и выполнять взрывные работы с учетом геологических, технических и экологических факторов. Качество буровзрывных работ напрямую влияет на производительность и экономичность дальнейшего процесса добычи и обработки руды.
Как и любые сервисные услуги, данный тип работ предполагает проведение оценки и приемки качества, которые могут проводиться с использованием современных технологий.
Фрагментация породы является одним из ключевых показателей качества буровзрывных работ. Измерение размера образующихся обломков (гранулометрия) после взрыва и их распределение позволяют оценить качество разрушения породы. Оценку размера гранул после взрывных работ можно проводить на месте взрыва с помощью носимого планшета с камерой или с помощью установленной над дорогой камеры, которая оценивает гранулометрический состав руды в кузове проезжающих под ней самосвалов. Также камера может быть установлена на рукояти экскаватора или на погрузчике. В этом случае оценка гранул выполняется при их попадании в ковш. Результаты измерений гранулометрического состава сразу поступают на диспетчерский пункт для принятия оперативных решений.
Повышение эффективности работы водителей автосамосвалов
Многие респонденты высказали заинтересованность в цифровых технологиях, которые помогли бы водителям самосвалов эффективнее выполнять свою работу. Один из ключевых показателей эффективности — это коэффициент использования оборудования (КИО). И здесь предприятиям доступно множество технических решений и систем.
Функция автоматического определения простоя и возможность ввода причин простоя техники (обеденный перерыв, поломка, очередь на погрузку и пр.) позволяют диспетчеру оценить, насколько эффективно используется оборудование.
Еще один класс систем, которые сегодня вызывают активный интерес предприятий, — системы бережного отношения к технике. Это комплекс технологий и инструментов, направленных на снижение износа, поломок и преждевременного выхода из строя оборудования. Внедрение этих систем также способствует оптимизации эксплуатационных характеристик и снижению затрат на обслуживание и ремонт. Вот некоторые примеры таких систем:
1. Системы контроля состояния шин. Эти системы отслеживают давление и температуру в шинах, предупреждая о возможных проблемах и своевременно сигнализируя о необходимости замены или ремонта.
2. Советчик водителю. Системы анализа стиля вождения предоставляют водителю обратную связь, направленную на снижение необходимости резких маневров и оптимизацию расхода топлива.
3. Системы предиктивной диагностики и прогнозирования состояния оборудования позволяют отслеживать состояние силовой установки в режиме реального времени и заранее предсказать возможный выход оборудования из строя и запланировать его превентивное обслуживание или замену узла. Для этого собираются данные о состоянии масла и фильтров, а также диагностические данные блоков управления.
Использование систем бережного отношения к технике позволяет сократить эксплуатационные затраты, избежать нештатных ситуаций и внеплановых выходов оборудования из строя, продлить срок службы техники.
Оценка эффективности внедрения цифровых инструментов
Цифровизация запускает процесс повышения эффективности бизнеса. Вопрос подсчета потенциального экономического эффекта от цифровой трансформации на предприятиях горнодобывающей отрасли непростой. Это связано с тем, что ни одно из отечественных предприятий на сегодняшний день не прошло этот путь полностью. По имеющимся оценкам, цифровизация позволяет получить сокращение общих затрат на 10–15 %. Рост производительности карьеров в результате внедрения цифровых технологий может составить 5–15 % производительности обогатительных фабрик до 20 %, а производительности персонала — до 50 %. При этом среднетехническая скорость может вырасти на 8–12 %.
Внедрение цифровых инструментов — это длительный и ресурсоемкий процесс, который тем не менее позволяет добиться значительного эффекта. И важным этапом этого процесса является разработка методики оценки получаемых результатов, которая учитывает индивидуальные особенности предприятия.
Необходимо также добавить, что ключевыми факторами успеха при реализации проектов цифровизации являются комплексный подход к оценке планируемых результатов, наличие поддержки на уровне первых лиц предприятий, информирование сотрудников о целях цифровых проектов и обучение персонала, а также организация дальнейшей поддержки и развития цифровых систем.