Анна Кислицына, фото Николая Николаева
Михеевский горно-обогатительный комбинат (входит в структуру Русской медной компании) — предприятие, где нашли воплощение самые передовые методы и технологии, применяемые в добыче и обогащении меди. В ходе технотура по производству, состоявшегося 8 декабря 2021 года, сотрудники ГОКа продемонстрировали редакции нашего журнала все возможности современных технических решений: от систем автоматизации и применения машинного зрения и до внедрения двухтопливной системы.
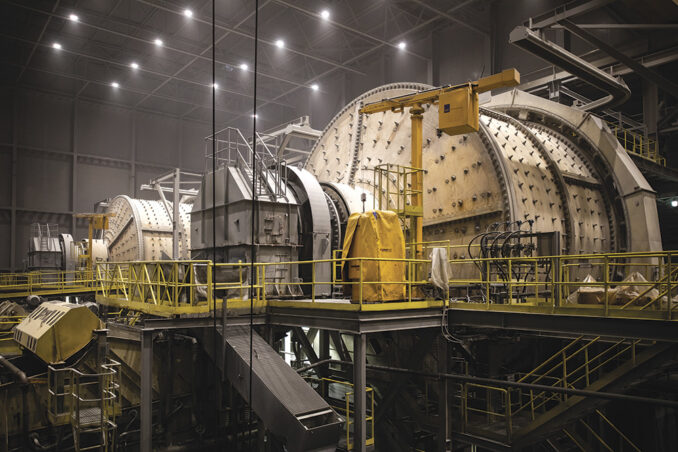
Работа на перспективу
Михеевский ГОК входит в число самых молодых предприятий страны — его строительство пришлось на 2011–2014 годы. Проектные решения предусматривали применение передовых и наиболее эффективных на тот момент технологий, учитывающих особенности разрабатываемого Михеевского месторождения, руды которого отличаются низким содержанием меди (средний показатель — 0,36 %). Для создания рентабельного производства было необходимо четко выстроить техпроцессы, снизить всевозможные потери и простои и, конечно, обеспечить максимальный уровень извлечения.
Со всеми этими задачами ГОК справился на ура. «Первая тонна концентрата была выпущена 18 февраля 2014 года в 13 часов 30 минут — это время зафиксировано на доске в моем кабинете, — вспоминает Александр Сизиков, генеральный директор предприятия. — Могу с уверенностью сказать, что к настоящему времени мы не просто полностью окупили затраты на создание производства, но и работаем с прибылью».
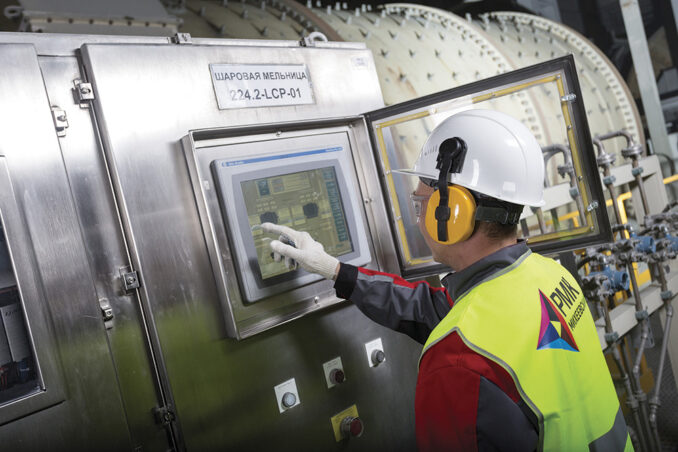
Но выход на прибыль был не единственной задачей ГОКа: за первые восемь лет работы предприятием были вложены значительные средства в поисковые и геолого-разведочные работы. Начинание увенчалось успехом: в пределах 10 км от ГОКа удалось обнаружить два крупных рудных тела (Западная залежь и Новониколаевский участок), после исследования которых сырьевая база предприятия возросла на 60 % — теперь общие запасы меди насчитывают 880 млн т. Для разработки данных месторождений потребуется строительство новых карьеров, но в технологической цепочке обогащения перемен не предвидится — руда на исследованных участках идентична добываемой на Михеевском месторождении. «Сейчас комбинат обеспечен сырьем на 30–40 лет вперед, — рассказывает Александр Васильевич. — Но останавливаться на этом мы не станем: сейчас зона поиска новых рудных тел расширилась до 100 км, и наращивание минерально-сырьевой базы продолжается».
Новый этап геолого-разведочных работ намечен, в частности, на Аятской площади: в минувшем году там был проведен сбор и анализ данных, а также подготовлена заявка для получения лицензии на пользование недрами.
В приоритете — безопасность здоровья и жизни
От беседы с Александром Васильевичем о карьерах будущего технотур привел к карьеру настоящему — благо, со счетов его списывать рано: к сегодняшнему дню глубина добычи составляет всего 220 м от запланированных 540. Здесь начинает свой путь медь, и начинается он с оптимизации: предприятие ведет обязательный мониторинг буровзрывных работ (далее — БВР), на основании данных которого осуществляется анализ применения взрывчатых веществ. Сами БВР осуществляются в строгом соответствии с нормами безопасности: проводится оповещение персонала диспетчером, территория оцепляется, задействуются светозвуковые сигналы.
Безопасность при осуществлении работ карьера в принципе поставлена на первое место: чтобы свести на нет вероятность аварий и несчастных случаев, карьерная техника, задействованная в транспортировке руды, оснащена системами автоматического пожаротушения, а также системами видеомониторинга, позволяющими предупреждать столкновения и осуществлять контроль в слепых зонах. На вспомогательной технике карьера (бульдозеры, автогрейдеры, погрузчики) установлена также система мониторинга основных показателей — результаты наблюдения при помощи ГЛОНАСС отображаются на рабочем месте диспетчера производственно-технического отдела.
Осваивая передовой опыт
Не остается без внимания и экологическая безопасность. Ради ее обеспечения Михеевский ГОК последние восемь месяцев трудится над воплощением одного из самых амбициозных проектов — переводом карьерной техники на двухтопливную систему «дизельное топливо/сжиженный природный газ». Заместитель генерального директора по производству Александр Ивлев рассказал, что за это время предприятию удалось перевести на новую систему уже 12 самосвалов Komatsu 730Е. С июня и до ноября проводилось переоборудование машин, осуществлялась наладка устанавливаемых систем. В ноябре состоялся запуск машин в тестовом режиме.
«Уже по первым неделям мы видим, какое значение этот проект имеет для экологии, — объясняет Александр Владимирович. — Благодаря переводу на двухтопливную систему нам удалось сократить выбросы СО2 и серы». Стоит отметить, что этого удалось достичь при замещении всего 30 % дизеля на СПГ, но это не окончательный результат: в 2022 году ГОК планирует повысить долю использования газа до 40 %.
Об особенностях перевода техники на СПГ в подробностях рассказал Юрий Шестов, начальник цеха ремонта и технического обслуживания. Так, он отметил, что в ходе работ по переоборудованию самосвалов необходимо было провести наладку трех систем управления: STATEX (управление генерацией), VCHNS (управление двигателем) и GFS (управление непосредственно газовой системой). «Это было похоже на составление техпроцесса, — признается Юрий Николаевич. — Все эти системы представляют собой отдельные «цеха» большого «завода» — самосвала. Нашей задачей было связать эти «цеха» в единую цепочку. Пока у нас все получилось, дальше предстоит наращивать процент замещения дизельного топлива газом».
Определение момента перехода с газа на дизель и обратно система осуществляет в автоматическом режиме, без участия оператора самосвала, в зависимости от доступности СПГ. Как правило, на дизельное топливо система переходит уже при исчерпании газа. Стоит отметить, что в системе GFS предусмотрены средства безопасности, отслеживающие герметичность элементов и их целостность. В случае разгерметизации система моментально блокируется, а в кабину оператора поступает специальный сигнал о наличии проблемы в системе. Также на самосвал была установлена дополнительная защита от пробоев.
«Важно, что нам не потребовалось изменять систему техобслуживания техники — трудозатраты не возросли, — делится Юрий Николаевич. — Хотя потребовалось тщательно подобрать масло: сейчас испытываем марку Total в тестовом режиме». Выбор масла был сделан исходя из расчета максимальной наработки — сейчас этот показатель составляет 350 часов против стандартных 250, предусмотренных техобслуживанием.
Проект по переводу техники на двухтопливную систему еще получит свое развитие: согласно планам предприятия, в 2022 году, кроме самосвалов, модернизации подвергнутся два экскаватора Komatsu РС4000D и три фронтальных погрузчика KomatsuWA900.
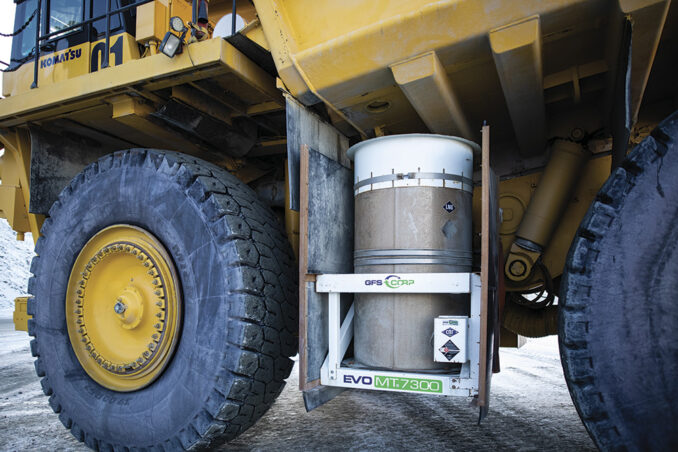
На страже чистой природы
Как и на любом другом предприятии РМК, минимизация вреда для окружающей среды в процессе производства входит в число главных задач ГОКа. Вопросам экологического контроля и реализации природоохранных мероприятий уделяется особое внимание — ответственность за организацию и мониторинг данных направлений возложена на отдел охраны окружающей среды.
В соответствии с программой производственного контроля специалисты отдела:
• контролируют обустройство и содержание в подразделениях предприятия и подрядных организациях мест временного накопления отходов;
• осуществляют контроль соблюдения установленных нормативов выбросов в атмосферу;
• проводят контроль качества атмосферного воздуха на границе санитарно-защитной зоны предприятия и в жилой зоне;
• проводят мониторинг качества поверхностных и подземных водных объектов, а также контролируют состояние почвенного покрова.
Анализ результатов замеров воздуха, воды и почвы осуществляется в аккредитованных лабораториях.
На предприятии организована система оборотного водоснабжения, а также оборудованы очистные сооружения хозяйственно-бытовых сточных вод и их повторное использование в технологическом процессе.
Для предотвращения загрязнения водных объектов организован сбор карьерного водоотлива, поверхностных вод для дальнейшего использования в замкнутом цикле водооборота обогатительной фабрики (далее — ОФ), позволяющем не осуществлять сброс сточных вод в природные водные объекты.
Для снижения выбросов в атмосферу используются аспирационные системы, а также импортное высокоэффективное и экологичное горное и транспортное оборудование, оснащенное системами дожигания топлива и очистки выхлопных газов. Кроме того, проводится орошение внутрикарьерных дорог и отвалов.
Большое значение в уменьшении количества выбросов играет обустройство мест дробления: все склады, места перегрузки сырья и участки дробления оборудованы укрытиями. А транспортировка руды на ОФ от гирационной дробилки Metso SUPERIOR MK 60-89, самой большой в России, осуществляется при помощи крытого рудного конвейера общей длиной более 1,5 км.
ГОК будущего
Обогатительная фабрика Михеевского ГОКа по праву считается одной из самых технологичных, современных и автоматизированных в России. Еще во время ее проектирования был применен ряд решений, позволивших воплотить инновации, которые даже сейчас, восемь лет спустя, доступны немногим производствам горнодобывающего сектора. В состав оборудования измельчения фабрики входят 10 мельниц (НПСИ, шаровые, доизмельчения и пр.). В их числе — уникальная мельница Isa Mill M10000, мельница тонкого измельчения. Она позволяет максимально раскрыть сростки минералов с пустой породой и позволяет достигать измельчения до 20 мкм. В отделении флотации установлены флотоблоки объемом 300 и 100 кубометров.
Главный секрет ОФ — автоматизация и цифровизация процессов измельчения и обогащения. Автоматизированная система управления технологическими процессами (далее — АСУТП) фабрики построена на базе оборудования PROSCON фирмы Outotec и включает в себя средства отбора, передачи, обработки и представления информации и управления, включая программируемые логические контроллеры и промышленные персональные компьютеры, обеспечивающие управление технологическим объектом по заданным критериям в соответствии с заложенными в систему алгоритмами.
Главная цель АСУТП — обеспечение высокоэффективной переработки руды и достижения максимально возможного извлечения металлов в концентраты. «К настоящему моменту мы достигли показателя извлечения на уровне 85 %, — объясняет Евгений Шукшин, начальник ОФ. — Для нашего объема производства это отличный показатель. Но надо понимать, что все мы здесь нацелены на повышение извлечения, на минимизацию потерь, и все наше оборудование представляет собой высокоэффективное средство по достижению этой задачи».
АСУТП задействована во всех операциях, производимых на фабрике. Ее функции, управляющие (задействованные в процессах выбора режимов и параметров оборудования) и информационные (осуществляющие централизованный контроль за состоянием объектов управления), позволяют выполнять следующие задачи:
• измерение технологических параметров, сбор информации о состоянии технологического процесса, оборудования и устройств управления;
• первичная обработка информации;
• вычисление средних и интегральных значений технологических параметров;
• расчет технологических показателей;
• непосредственное цифровое регулирование технологических параметров;
• оперативное отображение и регистрация состояния объекта управления;
• пуск и остановка оборудования.
Благодаря высокой степени автоматизации для осуществления мониторинга и управления техпроцессами ГОКу достаточно двух диспетчеров: один контролирует процессы измельчения, второй — процессы обогащения. Все параметры в онлайн-режиме выводятся на автоматизированные рабочие места, оснащенные комплексными мониторами. В случае отклонения от заданных характеристик диспетчер получает уведомление системы и при помощи телефонной и/или радиосвязи может связаться с операторами оборудования непосредственно на переделах и уточнить ситуацию.
Для получения оперативной информации все оборудование оснащено датчиками — начиная от ленточного конвейера, по которому руда поступает на фабрику: там установлены датчики схода ленты, датчики вращения, датчики прорыва и пр. «Мы минимизируем простои, — рассказывает Евгений Николаевич. — За все эти годы остановки оборудования были только плановые: на проведение ППР у нас отводится 72 часа».
Автоматизация коснулась и процессов контроля качества руды в ходе обогащения — на ОФ действует система оперативного аналитического контроля на базе анализаторов «Курьер 6iSL». Система проводит спектральный анализ следующих продуктов:
• исходная руда (слив г/ц II стадии измельчения);
• объединенный концентрат основной и контрольной флотации;
• хвосты контрольной флотации;
• слив гидроциклонов доизмельчения 1 (питание первой перечистки);
• хвосты контрольной перечистной флотации;
• концентрат второй перечистной флотации;
• коллективный концентрат (концентрат третьей перечистной флотации);
• хвосты обогащения;
• медный концентрат.
Осуществление анализа при помощи «Курьера» занимает от двух до трех минут. Для сравнения: подобные операции, выполненные в ручном режиме, обычно проводятся в течение нескольких часов.
Также на базе анализаторов PSI 300 и PSI 500 действует система анализа грансостава. Анализатор PSI 300 измеряет крупность частиц пульпы в диапазоне 25–600 мкм, PSI 500 — в диапазоне 1–500 мкм. Кроме того, на ОФ используется химический навигатор Chena, при помощи специальных электродов проводящий измерение потенциала в режиме онлайн.
Еще один передовой способ контроля, активно используемый фабрикой в ходе флотации, — машинное зрение. При помощи системы FrothMaster проводится анализ поверхности пены в реальном времени. Данный инструмент позволяет определять основные параметры пены, такие как скорость, размер пузырьков, стабильность и цвет. В состав системы анализа пены входят блоки формирования изображений пенного слоя, монтируемые над флотационными машинами. Один блок состоит из цветной камеры высокой резолюции, регулируемой подсветки и дополнительной светозащитной бленды и имеет класс защиты IP65. Блоки формирования изображений подключены к АСУТП с помощью протокола ОРС посредством системной шины через интеллектуальные коробки.
Нет предела совершенству!
Несмотря на то что ОФ оснащена по последнему слову техники, предприятие все равно находит возможности для улучшений. Так, три года назад к двум основным производственным линиям фабрики был добавлен вспомогательный производственный корпус (далее — ВПК), где осуществляется третья стадия извлечения. «Запуск ВПК позволил нам нарастить показатель извлечения почти на 10 %, — вспоминает Евгений Шукшин. — А ведь это и есть наша главная задача. Все сотрудники трудятся именно ради повышения эффективности извлечения — и трудятся слаженно, как одно целое».
Усилия коллектива не пропадают зря: содержание меди в выпускаемом ГОКом концентрате достигает 25 %. Учитывая ее исходное содержание в рудах Михеевского месторождения, данный показатель вызывает уважение. Точно так же вызывает его и сам Михеевский ГОК — своими продуманными техническими решениями, стремлением развиваться и внедрять лучший мировой опыт и никогда, никогда не останавливаться на достигнутом.
Воистину — ГОК будущего.