Авторы: Кочнев В.Г., к.т.н., директор ООО «ТТД», Грушинская О.В., заместитель директора
На основе полупромышленных испытаний различных золотосодержащих руд, проведённых на непрерывном стенде компании «Техника и Технология Дезинтеграции» (ТТД), была разработана промышленная технология обогащения кварцевой карьерной руды с производительностью 400 т/час. Оптимальная крупность руды, поступающей на фабрику, составляла 900 мм (единичные куски 1200 мм) со средним содержанием мелкого золота 1,8 г/т. На рис.1 представлена блок-схема технологии, где показано, что первичное дробление-измельчение производиться в мельнице самоизмельчения [1], разработанной и изготавливаемой в компании ТТД, рис.2.
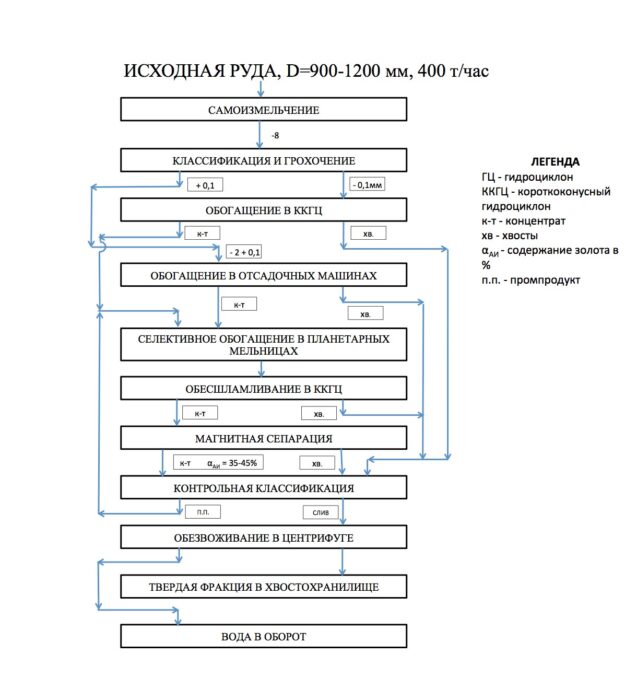
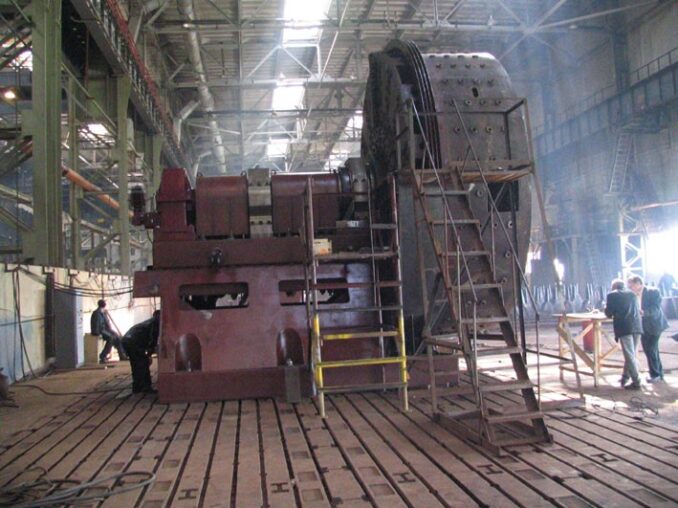
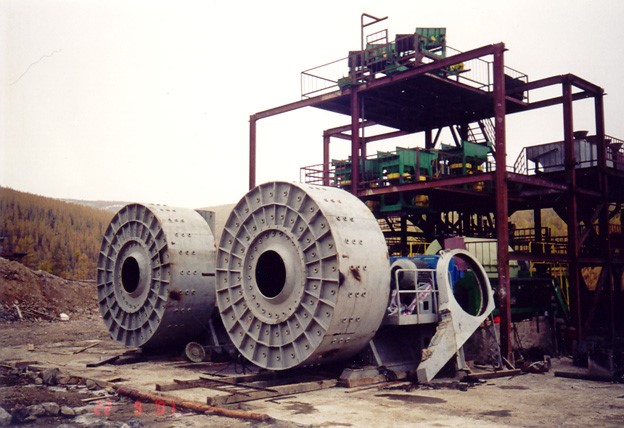
Предлагаемая мельница существенно отличается от существующих на рынке подобных мельниц, выпускаемых зарубежными и отечественными изготовителями, следующими параметрами: — отсутствие венцовой и ведущей шестерён; — использование подшипников качения вместо подшипников скольжения, работающих на консистентной смазке, соответственно отсутствие маслостанции; — мельницы не требуют массивных бетонных, как для традиционных, фундаментов, так как имеют свою несущую раму; — мельницы имеют массу на 30-35 % меньше традиционных и меньшую на 50-55% занимаемую площадь, что способствует наиболее быстрой доставке даже на отдалённое от цивилизации место и быстрому монтажу; — мельница обеспечена футеровкой и решёткой нашей же разработки, что обеспечивает повышенную производительность и более низкие энергозатраты (иногда в два раза); — конструкция мельницы позволяет загружать карьерный кусок крупностью 900-1200 мм; — конструкция мельницы позволяет изготавливать мельницы диаметром до 20 м, при сохранении важного соотношения D:L; — при соответствующем подборе решётки в нашей мельнице можно получить готовый продукт до 70 % класса -74 мкм, в этом случае одна мельница заменяет дробилку крупного дробления или несколько дробилок с учётом тенденции подачи в мельницы полусамоизмельчения куска до 150 мм, а также и шаровую мельницу; — для нашей мельницы разработана технология предварительного дробления критического класса крупности (-60 мм), что позволяет на некоторых рудах получить снижение энергозатрат практически в два раза; — в нашу мельницу не добавляются шары, как это делается для мельниц полусамоизмельчения, которые более ускоренными темпами выводят из строя футеровку, способствуют неоправданному увеличению энергозатрат.
Вернёмся к нашей технологии. Разгрузка мельницы самоизмельчения представляет собой пульпу с разжижением 0,5 и крупностью менее 8 мм, в которой содержание класса -74 мкм составляет 55-60%. Пульпа поступает в зумпф с насосом, и далее в классифицирующий гидроциклон (ГЦ), где идёт разделение по 100 мкм. Пески ГЦ поступают на грохот с резонирующими ситами с ячейкой 2 мм, надрешётный продукт грохота направляется в циркуляцию в мельницу самоизмельчения, а подрешётный -2 мм на отсадочные машины.
В нашей схеме отсадочные машины работают по технологии «обратной отсадки», что позволяет гарантированно извлекать золото крупностью + 30 мкм с извлечением 92-96%. Эта технология отработана нами не только на золоте, но и на алмазах крупностью -0,5+0,2 мм на геологической фабрике, на разведке месторождений алмазов в Архангельской области. Надо сказать, что на действующих фабриках этот класс вообще не извлекался отсадкой, а только пенной сепарацией. В нашем же случае мы получили извлечение этого сложного класса на уровне 96-98% при выходе концентрата 0,2% и с представительностью по кристаллам несколько тысяч. Протоколы переработки валовых геологических проб массой более тысячи тонн сохранились [2].
Последующие испытания технологии «обратной отсадки» были применены на золотосодержащих рудах – первые данные, полученные нами на крупных (более пяти тонн) пробах, подтвердили уникальность и результативность технологии.
Огромное спасибо разработчику проф. МИСИС Александру Григорьевичу Лопатину, к сожалению уже ушедшему от нас.
Ещё одно чрезвычайно важное достоинство описанной технологии – это возможность сохранения параметров работы отсадки без вмешательства оператора.
Несмотря на высокую степень извлечение отсадкой, часть мелкого золота средней крупности 18-25 мкм попадает в хвосты, которые дополнительно отправляются на обогащение в короткоконусные гидроциклоны, где это золото и извлекается. Иногда, при отсутствии в руде тонкого золота хвосты отсадки сразу же отправляются в хвостохранилище, поскольку они не содержат золота. Такова специфика работы технологии «обратной отсадки». На диаграммах, представленных на рис.4, хорошо видно, как и какую крупность извлекает отсадка, а какую — извлекают короткоконусные гидроциклоны. Также хорошо видно, что практически все золото до 20 мкм извлечено [3].
Этими двумя процессами поскольку золота крупнее 20 мкм в хвостах- единицы по сравнению с извлечёнными на отсадке и, особенно, в гидроциклонах. Достоверность графиков подтверждается, во-первых Гаусовским распределением золотин, во-вторых их представительным количеством – всего при анализе участвовало более 10 тысяч зёрен.
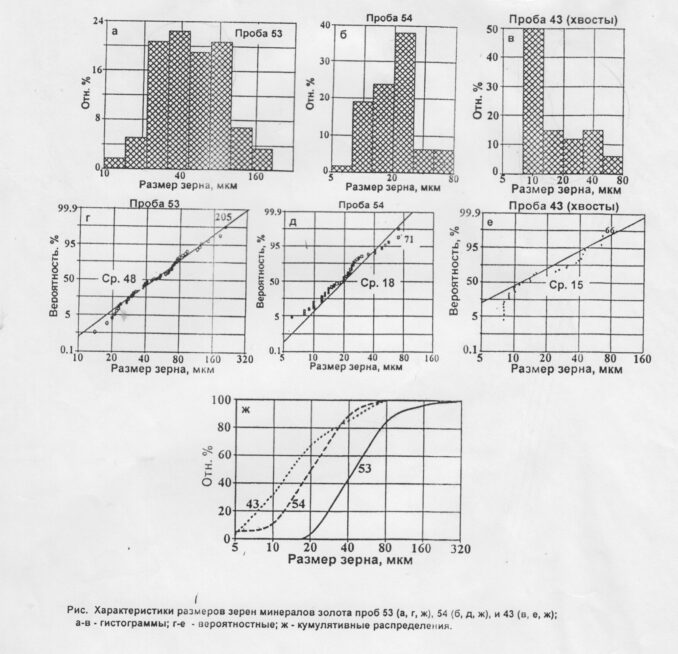
Доводка гравитационного концентрата (отсадки и ККГЦ) осуществляется на основе селективного метода с использованием планетарных мельниц нашей конструкции.
Метод селективного измельчения (обогащения) испытывается в компании ТТД более 18 лет – сначала он применялся для доводки концентратов, полученных на пилотной установке, затем при переработке керновых проб и наконец – на исходном сырье. Наиболее интересные испытания были проведены на валовой пробе с содержанием золота 1,7 г/т месторождения «НАТАЛКА». Испытания были проведены в непрерывном режиме с планетарной мельницей МП-0. При достижении эффективности измельчения 99,9 % класса менее 40 мкм был получен концентрат 460 г/т и хвосты – 0,15 г/т. Последующая доводка концентрата, также с помощью планетарной мельницы позволила получить продукт с содержанием золота 42 %, причём в классе +100 мкм – 92 % [4].
Вернёмся к нашей технологии. Концентраты, указанные выше, содержат 600-800 г/т золота. Это практически традиционные для нас содержания, полученные при первичном обогащении, что резко отличает их от существующих технологий, где содержания характеризуются цифрами 30-90 г/т.
Последующая доводка концентратов с использованием планетарных мельниц и мокрых магнитных сепараторов обеспечивает нам содержание в конечном продукте 35-45 % золота, что позволяет такой продукт сдавать на аффинаж, минуя плавку.
Для получения полусухих отвальных хвостов и оборотной воды в технологии используется осадительная центрифуга. Этот класс оборудования широко применяется в мире для различных нужд, однако для обезвоживания хвостов применяется редко. Нами была проведена большая работа по полупромышленным испытаниям текущих хвостов на одной из действующей алмазодобывающей фабрике. Проблема возникла ещё при геологической разведке, когда оседание твёрдых частиц в хвостохранилище происходила крайне медленно – один см/мес. Тоже самое было и на промышленном ГОКе. Какие-либо решения, связанные с использованием реагентов, помогало весьма слабо, да и ГОК находится в зоне нерестилища ценных пород рыб, в том числе и сёмги. Длительная эксплуатация полупромышленной установки с центрифугой, смонтированной нами на пляже хвостохранилища, наглядно показало реальную возможность получения полусухих хвостов и оборотной воды.
Таким образом, описание технологии обогащения на фабрике производительностью 400 т/час практически завершено, осталось лишь в краткой форме оценить ее преимущество перед существующими и проектируемыми схемами.
Таблица 1 – Технико-экономические показатели фабрики
Производительность, т/час | 400,00 |
Установленная мощность, кВт | 6 400,00 |
Расход эл.энергии, кВт-ч/т | 16,00 |
Содержание золота в руде, г/т | 1,80 |
Получено золота в час, г | 720,00 |
Количество часов работы в год | 8 000,00 |
Получено золота в год, г | 5 760 000,00 |
Получено золота в год при извлечении 98%, г | 5 644 800,00 |
Стоимость 1 г, $. | 57,90 |
Доход в год, $ | 326 833 920,00 |
Капитальные затраты, $ | 6 720 070,00 |
Эксплуатационные затраты, $/год, в.т.ч.: | 4 927 330,00 |
— стоимость энергозатрат, $ | 3 413 330,00 |
— затраты на содержание обслуживающего персонала (26 чел) | 924 000,00 |
— затраты на запасные части и расходные материалы | 590 000,00 |
ИТОГО затраты по фабрике, $/год | 11 647 400,00 |
Себестоимость по фабрике, $/г | 2,1 |
Себестоимость по фабрике, $/унция | 65,3 |
Основные преимущества технологии:
1. Высокое стабильное извлечение золота до крупности 20 мкм;
2. Отсутствие каких-либо реагентов, в том числе цианидов;
3. Высокое содержание золота в конечном концентрате (35-45 %) обусловлено, прежде всего, весьма эффективной технологией доводки, что позволяет получать и сдавать на аффинаж порошковый богатый материал, минуя дорогостоящую плавку;
4. Низкие капитальные и эксплуатационные затраты, следовательно низкая себестоимость получения одного грамма золота (при содержании золота в исходной руде 1,0-2,0 г/т себестоимость одного грамма составляет 2,0–3,0 долл., при содержании 3 г/т – 1,8-2.0 долл.), недосягаемая в современных технологических решениях, даже там где применяется полное цианирование;
5. На фабрике отсутствуют тяжёлые бетонные фундаменты, все оборудование, даже тяжёлое типа ММС, имеют свои несущие рамы, поэтому и монтаж фабрики не занимает более одного месяца;
6. Хвостохранилище не имеет ограждающих дорогих дамб. Хвосты складируются практически в обезвоженном состоянии и могут быть использованы для строительных работ;
7. Фабрика принимает с карьера крупный кусок 900 мм, единичные куски 1200 мм, что позволяет обходиться без предварительного дробления и относительно дёшево вести буровзрывные работы без оглядки на негабариты;
8. На фабрике отсутствуют шары крупнее 12 мм. Действующие фабрики используют шары крупностью 70-150 мм, как расходный материал на фабрике, колоссальным образом влияющий на повышение себестоимости конечной продукции. В нашей же технологии используются шары крупностью 2-12 мм, изготовленные из стали ШХ15, в основном как мелющие тела для планетарных мельниц и как пастель для отсадочных машин;
9. Технология обладает дополнительным потенциалом по снижению энергозатрат приблизительно в два раза (здесь не показано) за счет внедрения преддодрабливания критического класса крупности (-60 мм) из исходной руды и замены металлических шаров в цикле измельчения на керамические;
10. Технология позволяет извлекать с помощью селективного измельчения (обогащения) золото крупностью 5-10 мкм, даже из упорных руд;
11. Технология после несложных преобразований может работать в сухом варианте также эффективно, как и в мокром.
Литература:
- Кочнев В.Г. «Новые барабанные мельницы консольного типа» журнал «Золотодобывающая промышленность» №6, 2004 г.;
- Кочнев В.Г. «Минимизация капитальных и эксплуатационных затрат» журнал «Золотодобывающая промышленность» №5, 2004 г.;
- Баранов В.Ф. «Обзор мировых достижений и проектов рудоподготовки новейших зарубежных фабрик» журнал «Обогащение руд» № 1, 2008 г.;
- Кочнев В.Г. «Мельницы для тонкого и сверхтонкого помола» инфорационно-рекламный бюллетень «Золотодобыча» №88, 2006 г.
тел. 8 (812) 930-87-11