Мамонов С. В.1, 2, Дресвянкина Т. П.1, Зиятдинов С. В.1, Ершов А. А.2
1 ОАО «Уралмеханобр», 2 негосударственное частное образовательное учреждение высшего образования «Технический университет УГМК»
Уральские медно-цинковые руды являются в основном колчеданными, в которых содержание сульфидных минералов, и в первую очередь пирита, может доходить до 90 % и более [1]. Эти руды сильно различаются по минеральному составу, характеру вкрапленности ценных минералов, содержанию меди, цинка и серы и их соотношению.
Медно-цинковые руды одного из колчеданных месторождений Урала можно охарактеризовать как труднообогатимые. Руды характеризуются сложным минеральным составом, повышенным содержанием вторичных медных минералов и наличием флотационно-активного цинка и пирита.
Разработкой и совершенствованием технологии обогащения медно-цинковой руды колчеданного месторождения Урала занимались ведущие исследовательские центры страны. Исследовательскими организациями были предложены различные подходы к реализации технологической схемы обогащения и получены прогнозные показатели обогащения. Однако анализ работы фабрики показывает, что по разработанным технологическим и реагентным режимам наблюдаются потери меди и цинка с отвальными хвостами и разноименными концентратами.
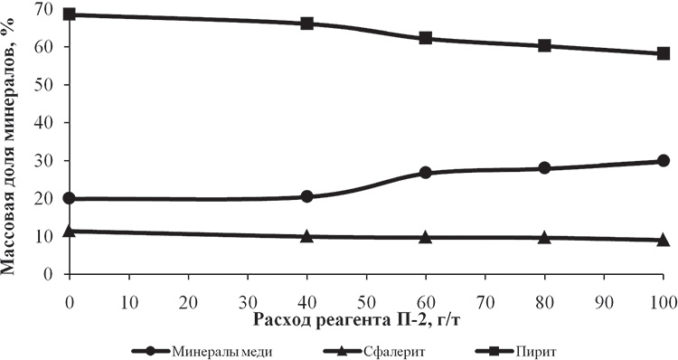
Решение вопроса по повышению технологических показателей обогащения, совершенствованию и оптимизации технологии обогащения медно-цинковой руды колчеданного месторождения Урала является актуальным.
Среди перспективных направлений переработки медно-цинковых руд, обеспечивающих повышение технологических показателей, можно рассматривать применение новых флотационных реагентов для увеличения извлечения металлов в концентраты и повышения эффективности депрессии активного цинка и пирита.
Проведены флотационные исследования по влиянию подачи реагента-депрессора пирита — реагента П-2 на технологические показатели обогащения медно-цинковой руды. Реагент П-2 испытывали в медном цикле флотации с подачей в операцию агитации перед селекцией коллективного медно-цинкового концентрата.
Флотационные исследования проведены при снижении расходов цинкового купороса и гидросульфида натрия на 50 % и при вариации расхода П-2 от 40 до 100 г/т исходной руды.
Медный продукт исследовался оптико-геометрическим и рентгеноструктурным методами анализа с целью определения колебания массовой доли пирита, халькопирита и сфалерита в нем от расхода реагента П-2. Результаты приведены на рисунке 1.
Результаты исследований показали, что при подаче реагента П-2 в операцию агитации коллективного концентрата перед селективной флотацией наблюдается депрессия пирита. Отмечено, что при увеличении расхода реагента П-2 от 0 до 100 г/т массовая доля пирита в медном продукте снижается с 68 до 57 % при одновременном увеличении массовой доли медных минералов с 19 до 29 %. Это, в свою очередь, приводит к увеличению массовой доли меди в медном продукте с 6,9 % (без П-2) до 10,3 % (П-2 — 100 г/т). Аналогичная картина наблюдается и для сфалерита: массовая доля цинковой обманки в медном продукте снижается при увеличении расхода реагента П-2, но незначительно — с 11 до 9 %. При этом потери цинка с медным циклом снижаются с 41,2 % (без П-2) до 23,0 % (П-2 — 100 г/т). При расходе реагента П-2, равном 100 г/т исходной руды, наблюдается депрессия также и медных минералов. При этом уровень извлечения медных минералов в медный цикл снижается с 85,70 % до 83,36 %.
Извлечение меди остается на одном уровне (85,27–85,56 %) при расходах П-2, равных 40–80 г/т исходной руды.
Таким образом, результаты исследований подтвердили, что реагент П-2 является депрессором пирита и в некоторой степени депрессирует и цинковые минералы. Оптимальным можно считать расход П-2, равный 80 г/т исходной руды, при котором уровень извлечения меди не меняется, а потери цинковых минералов с медным циклом флотации снижаются на 17 % (по сравнению с опытом без П-2).
Исследовано влияние реагента-депрессора цинковых минералов — полиметиленнафталинсульфоната (ПМНС) серии 2И. Реагент испытан в цикле селекции коллективного концентрата. Для более полной оценки влияния реагента ПМНС-2И на флотацию медных и цинковых минералов были снижены расходы депрессоров цинковых минералов — цинкового купороса и гидросульфида натрия — на 50 %. Расходы реагента ПМНС-2И варьировали от 0 до 60 г/т исходной руды. Результаты исследований приведены на рисунке 2.
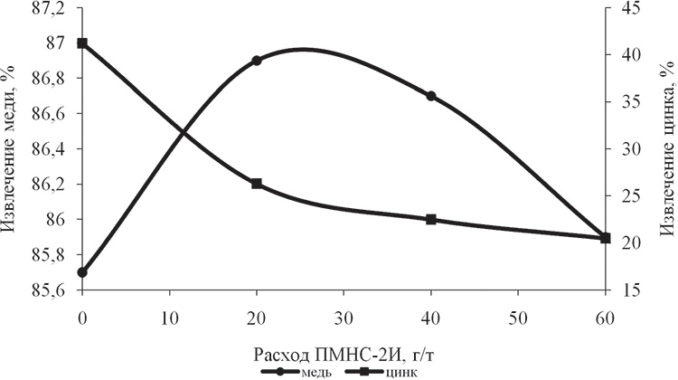
Результаты исследований показали: подача реагента ПМНС-2И в операцию агитации коллективного концентрата перед селективной флотацией усиливает депрессию сфалерита. Отмечено, что увеличение расхода реагента ПМНС-2И с 0 до 60 г/т позволяет снизить выход пенного продукта медного цикла на 7,3 % (с 19,3 до 11 %) при повышении содержания меди в нем на 4,2 % (с 6,9 до 11,1 %) и снижении содержания цинка на 1,5 % (с 7,6 до 6,1 %). При этом потери цинка с медным циклом снижаются на 20,7 % (с 41,2 до 20,5 %). Извлечение меди в медный цикл имеет экстремальный характер с максимумом в точке, соответствующей извлечению 86,9 % при расходе реагента ПМНС-2И 20 г/т. При увеличении расхода реагента ПМНС-2И до 60 г/т извлечение меди уменьшается незначительно по сравнению с расходом, равным 20 г/т.
Таким образом, подача реагента ПМНС-2И в количестве 60 г/т исходной руды в операцию агитации коллективного концентрата перед селективной флотацией позволяет снизить расход традиционных депрессоров цинковых минералов — цинкового купороса и гидросульфида натрия — на 50 % и снизить потери цинковых минералов при сохранении уровня извлечения медных минералов в медный цикл флотации.
Разработанные технологические решения по применению новых флотационных реагентов проверены в контрольных флотационных опытах, выполненных по принципу непрерывного технологического процесса. Сводные результаты приведены в таблице 1.
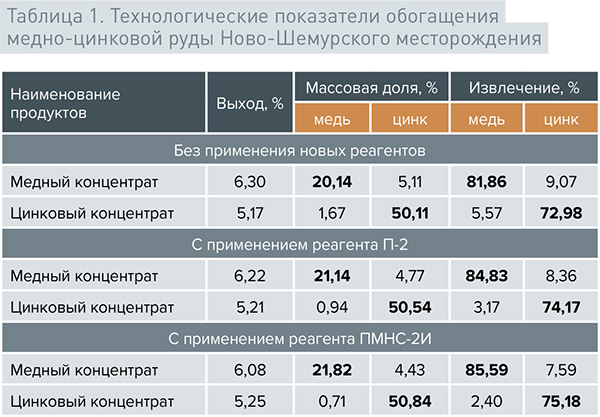
В результате проведенных контрольных флотационных опытов по принципу непрерывного процесса отмечено, что применение реагента П-2 позволяет повысить извлечение меди в медный концентрат на 2,97 % (с 81,86 до 84,83 %) при одновременном повышении качества медного концентрата на 1 %, а также повысить извлечение цинка в цинковый концентрат на 1,19 % (с 72,98 до 74,17 %) при повышении его качества на 0,43 %.
Аналогичная картина наблюдается и при подаче реагента ПМНС-2И. Применение этого реагента позволяет повысить извлечение меди в медный концентрат на 3,73 % (с 81,86 до 85,59 %) при одновременном повышении качества медного концентрата на 1,68 %, а также повысить извлечение цинка в цинковый концентрат на 2,2 % (с 72,98 до 75,18 %) при повышении его качества на 0,73 %.
Одним из перспективных направлений по достижению максимальной тонины помола сырья, для которого характерна тонкая и эмульсионная вкрапленность ценных минералов друг в друга и вмещающие породы, является ультратонкое бисерное измельчение.
Исследования влияния ультратонкого измельчения на технологические показатели обогащения проведены на пробе питания разделительной флотации (цикл селекции коллективного концентрата) медно-цинковой руды Ново-Шемурского месторождения, содержащей 6,86 % меди, 7,85 % цинка и 41,1 % серы.
В ходе исследований была изучена кинетика измельчения исследуемой пробы в шаровой (МШЛ-7) и в бисерной (KD-VGM2) мельницах с определением раскрытия сульфидных минералов в процессе измельчения.
Результаты исследований шарового измельчения, приведенные на рисунке 3, показали, что даже при измельчении исследуемой пробы до крупности 90 % класса -0,071 мм (20–25 % класса -0,02 мм) содержание раскрытых зерен халькопирита составляет 67 %, вторичных медных минералов — 40 %, сфалерита — 66 %.
Приемлемое раскрытие ценных минералов (85–95 % раскрытых зерен) наблюдается при содержании класса крупности 0,02 мм на уровне 75 %, что достигается только при ультратонком измельчении пробы в бисерной мельнице. Полное раскрытие сульфидов меди и цинка наблюдается только при измельчении исследуемой пробы в бисерной мельнице до крупности 92–97 % класса -0,02 мм.
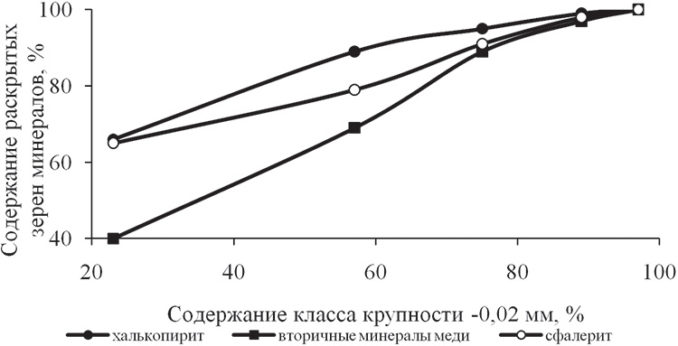
На исходной пробе питания разделительной флотации и продукте ее измельчения в бисерной мельнице до крупности 75 % класса 0,02 мм проведены флотационные исследования с получением грубых медного и цинкового концентратов. Исследования проведены по схеме, предусматривающей проведение основной и контрольной медных флотаций с получением грубого медного концентрата; проведение основной и контрольной цинковых флотаций на хвостах медного цикла с предварительной активацией цинковых минералов медным купоросом с получением грубого цинкового концентрата и хвостов цинковой флотации (направляются в дальнейшем в отвал). При проведении флотационных опытов реагентный режим принят постоянным. Результаты приведены в таблице 2.
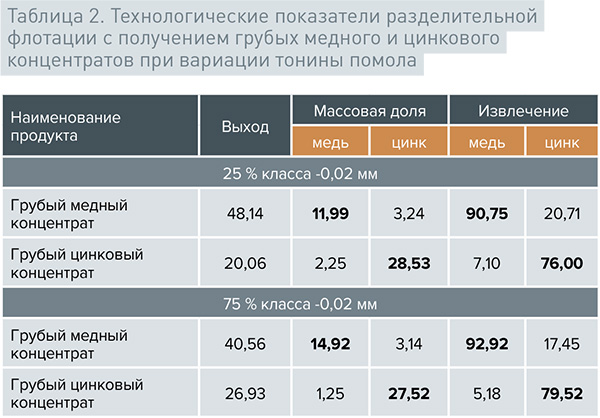
По результатам исследований установлено, что с увеличением в питании разделительной флотации содержания класса -0,02 мм с 25 до 75 % наблюдается повышение извлечения меди в грубый медный концентрат на 2,17 % при одновременном повышении качества грубого медного концентрата на 2,93 %. При этом извлечение цинка в грубый цинковый концентрат также повышается на 3,52 %, с 76 до 79,52 %, при сохранении качества грубого цинкового концентрата. Потери цинка с грубым медным концентратом снижаются на 3,26 %.
На рассматриваемом колчеданном месторождении Урала кроме медно-цинковой разности руд выделяют и медноколчеданные руды с содержанием цинка менее 0,8–1,0 % [2]. Отечественная нормативная документация разрешает из данного сорта руд не получать цинковые концентраты.
По нашему мнению, такое содержание цинка в рудах не является обоснованием неполучения цинковых концентратов. Сортность руд должна определяться технологическими возможностями и экономической целесообразностью получения медных и цинковых концентратов из «медных руд».
В ОАО «Уралмеханобр» проведены исследования по получению медных и цинковых концентратов из медного сорта руды медно-цинкового колчеданного месторождения Урала.
Объектами исследований явились технологическая проба медно-цинковой руды (МЦР) и три технологические пробы медной руды (МР, МР-1, МР-2).
Согласно результатам количественного химического анализа, в медно-цинковой руде содержится 2,21 % меди и 3,23 % цинка; в медных рудах содержится 1,91–2,53 % меди и 0,35–1,04 % цинка.
Исследования по получению медных и цинковых концентратов из медно-цинковой и медных руд проведены по коллективно-селективной схеме флотации с применением следующих реагентов: бутиловый ксантогенат калия, пенообразователь оксаль Т-92, цинковый купорос, гидросульфид натрия, медный купорос, известь.
В результате исследований получены (таблица 3):
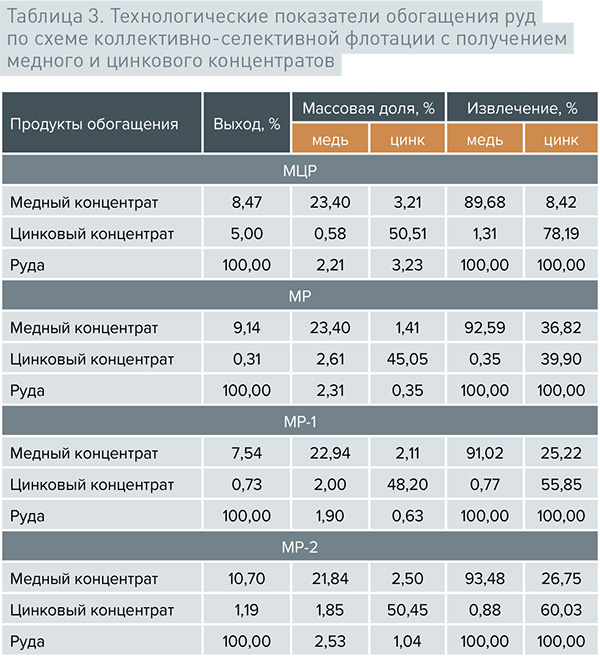
— из пробы медно-цинковой руды МЦР, содержащей 2,21 % меди, 3,23 % цинка, получен медный концентрат с массовой долей меди 23,40 % при извлечении меди 89,68 % и цинковый концентрат с массовой долей цинка 50,51 % при извлечении цинка 78,19 %;
— из пробы медной руды МР с массовой долей меди 2,31 %, цинка 0,35 % — медный концентрат с массовой долей меди 23,40 % при извлечении меди 92,59 %, цинковый концентрат с массовой долей цинка 45,05 % при извлечении цинка 39,90 %;
— из пробы медной руды МР-1 с массовой долей меди 1,90 %, цинка 0,63 % — медный концентрат с массовой долей меди 22,94 % при извлечении 91,02 %, цинковый концентрат с массовой долей цинка 48,20 % при извлечении цинка 55,85 %;
— из пробы медной руды МР-2 с массовой долей меди 2,53 %, цинка 1,04 % — медный концентрат с массовой долей меди 21,84 % при извлечении 93,48 %, цинковый концентрат с массовой долей цинка 50,45 % при извлечении цинка 60,03 %.
Исследования проведены также и на смеси медных и медно-цинковой руд при разном их соотношении. Графическая интерпретация результатов исследований приведена на рисунке 4.
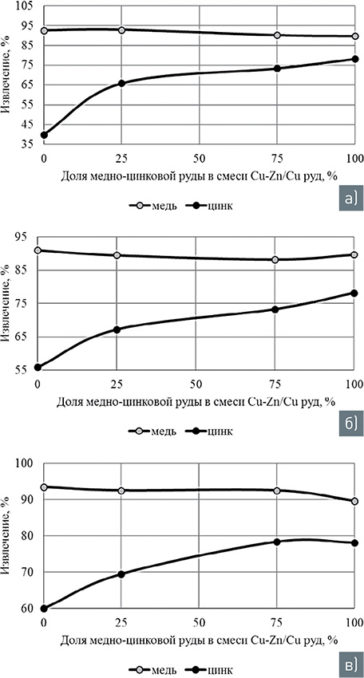
Результаты исследований показали, что:
— из смеси медной руды МР и медно-цинковой руды МЦР возможно получить медный концентрат с массовой долей меди 23–24 % при извлечении меди 90–92 % и цинковый концентрат с массовой долей цинка 50 % при извлечении цинка 65–73 %;
— из смеси медной руды МР-1 и медно-цинковой руды МЦР возможно получить медный концентрат с массовой долей меди 23 % при извлечении меди 88–89 % и цинковый концентрат с массовой долей цинка 50 % при извлечении цинка 67–73 %;
— из смеси медной руды МР-2 и медно-цинковой руды МЦР возможно получить медный концентрат с массовой долей меди 23 % при извлечении меди 92 % и цинковый концентрат с массовой долей цинка 50 % при извлечении цинка 69–78 %.
По результатам исследований выполнена укрупненная экономическая оценка целесообразности получения медного и цинкового концентратов из медных руд и смеси медных и медно-цинковых руд.
Результаты экономических расчетов показали, что переработка медных и медно-цинковых руд с получением медного и цинкового концентратов экономически выгоднее переработки медных руд с получением только медного концентрата и медно-цинковых руд с получением медного и цинкового концентратов. Прирост валовой прибыли в зависимости от пробы руды варьирует от 8,8 до 217,09 млн руб.
Показано, что переработка медных и медно-цинковых руд в смеси с получением медного и цинкового концентратов экономически целесообразна (рисунок 5):
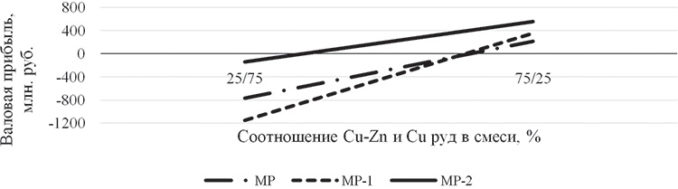
— при соотношении в смеси МЦР к МР-2 свыше 35:65;
— при соотношении в смеси МЦР к МР-1 свыше 65:35;
— при соотношении в смеси МЦР к МР свыше 65:35.
При этом прирост валовой прибыли в зависимости от содержания металлов в руде варьирует от 217,36 до 555,75 млн руб.
Заключение
Применение новых флотационных реагентов отечественного производства — реагента П-2 и реа-гента ПМНС марки 2И позволяет повысить технологические показатели обогащения медно-цинковой руды колчеданного месторождения Урала и снизить расходы депрессоров цинковых минералов в селективном цикле флотации на 50 %.
Ультратонкое бисерное измельчение позволяет увеличить тонину помола руд и достичь требуемого раскрытия сростков сульфидных минералов друг с другом и вмещающими породами по сравнению с традиционным измельчением сырья в шаровых мельницах.
Увеличение тонины помола руды и, как следствие, повышение уровня раскрытия ценных минералов при ультратонком измельчении позволяет увеличить извлечение меди и цинка в одноименные концентраты при одновременном повышении их качества.
Целесообразность получения медных и цинковых концентратов при переработке медных колчеданных руд, содержащих менее 0,8–1,0 % цинка, должна быть обоснована с технологической и экономической точек зрения.
На примере конкретного колчеданного месторождения показано, что из медных руд с содержанием цинка 0,35–1,0 % и меди 1,9–2,5 % получение медного и цинкового концентратов технически возможно и экономически эффективно.
Валовая переработка медных и медно-цинковых руд должна обосновываться экономическими расчетами с определением оптимального соотношения руд в шихте.
Список литературы
1. Технология обогащения медных и медно-цинковых руд Урала / под общ. ред. акад. РАН В. А. Чантурия и докт. техн. наук И. В. Шадруновой; Ин-т проблем комплекс. освоения недр РАН. — М.: Наука, 2016. — 387 с.
2. Методические рекомендации по применению Классификации запасов месторождений и прогнозных ресурсов твердых полезных ископаемых. Медные руды, утвержденные распоряжением Министерства природных ресурсов Российской Федерации от 05.06.2007 г. № 37-р.